Chapter 18
Polymer Applications: Plastics and Plastic Additives
18.1 Introduction
As mentioned in the introduction to this book, there are five major applications for polymers: plastics, rubbers, synthetic fibers, surface finishes, and adhesives. Previous sections have dealt with the properties of polymers themselves. Although these properties are undoubtedly most important in determining the ultimate applications, polymers are rarely used in a chemically pure form; so in a discussion of the technology of polymers, it is necessary to mention the properties of polymers used for these industrially important applications. There are also numerous modifiers and additives commonly used, which are introduced in Section 4, but are useful in many products that fit any of the five applications discussed in the next five chapters. This chapter will focus on simple plastics.
18.2 Plastics
Plastics are normally thought of as being polymer compounds possessing a degree of structural rigidity–– in terms of the usual stress–strain test, a modulus on the order of 108 Pa (N/m2) (15, 000 psi) or greater. The molecular requirements for a polymer to be used in a plastic compound are as follows: (1) if linear or branched, the polymer must be below its glass transition temperature (if amorphous) and/or below its crystalline melting point (if crystallizable) at use temperature; otherwise (2) it must be crosslinked sufficiently to restrict molecular response essentially to straining of bond angles and lengths (e.g., ebonite or “hard” rubber).
18.3 Mechanical Properties of Plastics
The engineering properties of commercial plastics vary considerably within the broad definition given above. Figure 18.1 sketches some representative stress–strain curves for three types of plastics. As discussed previously, for any given material, the quantitative nature of the curves depends markedly on the rate of strain and the temperature. In general, faster straining and lower temperatures give higher moduli (slopes) and smaller ultimate elongations.
Figure 18.1 Typical stress–strain curves for plastics: (a) rigid and brittle; (b) rigid and tough; (c) flexible and tough.

Plastics with stress–strain curves of the type in Figure 18.1a are rigid and brittle. The former term refers to the high initial modulus. The latter refers to the area under the stress–strain curve, which represents the energy per unit volume required to cause failure. These materials usually fail by catastrophic crack propagation at strains in the order of 2%. Since hardness correlates well with tensile modulus, which is another valuable property of this type of plastic. Examples of this class are polystyrene, poly(methyl methacrylate), and most thermosets.
Curve b represents rigid and tough materials, sometimes known as engineering plastics. In addition to high modulus, tensile strength and hardness, these materials undergo ductile deformation or drawing beyond the yield point, evidence of considerable molecular orientation before failure. The latter confers toughness or impact resistance, that is, the ability to withstand shock loading without brittle failure. Examples of this class of materials are polycarbonates, cellulose esters, and nylons. Although the reasons are not entirely clear, such plastics generally exhibit a secondary dynamic damping peak (Chapter 15) well below their use temperature.
Curve c represents flexible and tough plastics, as typified by low- and medium-density polyethylenes. Here, the ductile deformation leading to very high ultimate elongations results from the conversion of low-crystallinity material to high-crystallinity material. The tensile samples “neck down” with the density, percent crystallinity, and modulus of the material in the neck being appreciably greater than those of the parent material. Despite their good toughness, these materials are limited in their structural applications by their low moduli and tensile strengths.
18.4 Contents of Plastic Compounds
In addition to the polymer itself, which is seldom used alone, plastics usually contain at least small amounts of one or more of the following additives (summarized in Table 18.1) [1, 2].
Table 18.1 Common Additive Types for Plastics.
Additive Type | Example(s) |
Reinforcing agents | Graphite fibers |
Fillers | Wood flour, calcium carbonate |
Coupling agents | Bifunctional silanes |
Stabilizers | Quinones and other free-radical scavengers |
Pigments | Titanium dioxide, carbon black |
Dyes | Various colored dyes |
Plasticizers | Phthalates, medium MW organics |
Lubricants | Stearic acid, low MW organics |
Processing aids | Low MW polymers (to reduce viscosity) |
Curing agents | Sulfur, crosslinking agents (often with a promoter) |
Blowing agents | Pentane and volatile organics, CCl3F (makes foam) |
Flame retardants | Phosphorus, organics with Br or Cl groups |
18.4.1 Reinforcing Agents [3]
The function of these is to enhance the structural properties of the compound, in particular, properties such as modulus (stiffness), strength, and the retention of these properties at higher temperatures. The use of long fibers to reinforce epoxy and polyester thermosets was mentioned in the previous chapter. While glass is by far the most common reinforcing fiber, largely due to its strength, ready availability, and relatively low cost, other, more exotic fibers are used where very high strength-to-weight ratios are required and cost is of secondary concern. Carbon or “graphite” fibers, made by pyrolysis of pitch or polyacrylonitrile fibers, offer superior performance at a cost premium over glass. They are used in many aerospace applications and in more down-to-earth objects such as golf-club shafts, tennis-racket frames, racing-car bodies, and automotive springs and driveshafts. Aramid (aromatic polyamid) fibers (Kevlar) are also used to reinforce plastics for premium-property applications, sometimes in combination with other fibers. And, more recently, nanofibers (including carbon nanotubes) and nanoclays have been employed as additives to strengthen plastics with even smaller amounts of additive (see Figure 18.2).
Figure 18.2 Stress–strain curves showing the effect of adding carbon nanofibers to poly(ether ether ketone), PEEK, a semicrystalline thermoplastic. Reprinted from [4] with permission from Elsevier.
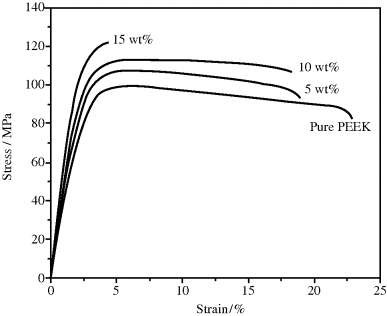
Short (1/8 to ½ in.) (3–13-mm) glass and other fibers are used extensively to reinforce thermoplastics [5]. Addition of up to 40 wt% short glass fibers to nylon, polypropylene, poly(butylene terephthalate), and others, provides a relatively inexpensive way of greatly improving the structural strength of the plastic, as illustrated in Table 18.2. The glass-reinforced materials also have less mold shrinkage and, therefore, give parts with better dimensional control and stability. The down side is that they are more difficult to process and often have a rough surface finish.
Table 18.2 Some Propertiesa of Short Glass Fiber-Reinforced Thermoplastic [6]
Note that major gains in heat-distortion temperature are obtained when using reinforcing agents with the crystalline polymers nylon 6/6, poly(butylene terephthalate), and polypropylene, but not with the amorphous polystyrene and polycarbonate. This is a general result. The crystallites “lock on to the fibers, maintaining mechanical integrity well above Tg.
Another example of reinforcement is the use of up to 20% dispersed rubber particles, on the order of 1 μm in diameter, to increase the toughness or impact strength of a normally brittle plastic. Figure 18.3 illustrates the effect of adding increasing levels of a micron-sized rubber to polystyrene in a high rate-of-strain tensile test (to simulate shock loading). The addition of the rubber particles decreases the modulus (slope) and ultimate tensile strength but introduces considerable ductile deformation (elongation beyond the “knee”), thereby increasing the area under the stress–strain curve. It also imparts a secondary dynamic damping peak below use temperature. In effect, it converts a type a material (Figure 18.1) to a type b material. For many applications, the improvement in impact strength considerably outweighs the slight decreases in modulus and tensile strength produced by the addition of rubber. Impact modifiers are rubbery additives that impart such toughness when blended with plastics. Proper compatibility (good adhesion but not solubility) between the phases is essential in these applications. This is often achieved with graft and block copolymers (compatibilizers), which have blocks of repeat units at each end that are compatible with each polymer phase.
Figure 18.3 The influence of discrete, micrometer-sized rubber particles on the high-speed (133 in/in min) stress–strain curves of polystyrene [7].

Commercially important examples of rubber-toughened plastics include the high-impact polystyrenes (HIPS), in which polystyrene is toughened with a polybutadiene rubber, and the acrylonitrile-butadiene-styrene (ABS) plastics, in which a polybutadiene or poly(butadiene-co-acrylonitrile) rubber toughens a poly(styrene-co-acrylonitrile) glassy phase. More complete discussions of these two-phase polymer systems are available elsewhere [7, 8].
18.4.2 Fillers [9]
Fillers are particulate materials whose major function often is simply to extend the polymer and thereby reduce the cost of the plastic compound. Fillers can take up a substantial portion of the volume of polymeric products (often approaching 50%), particularly for items where low cost is more important than product performance. One of the earliest examples of a filler is the wood flour (fine sawdust) long used in phenolic polymers and other thermosets. Calcium carbonate is used in a variety of plastics and polypropylene is often filled with talc. Even water has been used to extend polyester casting compounds.
Fillers may also be used to improve certain properties of the compound. Almost all of them reduce mold shrinkage and thermal expansion coefficients. They reduce warping in molded parts. Mica and other fillers can increase heat resistance. Hollow glass or phenolic microspheres reduce the density of the composite. Conductive fillers, such as certain carbon blacks and aluminum flake, impart electrical conductivity that bleeds off static charge (important in car tires) and provides plastics with electromagnetic interference (EMI) shielding capability. Just about any filler whose hardness and modulus are greater than those of the polymer will increase the hardness and initial modulus of a mixture with the polymer, but generally, elongation, ultimate strength, toughness, and processability suffer.
18.4.3 Coupling Agents
For a reinforcing fiber, such as glass, to be of maximum benefit (or a filler not to be too detrimental to mechanical properties), stress must be efficiently transferred from the polymer to the reinforcing agent or the filler. Unfortunately, most inorganics have hydrophilic surfaces, while most polymers are hydrophobic, so interfacial adhesion is poor. This problem is exacerbated by the tendency of the surface of many inorganics (particularly glass) to adsorb water, which further degrades adhesion by reducing the amount of hydrogen bonds between the fibers and the polymer. Coupling agents are intended to help overcome these difficulties.
The most common coupling agents are silanes, with the general formula YRSi(OR′)3. The (OR′) group reacts with the inorganic substrate and the Y group reacts (or at least forms strong secondary bonds) with the polymer, thereby enhancing interfacial adhesion. The reaction sequence by which vinyl-triethoxysilane is believed to couple to a substrate containing hydroxyl surface functionality (e.g., glass) is shown below.
The “dangling double bonds” so introduced can then participate in the cure of an unsaturated polyester resin (Example mprb2.3), covalently bonding the polymer to the surface.
A wide variety of silane coupling agents is available, with the functional groups optimized for use with various polymers and substrates. Titanate coupling agents perform in a similar fashion. Fillers and reinforcing fibers are supplied pretreated with coupling agent or the agent may be added during compounding (in which case, presumably most of it migrates, or blooms, to the interface).
In the case of fillers, coupling agents have an added benefit. By converting an otherwise hydrophilic surface to a hydrophobic surface, compatibility with the polymer is improved. This results in easier and more uniform dispersion of the filler in the polymer, and at a given filler, loading can reduce the viscosity substantially, thereby improving processability.
Graft and block copolymers often perform a coupling function in the case of rubber-toughened plastics mentioned in the discussion of reinforcing agents. In the manufacture of high-impact polystyrene, for example, the polybutadiene is dissolved in the polymerizing styrene monomer. As a result, some of the styrene is grafted to the rubber. The grafted polystyrene chains are physically compatible with the surrounding homopolystyrene and are chemically bound to the rubber, thereby enhancing adhesion between the dispersed polybutadiene particles and the polystyrene matrix. The graft copolymer is thought to be essential for effective impact enhancement in this particular system, because simple mechanical blends of polystyrene and polybutadiene tend to be less homogeneous and show little impact enhancement. However, minor amounts of styrene–butadiene block copolymers do act as compatibilizers and, therefore, improve the impact strength of such blends, much as a soap or a surfactant that emulsifies oil in water.
18.4.4 Stabilizers
Most polymers are susceptible to one or more forms of degradation, usually as a result of environmental exposure to oxygen or ultraviolet (UV) radiation, or to high temperatures during processing operations. Stabilizers inhibit degradation of the polymer. In the case of poly(vinyl chloride), for example, the major product of thermal degradation is HCl, which, besides being a strong acid, catalyzes further degradation. Compounds such as metal oxides, which react with the HCl to form stable products, are used as stabilizers. Oxidative degradation of polymers is thought to take place by a free-radical mechanism involving crosslinking and/or chain scission initiated by free radicals from peroxides formed in the initial oxidation step. Similarly, these reactions can be initiated by free radicals produced by UV radiation (a serious threat to polymers used in cars, particularly dashboard materials). Stabilizers against such reactions are generally quinone-type organics that are effective free-radical scavengers.
18.4.5 Pigments
Plastics are often colored by the addition of pigments, which are finely divided solids. If the polymer is itself transparent, a pigment imparts opacity. Titanium dioxide is a common pigment where a brilliant, opaque white is desired. Sometimes, pigments perform other functions. For example, calcium carbonate acts as both a filler and a pigment in many plastics, and carbon black is often a stabilizer as well as a pigment. It prevents degradation by absorbing and preventing the penetration of UV light beyond the surface of the material.
18.4.6 Dyes
Dyes are colored organic chemicals that dissolve in the polymer to produce a transparent compound (assuming the polymer is transparent to begin with). Many polycarbonate drinking bottles that are colored, yet transparent, use dyes. Some thermoplastics, though transparent, develop a slight yellow tinge from minor degradation during processing that causes selective absorption of light toward the blue end of the spectrum. The yellow can largely be “canceled out” by the addition of a blue dye that reduces the transmission of yellowish wavelengths. This technique unavoidably results in a slight lowering of the total light transmission.
18.4.7 Plasticizers
The addition of a relatively low molecular weight organic plasticizer (often exceeding 10–20% of the polymer mass) to a normally glassy polymer will progressively reduce its modulus by bringing the compound's glass transition temperature down closer to use temperature. The level at which the modulus is reduced to the point where the compound is considered an elastomer rather than a plastic is somewhat arbitrary, but plastics sometimes contain small amounts of a plasticizer to reduce brittleness. Plasticizers must be thermodynamically compatible with the host polymer to avoid phase separation.
Common plasticizers, such as those based on phthalates or trimellitates, have been used frequently, particularly with poly(vinyl chloride), allowing an otherwise hard material (e.g., drain pipes) to be used in flexible products (e.g., shower curtains or water hoses). Several recent studies showing migration of plasticizers out of materials during their lifetime has led to the development of more stable or less toxic plasticizers, such as citrates that are used in medical plastics (e.g., IV bags and tubing). A recent review paper covers the major uses of common plasticizers and discusses the numerous applications and research trends [10].
18.4.8 Lubricants
External lubricants are low molecular weight organics that are relatively insoluble in the polymer and “plate out” or migrate to the surface of the compound and form a slippery coating during processing operations. They produce smoother extrudates and molded articles, and minimize sticking in the mold by acting as mold release agents. Where subsequent painting or printing of the surface is required, they can reduce adhesion, and so must be used with care. Stearic acid and its metal salts are common external lubricants. Internal lubricants are soluble in the polymer, and ease processing by lowering the compound's viscosity.
18.4.9 Processing Aids
Various compounds (often a second polymer) are used to modify the rheological properties of a polymer during processing to provide higher outputs, better surface finish, and easier handling in general. For example, low molecular weight polyethylene is added to PVC to improve extrusion behavior.
18.4.10 Curing Agents
These are chemicals whose function is to produce a crosslinked, thermosetting plastic from an initially linear or branched polymer. For example, a vinyl monomer, such as styrene, a free-radical initiator, and sometimes a promoter (e.g., cobalt naphthenate, to speed up the reaction) can be dissolved in a low molecular weight unsaturated polyester resin, which forms crosslinks by an ordinary addition mechanism involving the double bonds in the polyester (Example mprb2.3). Curing is also important in forming tires, as sulfur is compounded with natural, butadiene, or isoprene rubber to form a crosslinked rubber.
The polymer for a two-stage thermosetting compound is deliberately produced with a stoichiometric shortage of one of the reagents to give a highly branched, but not yet crosslinked structure, which is later cured in the mold with a curing agent. An “A-stage” phenolic polymer is produced by reacting phenol and formaldehyde in about a 1.25:1 mol ratio (a molal excess of formaldehyde is required for crosslinking). This still-thermoplastic product (a novolac) is compounded with fillers, pigments, reinforcing agents, and a curing agent, hexamethylenetetramine, to give a “B-stage” resin. The curing agent decomposes in the presence of moisture (a product of the condensation reaction) upon heating in the mold, giving the additional formaldehyde required for crosslinking and ammonia which acts as a basic catalyst for the reaction:
Single-stage resins (resoles) are made using the final desired reactant ratio, about 1:1.5 phenol:formaldehyde, but the reaction is stopped short of crosslinking. Crosslinking is completed in the mold without the necessity of a curing agent.
Free-radical initiators (usually organic peroxides) are used as curing agents for saturated thermoplastic polymers. The curing agent must be compounded with the polymer at temperatures low enough to prevent appreciable decomposition to free radicals. The compound is then heated in the mold, producing free radicals that abstract protons from the polymer, leaving unshared electrons on the chains, which combine to form crosslinks:
Sometimes, sulfur or multifunctional vinyl monomers are added to improve crosslinking efficiency by helping to “bridge the gap” (i.e., produce longer crosslinks) between the chains. In this manner, polyethylene is crosslinked with dicumyl peroxide, converting it from a thermoplastic to a thermoset with much greater heat resistance to stress cracking and abrasion. It can also tolerate much higher levels of carbon black filler without becoming excessively brittle.
18.4.11 Blowing Agents
Foamed plastics must contain a material that generates a gas to produce foaming. They are chemical blowing agents (CBAs), which generate gas through a chemical reaction, and physical blowing agents, inert but volatile chemicals that are dissolved in the polymer or its precursors and simply vaporized upon heating or a reduction in pressure. As an example, polyurethanes (Example mprb2.4Q) may be “water blown” by the reaction of excess diisocyanate with water, generating CO2:
This is not often done in practice because of the expense of the diisocyanate and the difficulty in controlling foam structure. Alternatively, they can be foamed with a physical blowing agent, traditionally CCl3F or other chlorofluorocarbons (CFCs). The latter gives excellent control of foam structure and, because of its low thermal conductivity, makes good insulating foams. Unfortunately, it poses a threat to the atmospheric ozone layer and has been phased out for many operations. Carbon dioxide and liquefied gases are among several alternatives to replace the CFCs.
CBAs must be compounded with a polymer below their decomposition temperatures and then decomposed to generate the gas at temperatures low enough to prevent degradation of the polymer. A variety of CBAs is available, covering a range of decomposition temperatures, for use with most common plastics [11, 12].
In the manufacture of polystyrene foam molding beads, pentane is added to the monomer in a suspension polymerization or absorbed by the beads afterward. When the beads are placed in a mold and heated (usually with steam), the pentane volatilizes, expanding the beads against each other and the mold walls. These beads are used in many familiar applications, such as drinking cups, picnic coolers, and packaging peanuts.
18.4.12 Flame Retardants [13–15]
Most synthetic polymers, being composed largely of carbon and hydrogen, are flammable (although no more so than natural materials such as wood and cotton—both natural polymers, which synthetic polymers often replace—a fact sometimes overlooked). Plastics are increasingly being compounded with flame retardants to reduce their flammability. The most common flame-retarding additives for plastics contain large proportions of chlorine or bromine. These elements are believed to quench the free-radical flame propagation reactions. They may be compounds that are simply mixed with the plastic, for example, decabromodiphenyl ether, or they may be reactive monomers that become part of the polymer. Examples of the latter include tetrabromobisphenol-A substituted for some of the normal bisphenol-A in epoxies (Example mprb2.4O) or polycarbonates (Example mprb2.4N) and tetrabromophthalic anhydride used in polyesters (Example mprb2.3). Antimony trioxide is often used in synergistic combination with halogenated compounds. Organic phosphates are thought to function as flame retardants by forming a char that acts as a barrier to flames. A compound such as tris(2,3-dibromopropyl) phosphate combines halogen and phosphate. Poly(vinyl chloride), because of its chlorine content, is inherently flame resistant, but if it is to maintain this valuable property in plasticized form, it must be compounded with halogenated or phosphate plasticizers.
The safety of halogen and antimony flame-retardant systems has been questioned, both the compounds themselves during processing operations and their combustion products. They have largely been replaced with phosphorus-based systems [16]. Hydrated alumina, another alternative, is a particulate filler that contains 35% water of hydration, the evaporation of which absorbs energy and inhibits flame spread.
18.4.13 Miscellaneous
Various other materials are added to plastics to provide certain end-use properties. For example, where a polymer will be subjected to a warm, humid environment (e.g., vinyl shower curtains and silicone-rubber bathtub caulks), it often contains a biocide to inhibit the growth of mold, mildew, and fungus. These biocides are generally organic copper, mercury, nanosilver, or tin compounds. Fatty-acid amines are added to compounds for use in bottles and phonograph records as antistatic agents. These chemicals, because of their limited compatibility with the polymer, migrate (or bloom) to the surface of the material and, because of their polarity, attract moisture from the atmosphere. The moisture bleeds off static electricity charges, which otherwise would attract considerable dust over time. These same fatty-acid amines also function as slip or antiblock agents, which prevent layers of plastic film and sheet from sticking to each other. Nucleating agents, which promote more but smaller crystallites, were discussed in Chapter 4.
18.5 Sheet Molding Compound for Plastics
The subject of sheet molding compound (SMC) is introduced here because: (1) they are commercially important, (2) they make use of many of the additives discussed in the previous section, and (3) they do not seem to fit logically anywhere else. Sheet molding compounds provide a high strength-to-weight ratio, with low cost and easy, rapid processing. SMCs are easily-moldable polymer composites that are formed into sheets with a curing agent included (which is activated during a delayed molding step). They are used for automotive body parts such as front ends and fender extensions and for other structural parts in such items as business copy machines and air-conditioner hosings. They, along with RIM polyurethanes and polyureas and injection-molded thermoplastics, are in the competition for increased use in auto body panels (doors, hoods, fenders, etc.).
SMCs consist mainly of unsaturated polyester resin (Example mprb2.3), filler (usually CaCO3), and chopped-glass reinforcing fiber. Early SMCs contained roughly a third of each, but newer materials are closer to 25% resin, 30% glass, and 45% filler [17]. The liquid polyester and filler are compounded in a high-shear mixer along with minor amounts of a curing agent (usually an organic peroxide), a thickener (MgO or CaO), an external lubricant as a mold-release agent (zinc stearate), and sometimes a low-shrink additive.
The material leaves the mixer looking (but not smelling) like pancake batter, and is spread continuously onto layers of polyethylene film (Figure 18.4). Chopped glass fibers (about 1 in long) are sprinkled on, the layers are combined, and the sheet is kneaded by rollers to wet out the glass. The sheet is then rolled up and allowed to age, which during time. The thickens to the consistency of cardboard. This thickening is believed to involve interaction of the MgO or CaO with the carboxylic acid groups on the polyester, with water also playing a role, but it is not a true polymerization.
Figure 18.4 Sheet molding compound line.

Before use, the sheets are cut to size and the polyethylene stripped off. They are then placed in a heated compression-type mold (several layers may be stacked for greater thicknesses) where true cure (crosslinking) of the polyester takes place.
The choice of a curing agent for a SMC involves a compromise between an active initiator, which will give quick cures, but conversely, imparts a short shelf life to the stored SMC, and a less active initiator with a longer shelf life but slower cure. A drawback of early SMCs was the wavy surface and sometimes visible glass-fiber texture produced by shrinkage of the polyester during cure. This necessitated hand-finishing operations, which are not at all popular in the automotive industry. The low-shrink additives that counteract this usually involve a second, linear polymer dissolved in the polyester, which precipitates out as a micrometer-sized dispersed phase as the polyester cures. Why this should reduce shrinkage is not at all clear, but if the low-shrink additive is a rubber, it may act as a toughening agent as well (see Section 4.1).
Bulk molding compounds (BMCs) are similar in composition to SMCs, with somewhat shorter fibers (¼ to ½ in), and perhaps less glass (15%) and more filler. They are produced in chunk form and compression molded like other thermosetting compounds.
18.6 Plastics Recycling
The recycling and reuse of plastics is important for both environmental and monetary reasons. Just as metals are separated prior to recycling, polymers must be separated as well. Typical recycling symbols indicate which type of plastic an item is made from (Figure 18.5). The additives covered in the chapter make recycling difficult, as they are generally well-mixed with the polymer host, and thermodynamically difficult to remove. Some plastics are copolymers or blends of polymers that can also be challenging to recycle. Impurities (i.e., the additives) can significantly alter the properties of a material, and most of the reprocessing methods used to make new products from recycled plastics reduce the molecular weight of the materials. Thus, recycled plastics do not find many uses in products requiring high mechanical strength or that have a narrow range of acceptable properties. The U.S. Food and Drug Administration requires the use of virgin plastic materials for linings that touch a food product, thus recycled plastics are limited to outer packaging for food applications. One reason for this is the potential for harmful chemicals or bacteria to find their way into the void space of the original material. Recycled plastics more often than not are used in lower-end products like garbage bags and park benches.
Figure 18.5 Plastic recycling symbols for (1) poly(ethylene terephthalate), (2) high density polyethylene, (3) vinyl polymers, (4) low density polyethylene, (5) polypropylene, (6) polystyrene, and (7) all other polymers.

The recycling process normally involves several steps of chopping, grinding, and melting to form pellets, similar to those used for the original hopper feed for thermoplastic processing. Thermosets, on the other hand, cannot be reprocessed by melting without degrading the material, so after chopping, they are generally used only as filler material.
Problem
1. Seymour, R.B. (ed.), Additives for Plastics, Vol. 1, State of the Art, Vol. 2, New Developments, Academic, New York, 1978.
2. Greek, B.F., Chem. Eng. News, June 13, 1988, p. 35.
3. Milewski, J.V. and H.S. Katz (eds), Handbook of Reinforcements for Plastics, Elsevier, New York, 1987.
4. Sandler, J., P. Werner, M.S.P. Shaffer, V. Demchuk, V. Altstadt, and A.H. Windle, Composites- Part A: Appl. Sci. Manufac. 33, 1033 (2002).
5. Clegg, D.W. and A.A. Collyer (eds), Mechanical Properties of Reinforced Thermoplastics, Elsevier, New York, 1986.
6. Kline, G.M., Modern Plastics Encyclopedia McGraw-Hill, New York, 1990.
7. Rosen, S.L., Trans. N.Y. Acad. Sci. 35(6), 480 (1973).
8. Riew, C.K. (ed.), Rubber-Toughened Plastics, American Chemical Society, Washington, DC, 1989.
9. Katz, H.S. and J.V. Milewski (eds), Handbook of Fillers for Plastics, Elsevier, New York, 1987.
10. Rahman, M. and C.S. Brazel, Prog. Polym. Sci. 29, 1223 (2004).
11. Heck, R.L., III, Plast. Compd., November/December 1978, p. 52.
12. Hallans, R.S., Plast. Eng., December 1977, p. 17.
13. Schongar, L.H., Plast. Compd., May/June 1978, p. 44.
14. Blake, W.P., Plast. Compd., July/August 1978, p. 26.
15. Nametz, R.C., Plast. Compd., January/February 1979, p. 31.
16. Wood, S.A., Mod. Plast. 67(5), 40 (1990).
17. Wigotsky, V., Plast. Eng. 47(6), 8 (1991).