Chapter 6: Making Your Own Tools

The great thing about having a blacksmith forge is that you can make your own tools or refurbish old tools very inexpensively. Historically, journeymen blacksmiths had to make their own tools before setting off on their own and making tools for everyone else. The tools in this chapter will get you started forging and will help out around the house and farm.
MAKING YOUR FORGE TOOLS
Your first project should be a set of fire-maintenance tools because without proper fire maintenance, you will be forever inefficient as a blacksmith—dirty fires will prevent you from forge-welding, clinker will rob your fire’s heat, and you will burn more fuel than you need to as the fire constantly grows more inefficient and larger. Forging a poker, rake, shovel, ladle, and coal scoop or scuttle will help you work on tapering, rounding, dishing, and riveting.
Making a Match
The Ubiquitous S-Hook

1. Begin by tapering one end of a 1⁄4-inch round rod over the far edge of the anvil until the taper is approximately 3⁄4 inch long. Cut off the rod at 51⁄2 inches and repeat tapering the other end. 2. Scroll the ends of the taper by beginning to bend the tip over the far edge of the anvil and then rolling it back as shown. 3. Quench the scroll in water to protect it and then bend each of the ends around the horn of your anvil or a 3⁄4-inch-diameter rod. If you are making multiples, a rod will make them more consistent. 4. Finish the bend by hammering straight down to straighten the tip of the bend and create a deeper hook.
Fire Poker
Starting Stock
- 3/8-inch rod, 2 ½–3 feet long
Tools Required
This is the easiest project in this book other than the S-hook; you need to simply taper and round one end of a rod and then make the handle. Don’t let the simplicity of this project fool you, though: a poker is an important tool, especially if you use coal, because the fire will settle and block your air supply. Every so often, it is good to lift and break the coal up with your poker to let more air into the fire. The poker will also let you lift any clinker out of the fire and blow the ash out of the way.

- Begin by tapering one end of the rod over the far side of the anvil until the taper is 5 inches long. I always taper over the far side of the anvil, if I can, to protect the anvil face from the edge of my hammer. As you can see in the photo, one corner of the hammer would hit the anvil face before I hit the rod near the tip of the taper. This leads to dings in your anvil face as well as marring the smoothness of your finished pieces because those dings will be pressed into the metal you are forging. The only way to achieve a perfectly smooth forged finish is with smooth hammer and anvil faces.

- Once you have a 5-inch-long gentle taper, proceed to round the taper, remembering to go from square to octagon to round as previously described and as shown here. Hold the adjacent corners perpendicular to the anvil face and hammer straight down. If you don’t follow the proper steps, you will end up chasing a corner around, forming cracks near the tip.

- On the handle end, square up ¾ of an inch. Once it is square, bend it 90 degrees over the far side of the anvil.

- Approximate your hand width, with an extra inch for comfort plus 2½ inches for the bend, from the end. In my case, the total length was 7 inches, and I have average-sized hands. Mark that length on the anvil and, once the rod is heated, line the end of the rod up with the chalk mark. Next, lift the end up and start bending the rod on the edge of the anvil. Once you have your mark, bend it over a round object, such as an anvil horn or a piece of pipe or rod in the vise. Just make sure that when you bend the handle around, you bend it so that the tab you bent over at the end bends around to touch the shaft of the poker. If you do end up bending it the wrong way, simply twist the tab so it is correct, and no one will know the difference.

Close the handle over the anvil face. As you do this, a bend will form in the bottom of the handle, as you will see in the final piece.
Congratulations! You’ve finished your first blacksmithing project, and now you can say that you’re a blacksmith!
Fire Rake
Starting Stock
- 3/8-inch rod, 2–3 feet long
Tools Required

- With full-face hammer blows, flatten 5 inches of the rod down to ⅛ of an inch thick on the face of the anvil, as shown. Keep your hammer and rod parallel to the anvil face and allow the metal to spread wide; this will become the rake that you will use to move coal in and out of your fire. If you need more width, remember that you can use a fuller to move the metal in one direction. In this case, to make the piece wider, you need the curve of the fuller to be perpendicular to the length of the rod. This pinches the metal side to side rather than lengthwise, much like you would use your fingers to spread clay. In other words, your peen needs to be parallel to the length of the rod.

- You want to end up with a shape similar to that shown in the photo of the rake’s end. Offset the widening by placing the metal on edge across the hammer face and hammering it at the point where the metal widens and anywhere else where it is not lying flat on the anvil. Of course, success relies on a straight anvil face, so you should double-check the straightness of the rake with a straightedge or ruler.

- Bend the rod 90 degrees over the far side of the anvil, just before the flattened portion, with shearing hammer blows. Square up the bend on the anvil corner as shown.

- To add strength to the bend you just made, taper the outside of the corner. This widens the corner and puts more metal in line with the direction in which the corner will want to straighten, thus strengthening it. You don’t need to do this, but it will help keep your rake from straightening with use. Taper the corner to ⅛ inch at the far edge to prevent damaging your anvil.

- For the rake handle, we’re going to use a simple wrapped taper eye to distinguish it from the other forge tools. Taper and round the end, following the recommended procedures in the poker project, so that you have 5 inches of rounded taper.

- Bend the start of the taper slightly further than 45 degrees over the far edge of the anvil and then bend the tail back around the horn or rod until it looks like this image. The interior diameter of the ring should be ¾ of an inch.

- Using your tongs or a pair of pliers, wrap the tail around the shaft of the rake as shown. Make sure that you tuck the tail in tight to prevent cutting yourself on the sharp tip.

- This time, let’s add a twist! To twist round metal, you need to first square the rod; you can then twist it by clamping the rake in the vise where you want the twist to start. Because you made a round handle, simply heat only the section you want twisted, put a rod through the handle, and twist while pulling straight (see next paragraph). If you heat a larger section than you would like, quench the unwanted part.
Because this is your first twist, don’t worry too much about the length of the twist; just concentrate on keeping the twist straight and even. A trick to keeping a twist straight is to pull straight backward consistently while you turn. This will help keep you from bending the rod while twisting it. Use a wooden mallet to straighten the twist.

Tell Them Apart

Fire Shovel
Starting Stock
- Handle: ½-inch rebar rod, 17 inches long
- Shovel: 18-gauge sheet metal, 3 inches x 4 inches
- Rivets: ¼ inch rod, at least 3 inches long
Tools Required
- Cross-peen
- Hammer
- Anvil
- Method of “dishing” sheet metal (e.g., swage or wood stump)
- Method of cutting sheet metal (angle grinder with cutting disc, cold chisel, hacksaw, bandsaw, oxy/acetylene torch, plasma cutter)
- Hot cut or chisel
- Punch
- Vise
- Drill and ¼-inch metal drill bit
There are a few different ways that you can make a shovel. In this project, you will cut the shovel out of a piece of sheet metal and rivet it to the handle. Because I like to salvage to both reduce my costs and help the environment, for this project I used an old rusted-out garden spade, but you can use any similar thin-gauge metal. I wouldn’t go any thicker than ⅛ of an inch for weight, though.


- Cut out the shovel blank, 3 x 4 inches rectangular, and round the corners with a grinder or file. In a V-swage, use your cross-peen to dish the shovel, as shown. Using a cupped dishing tool or a block of wood and a ball-peen, dish one end of the shovel into a cup.

- The shovel blank should look like this when it is finished and ready for the rivet holes.

- Over the near side of the anvil, flatten the end of the rebar and let it spread as much as possible. Use your cross-peen to spread the metal wider, if needed; you want the metal to be wide enough to keep the shovel from twisting once riveted. Center-punch two holes down the center of the widened end, ¾ inch apart. Center punching will create a depression to seat the drill bit, preventing it from skating around and missing your mark.

- Next, taper behind the widening slightly to help balance the weight of the shovel. Keep the widened tab over the far edge of the anvil; remember to go from square to octagon to round. As you get closer to the tab, use a ball-peen or rounding hammer on the horn to clean up the transition where it begins to widen.

- Using a rounding or ball-peen hammer and a curved shape, such as the anvil horn, taper and round 1½ inches of the handle end.

- Flatten 5 inches of the handle slightly and put a small curve into the handle over the horn. Proceed to bend the tip you drew out 45 degrees, and bend it around with a pair of scrolling tongs to create a loop to hang the shovel. Clamp the shovel to the handle to drill the holes and then rivet with ¼-inch rod. Bend the handle near the shovel to a comfortable angle for you to use.

Forge Ladle
Starting Stock
- Handle: ⅜-inch square rod, 2 feet long
- Ladle: 18-gauge sheet metal, 6-inch-diameter circle
- Rivets: ¼-inch round mild steel
Tools Required
- Hammer
- Anvil
- Method of “dishing” sheet metal (e.g., swage or wood stump)
- Method of cutting sheet metal (angle grinder with a cutting disc, cold chisel, hacksaw, bandsaw, oxy/acetylene torch, plasma cutter)
- Hot cut, chisel, or hacksaw for partially cutting off rivet
- ¼-inch punch
- Vise
- Drill and 1⁄4-inch metal drill bit

- Mark a 6-inch diameter circle out of your 18-gauge sheet metal. In this case, I cut it out of the 55-gallon drum lid that I also used for the coal scoop. Using your preferred cutting method, cut close to the line and then file or grind the blank to the line you drew. This will give you a nice, round ladle blank.

- I used a cupping swage designed for forging spoons and ladles; you can buy or make a similar one. You also could use any similarly dished shape, such as the metal cap from an old oxygen tank or a wooden stump stood on end.

- With a rounding hammer or larger ball-peen hammer, begin dishing from the center of the circle and continue working your way out in a spiral pattern. Work in overlapping hammer blows to smooth the ladle.

- To start the handle, taper one end of the ⅜-inch square rod on the far side of the anvil with full-face hammer blows until the taper is 1½ inches long. Let it widen (this will later become a fishtail scroll).

- Curl the end of the handle taper over the rounded far edge of the anvil and begin scrolling by holding the rod flat on the anvil and continuing to hammer back toward yourself. Remember that consistent heat makes your scrolls smoother. As you notice irregularities, correct the scroll as shown by lifting the rod off the anvil and hammering. If your scroll doesn’t end up smooth and symmetrical, unroll it with a pair of scrolling tongs or pliers and begin again. You can correct some minor alignment issues by hammering it on edge.
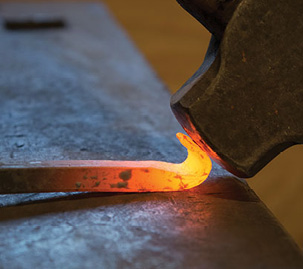
- Bend 6½ inches approximately 45 degrees to one side over the far side of the anvil and then bend 5 inches around your horn, mandrel, or ¾-inch rod held in a vise. The diameter of the ring should be ¾ of an inch.
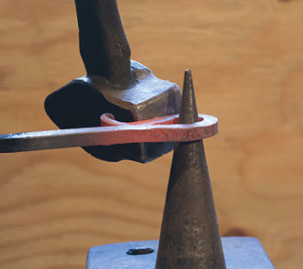
- Line up the bend of the ring so that 1 inch of the end taper is flat against the shaft, as shown. To flatten it, place the loop over the far edge of the hole with the scroll up and use your cross-peen to get between the ring and the scroll without damaging them.

- Quench the handle end and heat up the other end to create the area to attach the ladle. Flatten 1½ inches over the near side of the anvil down to ⅛ inch thick. Create a step by using a half-faced blow, as shown. Let the steel widen to create as much contact area as possible for the ladle. After flattening the end, punch two ¼-inch holes in the flattened portion, ½ inch in from each end. Once you’ve punched the rivet holes, curve the end over the horn so that it matches the curve of your ladle.

- Mock assemble the ladle and handle, with the handle on the outside, and mark where the punched holes line up on the ladle bowl. Drill two ¼-inch holes in the ladle at your marks. Make two ¼-inch-diameter rivets to attach the handle and then rivet the ladle to the handle. I find it easier to assemble the ladle with the preformed head on the outside and rivet the inside head while supporting it on the near edge of the anvil, as shown. You can rivet these cold, but I prefer to heat them to red in the forge before fully cutting the prepared rivet off its parent stock. If you don’t feel comfortable making your own rivets yet, purchase them from a local welding or agricultural store.
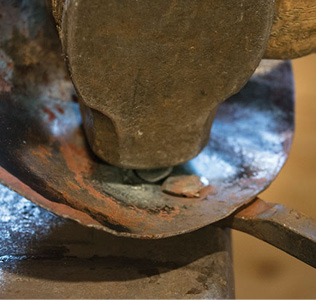
Note: Remember that the shaft length of a rivet with one preformed head should be the total width through which the rivet will be passing plus two times the shaft diameter—in this case, a maximum of ½ inch extra on a ¼-inch-diameter rivet.
Coal Scoop or Scuttle
Starting Stock
- Handle: ½-inch round rebar, 25 inches long
- Shovel: 18-gauge sheet metal, 7¾ x 9½ inches
- Rivets: ¼-inch rod
Tools Required
- Hammer
- Anvil
- Method of “dishing” sheet metal (e.g., swage or wood stump)
- Method of cutting sheet metal (angle grinder with a cutting disc, cold chisel, hacksaw, bandsaw, oxy/acetylene torch, plasma cutter)
- ¼-inch drill bit and drill

- As I mentioned in the ladle project, I used the same metal drum lid for the ladle and for this project; shown is the shovel blank for the coal scoop. The blank is 7¾ inches wide by 9½ inches long, and the inside chalk lines, where I will be bending the sides up, are 1 inch inside. Clean up any sharp edges after cutting out the blank.

- Notch the end of the blank as shown, in line with the inside bend lines. Because the sides will be 90-degree corners, the notches will make it easier to dish and fold the edges up without wrinkling.

- In the vise, fold both edges 90 degrees along the 1-inch chalk line. Using a dishing stump or swage and a rounding or ball-peen hammer, dish the end up, as shown. Once it is dished up, fold the tabs behind to help strengthen the shovel.

- On the face of the anvil, flatten 7½ inches of the rod and widen it to a minimum of ¾ inches. You will split this into two later, so you need as much width as you can get. You can use a cross-peen to help widen it once you have begun to flatten it.

- Flatten any irregularities in the edges without drawing out the width (remember that you need all of the width you can get).

- Set down the end of the widened area to create a slight shoulder for the edge of the shovel to sit in, but no more than ⅛ inch. Neck down and slightly taper the area just behind the widening, as you did for the forge shovel.

- With your cutting tool, split 6¼ inches of the widened area in half. Over the near edge of the anvil, using half-faced blows, set down ½ inch on the same side of both ends of the slit material. These will be drilled and riveted to the sides of the scoop.
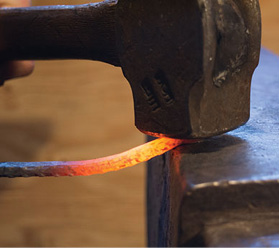
- Center-punch and drill ¼-inch holes in the center widening that was left intact and in the two split ends. Bend the ends, as shown, to match the outside of the coal scoop.
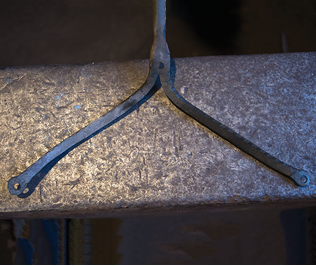
- Set down adjacent 90-degree sides over the near side of the anvil with half-faced blows. Taper it into a 3-inch-long point.

- This is what the end should look like after setting down the sides. Continue tapering the end to a sharp point.

- With your scrolling tongs, create a scroll and proceed to bend the handle around the horn, as shown. Stop once the tip hits the shaft of the handle. Heat the corner just before the hammer (refer to the photo) and bend the handle flat over the anvil face.

CHISELS AND PUNCHES
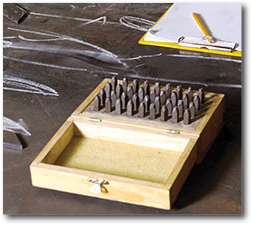
Did You Know?
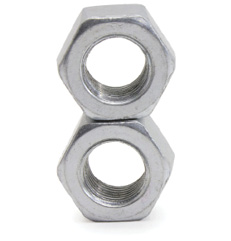
Handheld Chisel
Starting Stock
- ¾-inch medium- to high-carbon steel 10–12 inches long
Tools Required
- Hammer
- Anvil
- Appropriate quenching medium: oil for high-carbon steel or water for medium-carbon steel

One of the best chisels you can have for removing rivets has a curved edge and a single bevel.
- To forge a straight chisel, begin by tapering two sides.

- Correct any widening so that the chisel edges are in line with the shaft edges. Now heat the chisel up to nonmagnetic and let it cool by the fire. Once cool, heat half of the chisel up to nonmagnetic and quench one-third of the tip in water or oil. Quickly polish the tip and watch the colors run as the remaining heat tempers the tip. Quench it again when it reaches straw yellow at the tip.

Sharpen the chisel to a 60-degree edge, taking care to not heat the tip up with the grinder, and test to see if your chisel will cut cold metal. If the edge dulls right away, it needs to be tempered to a harder temper. If the edge chips, it needs to be a softer temper.
All chisels are made the same way, but with a different edge ground in. For example, a slitting chisel has a V-shaped point ground into the edge rather than a straight edge. To add a handle, punch and drift an eye for the handle, as I will demonstrate in the next project, the handled slot punch.
Handled Slot Punch
Starting Stock
- 1¼-inch medium- to high-carbon steel, 6 inches long
Tools Required
- Hammer
- Anvil
- Handheld slot punch

- To make a handheld slot punch, simply forge a longer tapered chisel (see previous project) and leave the end flat. Relieve any sharp corners around the edges of the bevel to prevent any sharp corners in the hole when you later drift it open.

- For this handled slot punch, I used the male joint on a piece of oilfield sucker rod. The transition to ¾-inch round from larger 1¼-inch steel makes for an easier time forging. You can use any 1¼-inch steel, but you have to forge the punch end down until it looks like that shown in the photo. Flatten the taper on a 45-degree angle to where the handle will go through to make it easier for you to line up the punch while holding the metal.

- Using your handheld slot punch, punch through the flattened area from both sides so that the slug meets in the middle. This will minimize the taper of the eye, making drifting easier.
After you have punched through the eye, continue to drift out the eye using your slot punch; enlarge it by hammering the sides into an eye mandrel to draw them out. Work from both sides to minimize the amount of taper. You can make a separate mandrel to protect your slot punch if you wish, but I just reforge and heat-treat my slot punches as needed.

Punches

Eye Drift and Mandrel
Starting Stock
- 1¼-inch axle shaft or similar medium-carbon steel, 8 inches long
Tools Required
- Hammer (the heaviest that you can swing comfortably) or striker with sledge
- Anvil

- Begin by tapering the drift to 5 inches long on two sides. Correct the widening and taper the other two sides in so that the end of the drift matches your slot punch, ⅞ x ⅛ inch in this instance. Flatten the portion behind the working taper to 1½ x 1 inch for 3 inches and then taper the hammer end slightly. This reverse taper lets you hammer the drift all the way through, rather than trying to reverse it out of the hole. Because they are not doing any cutting or hard labor, I don’t bother to heat-treat my drifts because they lose their temper once in the hot hammer eye. Simply normalize or anneal the piece at the end of forging to reduce any grain stresses.

- Always correct the fish lips that develop as you forge this thicker steel. Because your hammer blow is strongest at the edge, the outside of the metal moves the most. If these fish lips continue to develop, they will be tapered down into two 1⁄16-inch thin pieces of metal with a cold shut between them. It wouldn’t take much to break the tip of the drift if that happens. To correct it, simply upset the end back again until it is flush.
Note: If you end up with cold shuts at the end of the process, you can forge weld it together to avoid forging another one, but it will be a weaker tool. It is best to prevent such problems from the start.

Tongs
Starting Stock
- Two pieces of ¾-inch round rod, 16 inches long
- Rivets: ⅜-inch round rod, more than 3 inches long for each
Tools Required
- Begin over the near side of the anvil with half-faced hammer blows. Set 2 inches down to less than half of the starting diameter to allow for finishing later. Draw out the jaw, again leaving a little extra for finishing. The jaws should taper toward the tip for maximum strength.

- Rotate the stock 90 degrees away from your body and hold the tongs at a 30-degree angle. Set down at the beginning of where you set down in the first step. To prevent thinning the stock down too much before you are finished forging to the proper dimensions, don’t forge it down to half of the original diameter.

- Rotate the stock another 90 degrees away from you and set the rein side of the boss down over the far side of the anvil with a half-faced blow, the same way that you did in the first two steps. The boss for the rivet should be 1¼ inch back to allow for finishing. Make sure that the taper is away from the boss you’ve created. Proceed to finishing the jaw up and draw out the reins down to ½ of an inch on the end. You can cut off the jaws a few inches past the boss and forge-weld the jaws onto ½-inch round to save drawing out the reins.

- Using a fuller, create a depression in the middle of the jaws to grab round and square stock better. With a chisel, cut grooves into the sides to help grip flat bar. Punch and drift out a ⅜-inch hole so that the rivet fits snugly. Repeat on the second blank, just as you did for the first one; they need to be exactly the same.

File the inside of the boss flat so that the two tong blanks fit together nicely. Test-fit with a nut and bolt instead of with a rivet, in case you need to separate the tongs and file more off the inside. Once you are happy with the fit, make a rivet out of ⅜-inch rod and rivet the two pieces together. Heat the boss up and open and close the tongs a few times to loosen the hinge after riveting.

Perfect Fit
Claw Hammer
Starting Stock
- 1-inch tie rod or similar medium-carbon steel, 6 inches long (You can increase the diameter of steel if you want a heavier hammer.)
Tools Required
- Hammer
- Anvil
- Slot punch
- Hammer eye drift
- Cold chisel
- Cutting plate

- Begin by slightly upsetting the hammer end to create a ⅛-inch wider end. It’s very slight, but it will help balance the hammer to the front. Flatten 1½ inches from the hammer head end to make punching easier. It should be no less than 1 inch thick once flattened; you just want to help keep the piece from rolling away while you slot-punch.
Using the slot punch you made previously, punch through from both sides. Set the punch 2 inches from the hammer head and in the midline. Remember to use light blows at the start so that you can move the punch if needed.

- Once you’ve punched the hole, begin to drift the hole with the eye drift you just made. Because I fasten the head with a wedge, I like to drift more from the topside to create more taper on the top so that it wedges more securely than a flat-sided eye. Draw out the eyes over the anvil to help stretch the metal rather than having the drift pull it wider, which can lead to cracks. If the eye is moving more on one side than the other, or getting off center, draw out the shorter side with the mandrel in place and with the other cheek protected in the hardy hole or in your opened vise. This will help keep the eye symmetrical and centered.

- Over the near side of the anvil, taper down the claw end of the hammer. (Note: If this were a cross-peen, you would want a steeper taper.)

- With a 60-degree-edged chisel, slit the claws from the underside. (Note: Although a cutting plate is not pictured in the photo, be sure to use one to protect your anvil face.)

By cutting through from one side, you create a taper to catch the nail heads automatically. If you want to make a leafing hammer, dishing hammer, or cross-peen hammer, simply dress the taper to the shape you want rather than splitting it.
Proceed to heat-treating the hammer head. Anneal and harden as you normally would, but this time, temper the head by heating up your mandrel and fitting it in the eye. Quench when the face turns straw yellow.
Crowbar
Starting Stock
- 1-inch round or octagonal medium-carbon steel, 18 (or more) inches long
Tools Required
- Hammer
- Anvil
- Chisel
- Cutting plate
I made this crowbar with a shorter shaft simply because I had many longer ones that didn’t fit in tight places. You can adjust the length of your starting stock according to the desired length of crowbar.

- Taper one end of the bar 2 inches and the other end 2½ inches, down to ⅛-inch thickness on both ends. The 2-inch end will be the chisel end, and you will split the 2½-inch end into the claws.

- While tapering, hold the taper on edge and correct any widening that occurs. You will need a slight taper to the width, as shown.

- Using a cutting plate to protect your anvil face, slit 1½ inches of the longer taper down the middle. Because you want a taper inside the slit to help grab nails, only slit from one side with a cold chisel, as shown. The bevels of chisel will taper the inside of the slit naturally.

- In the vise, clean up the end of the slit by holding the chisel at a slight angle so that there is a taper past the end of the slit to house a nail head.

- Over the horn or a curved piece of steel, bend the chisel end slightly to create a prying surface.

- Bend the claw end of the crowbar 4 inches from the end, as shown, using your anvil horn or a large rod. Put a slight curve into the prying end before the claws, as shown, to help make prying easier.

- Taper the bend as you did with the fire rake to strengthen the bend (see Step 3 in the rake project). Again, do this over the far side of the anvil, as shown, to protect the anvil face from errant hammer blows.
After you are done forging, normalize or anneal the crowbar by heating it to nonmagnetic and either leaving it by the fire or burying it in ash so that it cools slowly. This step removes any grain stresses that occurred during forging. Once it is normalized or annealed, you can either leave it as is or heat-treat it to improve its strength. If you leave it at its softest, it is more likely to bend; however, if you temper it too hard, it will be more likely to break.
Heat-Treating the Crowbar
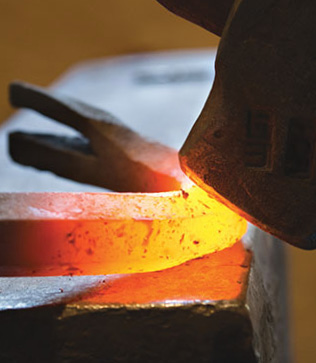
Flat-Bit Screwdriver
Starting Stock
- ¾ x ¼ inch rectangular medium-carbon steel, 6 inches long
Tools Required
- Hammer
- Anvil
- Spring fuller or guillotine
- Brazing rod
- Drill and ⅛-inch metal drill bit

- Taper the end down to ½ of an inch; the taper should be 4 inches long. Next, fuller ¾ of an inch back from the end to define the transition between the neck and the head of the screwdriver. The end dimensions of the transition to the head will be ¼ inch, so fuller down to ⅜ of an inch to start. You will forge it to the final dimensions later when finishing the screwdriver.

- This image shows the guillotine fuller being used on a different project. As you can see, there are different-sized spaces ground out so that the guillotine can be used for fullering pipe. You can make a guillotine fuller if you have a welder, a file or grinder, and a drill press. I made this one from mild steel; the bottom jaw is fixed, while the top jaw is hinged on a bolt.

- Once you’ve fullered the neck, forge it down to its final dimensions, gradually tapering down to the head transition, which is ¼-inch square. To do this, alternate between the near (a) and far (b) edges of the anvil. Once you’ve finished the taper, chamfer the edges of the neck by holding the edges perpendicular to the anvil and forging them back into the mass; this is the same technique as you would do to begin rounding the metal. Finish by creating a flat taper on the end of the screwdriver as you would for a chisel. File the end smooth and square so that it matches the screw head it will be used on.

- Cut the screwdriver off any remaining metal so that the handle is 4 inches long. Either forge or file a slight curve to the end for aesthetics and to get rid of any sharp edges. Drill ⅛-inch-diameter holes in the handle that are the same dimensions as the brazing rod, 2½ inches apart, centered on the handle. After you’ve drilled the holes, proceed to heat-treating the screwdriver by heating it to nonmagnetic and letting it cool by the side of the fire. Once it is cooled, heat the tip and neck back up to nonmagnetic and then quench only the tip. Next, quickly polish the head of the screwdriver so that you can see the temper colors run. Quench the screwdriver completely once the tip turns yellow.

- Cut a piece of hardwood 3 x ¾ x ¾ inches. Round the ends to create the profile seen here and then split it in half to create the two identical halves that will make your screwdriver handle. Match the holes drilled in the handle of the screwdriver body by clamping the wood to the screwdriver and drilling through the pre-existing holes in the metal. Next, countersink the holes on the outside of the wood to house the brass rivet head. Sand the pieces smooth and round the corners. If the handle is too wide, sand the wood slabs until the screwdriver feels comfortable in your hand when it is mock assembled.

Remove the flux and cut two rivets from ⅛-inch brazing rod, which you can get from most hardware, agriculture, or welding-supply stores. Measure the total width of both handle slabs and the handle of the screwdriver as assembled and add two times the diameter of the brazing rod, ¼ inch in this case. The extra metal will become the rivet heads once they are peened.
Assemble the handle and, with a ⅛-inch spacer under the handle to protect one side of the rivet, begin to peen the rivet. Once one side is peened, flip to the other side and peen it without a spacer under the handle. Repeat the process on the second rivet, and you have a brand-new screwdriver!
Nail and Rivet Header
Starting Stock
- Header: 1-inch round medium-carbon steel, 1 inch long
- Handle: ¼-inch round, 2 feet long
Tools Required
- Hammer
- Anvil
- Means of cutting a rod to length
- Square punch (See the Handled Slot Punch project)
- Vise
- Hot-cut hardy

- Cut off 1 inch of 1-inch diameter round medium-carbon steel. Medium-carbon steel will be more resilient to errant hammer swings than mild steel. In this photo, I am using my anvil hardy, but you can use any cutting tool, such as a hacksaw, cutting torch, or abrasive saw.

- Upset the header with lighter hammer blows to rivet over both sides and create a lip for the handle to sit in. Flip the piece and work both sides evenly to create a lip on both sides. Form a slight dome on one side to make heading the nail easier.

- Using a square punch with a ⅛-inch square end (a), punch completely through from the back side (b). Once the punch feels solid when you hit it, shear out the plug over your pritchel hole (c). Only punch and drift the hole to ¼ inch from the top to create a slight bevel around the hole to prevent damaging the nails you make. Most household nails are made from ¼-inch nail stock, and you need a slight lip to catch the nail to head it.
After punching the header, the dome will be flattened and need some dressing. Be careful to keep from damaging the hole you punched. If you do need to repair the hole after dressing the dome, use the punch again; be careful not to punch too deep or the hole will be too large.

- Center-punch to mark the middle of the ¼-inch round rod. Heat it and wrap it around the cooled header, which is held in the vise. Cross over the handle ends tightly against the header and begin to twist. Once you’ve started the twist, clamp the handle in the vise and continue twisting the rods tightly with your tongs, as shown. Straighten the header handle on the anvil, making sure to rotate the handle in the same direction that you twisted. If you rotate opposite to your twist, it will loosen the header, leading to much frustration.
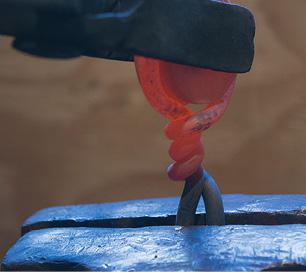
- After straightening the rods for the handle, clamp 1½ inches of the end in the vise and twist with the tongs, as shown. Once the ends are twisted together, cut one of the rod ends at the end of the twist. Blend the cut end of the rod into the twist around the other rod and proceed to taper the remaining end.

- Over the far side of the anvil, square-taper the remaining end with full-faced blows. Continue through the steps of rounding the taper.

- With your scrolling tongs, or over the far side of the anvil, bend the taper 45 degrees at the end of the handle twist.

- Curl the taper around with your scrolling pliers, horn, or 1-inch rod that is held in the vise.

- Once you’ve finished your header, it is only fitting to make a test nail (see project in Chapter 7) from which to hang the header.
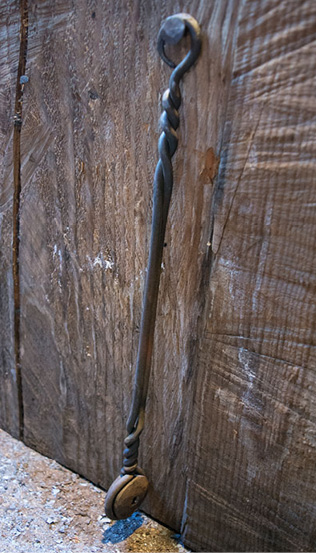
Hold-Down
Starting Stock
- ½-inch mild-steel rod, 24 inches long
Tools Required
- Flatten 1 inch of one end of the rod to a ¼-inch thickness. Proceed to bend the rod around the horn at the center point.

- Flip the bar so that the untouched side is up and then bend the side with the flattened end over the horn, as shown.
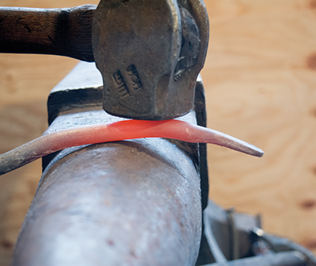
- To use this tool, tap the straight end into the pritchel and use the foot you created to hold pieces tightly on the anvil while you chisel or fuller them.

Spring Fuller with Adjustable Hardy Shaft
Starting Stock
- ¼-inch by 1-inch flat bar, 40 inches long
Tools Required

- Begin by bending 8 inches 90 degrees over the far side of the anvil.
(Note: The bends in this project can be hard to follow. If you become confused, refer to the finished photo to help you figure out the bends.)

- Seven inches further into the bar, bend the bar back on itself loosely to become the hardy shaft, as shown. Make sure that the shaft is long enough to stick out below the heel of the anvil so that a wooden wedge can be used to wedge it in place. Leave a gap because you will be wedging a piece of wood between the two sides to wedge the fuller in place.
Bend the bar back 90 degrees, even with the other side of the hardy shaft, to make a “T.” I find it easiest to do this part when the shaft is in the hardy.

- Bend the bar back around, 3 inches further in from the hardy shaft, using your anvil horn. You want the two ends of the bar to run parallel to each other.
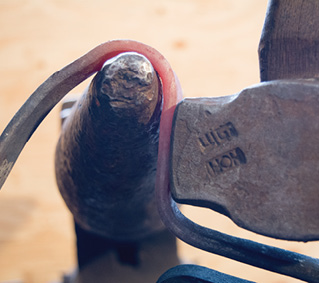
- Clamp the bar in the vise 4 inches back from the end and twist as shown. Repeat on the other end, and you have a matching pair of fullers. You can make fullers of different radiuses by changing the thickness of the bar that you use; just remember to round the edges.
