1 Introduction
In process development, sustainability has become the focus of industry and science with the goal of decoupling economic growth from the increasing consumption of resources (Hirzel et al. 2013). In 1987 the United Nations defined the concept of “sustainable development” as part of the Brundtland report. According to this, it is a “development that meets the needs of the present generation, without jeopardising the ability of future generations to meet their own needs” (BMUB 2018). Subsequently three dimensions of sustainability, ecology, economy, and social issues, were derived from the concept of “sustainable development” and transferred to the so-called “three-pillar model” (von Hauff and Kleine 2014). Given a technology-wise feasible and operable process, an incorporation of economic, ecological and social aspects has become mandatory in today’s process development.
Material flow cost accounting (MFCA) is one possible approach which can be used to evaluate the resource efficiency and take the ecological and economic aspects into account. The MFCA was developed in the late 1990s and is already widely used in different industries (Schrack 2016; METI 2010). In 2011 it was officially released as an international standard to serve as a management tool in organizations to consider “potential environmental and financial consequences of their material and energy use practices” (ISO 14051:2011). Compared to conventional cost accounting, MFCA allocates the expenses both to the products and to the material and energy losses (“non-products”). In its overall objective, MFCA aims at the quantification and visualization of material losses, thereby contributing to the motivation of the organization to reduce material and energy consumption (Viere et al. 2009, ISO 14051:2011). By reducing the use of materials and energy, on the one hand, the costs and, on the other hand, the impact on the environment should be reduced. The ecological aspect is thus indirectly taken into account in the MFCA. The material losses are only recorded in physical and monetary units and can pollute the environment as waste, sewage or emissions. Unlike the Life Cycle Assessment (LCA), MFCA does not provide an impact assessment, so the potential direct environmental impacts are not investigated. MFCA is primarily used in the evaluation of productions of general cargo at the product and plant level (METI 2010). In the material-converting industry as well, the application of MFCA can be used to identify potentials for improvement with regard to the use of energy and raw materials.
In the German Federal Ministry for Economic Affairs and Energy (BMWi) research project µKontE,1 a production process of a binding agent emulsion was transferred from a batch to a continuous mode of operation. First of all, the conception of the production plant and then the establishment in production took place. The initial batch process as well as the newly developed continuous process were evaluated and compared among others through MFCA. To investigate the applicability of MFCA during process development, the influence and benefits of different levels of detail in regards to the process modelling were examined.
2 Description of the Process
AURO Pflanzenchemie AG provided the investigated binding agent emulsion production process. For this case study process data, e.g. energy consumption, type and amount of process material and reactants, and information relating to the different cost types from the company were used. The batch production was carried out in an agitator vessel with heating jacket in which all process steps were performed consecutively. At the start, all reactants, consisting of partially organic as well as aqueous chemicals, are fed to the reaction vessel and heated up. Afterwards, several emulsification and shearing steps are applied until the required droplet size is achieved. Finally, the binding agent emulsion is drained from the stirred tank and the equipment is cleaned. In continuous production, the respective preparation of the organic and the aqueous reactants takes place simultaneously outside of the actual reaction vessel. These two phases are then combined and pre-emulsified in a passive mixer (premixer). Subsequently, this pre-emulsion is emulsified in an active mixer (rotor-stator mixer) in order to achieve the required product properties.
The transfer of this process from batch to continuous production involved several constraints with respect to the manufacturing scheme. The advantages of batch production concerning the production flexibility due to fluctuating market demands had to be maintained at the same time ensuring a constant and high product quality through online monitoring of process parameters in the continuous procedure. Furthermore, the high energy consumption of the batch production due to consecutive heating and cooling steps in a single vessel were targeted for heat integration in the continuous production process.
It was shown, that the specific energy demand in continuous production has been reduced by 50% compared to the batch process (Wengerter et al. 2017). While batch production required a high level of cleaning effort, the continuous operation of the system could be significantly reduced through the implementation of microstructured devices and thus lower plant hold-up and significantly increased cleaning intervals. Furthermore, personnel expenditures were considerably reduced by a largely automated plant control for the continuous process.
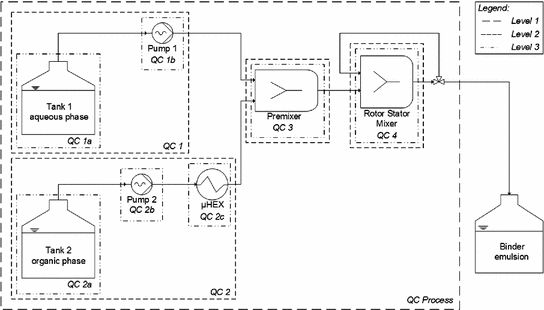
Process flow chart with the quantity centres of the three levels of detail
According to ISO 14051, the costs of the materials, the energy, the system and the waste management have to be taken into account. The material costs were allocated based on the mass balance for the individual quantity centres. The energy costs were allocated to the quantity centres according to the respective energy consumption. In this case, the system costs accounted for the monetary expenditures for intra-logistics, maintenance and the machine hourly rate as well as personnel costs. The first three cost items were allocated according to the number of quantity centres, while personnel costs were allocated according to the duration of work per quantity centres. The material losses were accounted for 100% of the waste management costs. These cost elements and their allocation have been taken into account for the different levels of detail with regard to the quantity centres.
The examined first level of detail included the production process as a single quantity centre, so that the input and output flows as well as costs were recorded in total over the full production plant. The second level included the structure of the plant by breaking down the model into the individual process steps. In the third level of detail, the individual components of the plant equipment of the respective UO were each assigned to individual quantity centre in order to enable the analysis of the plant and apparatus design in regards to potential improvements. Above all, the investigation aimed at a possible increase in energy and resource efficiency with regard to instrumental implementation.
3 Results and Discussion
The investigation on the first level of detail showed that material costs accounted for more than 90% of the overall cost. Thus, one option to reduce the cost of materials is the use of cheaper, alternative reactants. Although cheaper reactants may have a positive effect on manufacturing costs, they may also have a negative effect on product quality due to higher impurity levels. System costs accounted for the second highest share of costs at 9.31%, while energy costs are comparatively low at 0.58%. However, both system costs and energy costs are in absolute terms a big expense for the company, so they should be investigated further.

Cost flow of the second level

Cost flow of the third level
The investigations show that the effort for the necessary data collection increases significantly with the increase in the level of detail. The process data for each level of detail were collected directly at the system. For example, the energy consumption for each equipment was recorded by means of appropriate measuring points. However, this depends on the particular system, the measuring equipment and the procedures within the company itself. The third level is of great interest from an engineering point of view, as both the materials used and the design can have a direct influence on the required energy input. Thus, in combination with information about the individual UO process, engineering potentials can be identified, which can serve as a basis for technical improvements. In addition, findings from the detailed presentation of the system costs, in particular with regard to the space costs as well as maintenance and servicing depending on the technology used, are relevant in this context.
However, such an extensive analysis of the process is not needed in many cases. For example, in the development phase, data about the individual equipment is an advantage, while less detailed information about the production process are required for the management to support decision-making. Therefore, the level of detail should be tailored to the information needs of the target group based on the workload prior to the implementation of the MFCA.
The MFCA takes the ecological aspects into account indirectly. The material and energy inputs as well as the material losses can be assigned to their causes. However, MFCA does not identify the direct impact on the environment but merely identifies possible starting points for improvements in resource use. For a closer examination of the ecological aspects, a linkage with the LCA should be made. For a full view of sustainability, in addition to MFCA and LCA, social aspects must be considered. These are reflected in the production, for example, by the commitment and the tasks of the employees. This can be investigated, for example, by means of social life cycle assessment (SLCA) (Klöpffer and Grahl 2009).
4 Summary
As part of the μKontE project, a process for the production of a binding agent emulsion has been transferred from batch to continuous operation. Through the implementation of a development accompanying MFCA, the process transfer was supported and evaluated. Furthermore in this case study the influence and benefits of increasing the level of detail regarding the definition of quantity centres were examined.
The advantage of the MFCA, compared to conventional cost accounting, is the direct allocation of the costs also to the waste. An increasing level of detail in MFCA offers the opportunity to extract insights relevant to the respective target group. In this way, potential savings can be directly identified through a more detailed analysis and thus support process improvement. As a result, especially the economic effects of process changes can be demonstrated and the process understanding can be increased. This is necessary in order to be able to derive corresponding improvements from the MFCA, for example in terms of equipment. However, increasing the level of detail is associated with growing data requirements and thus higher temporal effort required for this method. This is difficult in early stages of process development, as some information is missing. Therefore, assumptions must be made, which in turn affect the validity of the data. In addition, the MFCA only indirectly takes the impact on the environment into account, so that a link with LCA is possible for a more detailed study of the ecological aspects. Overall, in the context of process development the advantages of increasing the level of detail in terms of the direct identification of perpetrators on the equipment level outweigh the expenses for the more extensive data collection.