Chapter 19
Polymer Applications: Rubbers and Thermoplastic Elastomers
19.1 Introduction
A rubber is generally defined as a material that can be stretched to at least twice its original length, and that will retract rapidly and forcibly to substantially its original dimensions on release of the force. In contrast, an elastomer is a rubber-like material from the standpoint of modulus but one that has limited extensibility and incomplete retraction. The most common example is highly plasticized poly(vinyl chloride).
Rubber has the following characteristics. (1) From the molecular standpoint, a rubber must be a high molecular weight polymer, since rubber elasticity is mainly due to the coiling and uncoiling of long chain segments (Chapter 13). (2) For the molecules to be able to coil and uncoil freely, the glass-transition temperature of the polymer must be above its use temperature. (3) Furthermore, the polymer must be amorphous in its unstretched state because crystallinity would hinder coiling and uncoiling. (4) There used to be an additional requirement that the polymer be crosslinked (although physical entanglements act as effective crosslinks). If it were not crosslinked, the chains would slip past one another (undergo viscous flow) under stress and recovery would be incomplete; however, if they were chemically crosslinked, they would be thermosets rather than thermoplastics.
19.2 Thermoplastic Elastomers [1, 2]
The introduction of the so-called thermoplastic elastomers (actually rubbers) has gotten around the requirement for crosslinking in the strictest sense, that of covalent bonding between chains. They are commonly found for applications requiring flexibility in automotives, household appliances, and soft-grip tools. The most common thermoplastic elastomers are styrene-b-butadiene-b-styrene (SBS) block copolymers produced in solution by anionic polymerization (Example mprb10.1). Since most polymer pairs are mutually insoluble, the polystyrene chain ends aggregate together in microscopic domains. These polystyrene domains, being below their glass transition temperature (100 oC) at normal use temperatures, are rigid and act to tie together the long, flexible polybutadiene segments (which are above their Tg at normal use temperature) as do ordinary crosslinks. Unlike the usual covalent crosslinks, however, the polystyrene domains soften above the Tg of polystyrene, and the polymer behaves as a true thermoplastic.
All thermoplastic elastomers have in common a continuous rubbery phase of “soft segments” tied together by glassy or crystalline “hard segments” at use temperature, which soften at elevated temperatures. Thus, thermoplastic elastomers do not have to be vulcanized and can be processed by the usual economical thermoplastic techniques.
19.3 Contents of Rubber Compounds
Natural rubber and, with a few exceptions, the many synthetic rubber polymers commercially available are unsaturated; that is, they contain double bonds that provide sites for vulcanization (crosslinking) reactions. The polymers are mostly linear or branched, but some also contain (either intentionally or unintentionally) minor amounts of gel (crosslinked particles) prior to vulcanization. This can have a profound effect on processing properties [3, 4]. The following substances are often included in rubber compounds.
19.3.1 Reinforcing Fillers
Most rubber compounds that are intended to develop a reasonable tensile strength, abrasion, and tear resistance will contain up to 50 phr (parts per hundred parts rubber by weight) or more of a reinforcing filler, nearly always a carbon black (thus the color of car tires). The use of carbon black in rubbers is quite different than in plastics, where it is strictly a pigment and limited to much lower loadings.
Carbon blacks are not simply carbon. Basic blacks have hydroxyl groups at the particle surfaces and acid blacks have carboxylic acid functionality. It has been shown that the rubber polymer forms strong secondary and primary covalent bonds with the carbon black, which accounts for its reinforcing ability. A wide variety of carbon blacks is available [5]. In addition to chemical functionality, they differ in factors such as particle size, degree of aggregation, and surface area, and different types of rubber polymers require particular kinds of black for optimum reinforcement. Silicone rubbers are sometimes reinforced with finely divided silica (SiO2).
Natural rubber (cis-1,4-polyisoprene) and its synthetic counterpart and butyl rubber are among the few rubber polymers that can develop reasonable mechanical strength without reinforcement. This is because (especially for natural rubber that has a regular tacticity) they crystallize with molecular orientation at high elongations and the crystallites function as a reinforcing agent, causing the sharp upturn in the stress–strain curves at high elongations shown in Figure 19.1 [6].
Figure 19.1 Stress–strain curves for filled and unfilled rubber vulcanizates [6]. Used with permission of McGraw-Hill Book Company.
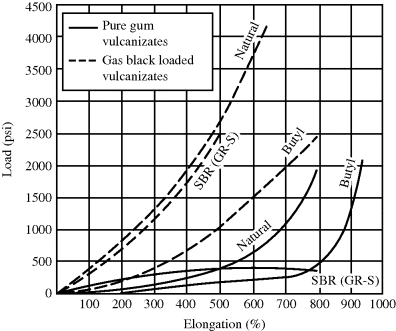
19.3.2 Fillers
As with plastics, the function of fillers in rubber is mainly to reduce the cost of the compound. Most rubber fillers are finely divided inorganics such as CaCO3. The addition of such high modulus fillers raises the modulus (stiffens the compound), though too much will cause a loss of rubbery properties, all other things being equal. Carbon blacks sometimes perform as fillers and as reinforcing agents in rubber compounds.
19.3.3 Extending Oils
Hydrocarbon oils are often used in rubber compounds. Their function is twofold. First, they plasticize the polymer, making it softer and easier to process. This is particularly important with very high molecular weight polymers. Second, since they are usually cheaper than the rubber polymer, they act like fillers in reducing the cost of the compound. Extending oils are available in various degrees of aromaticity and the properties of the compound depend on the type of oil in relation to the polymer as well as oil level.
Carbon black and extending oils have opposite effects on the modulus of a rubber compound. One trick for producing low-cost compounds from synthetic polymers is to polymerize to higher-than-normal molecular weight. The modulus is cut down by the addition of an extending oil and then brought back up to the desired level by the addition of large amounts of black. With these ever-increasing levels of black and oil in rubber compounds, it appears that there soon will not be any polymer left! Seriously, there is a limit to this technique, because other properties are soon excessively degraded.
19.3.4 Vulcanizing or Curing Systems
The function of these is to crosslink the polymer. The most common curing systems are based on sulfur. Although sulfur alone can cure unsaturated rubbers upon heating, the process is slow and inefficient in its use of sulfur. The mechanisms of sulfur curing are not well understood, but are thought to include (among other things) the formation of sulfide or disulfide links between chains and the abstraction of protons from adjacent chains to form H2S, with the chains crosslinking at the remaining unshared electrons.
To speed up the vulcanization process, accelerators are generally used. These are usually complex sulfur-containing organic compounds, often of proprietary composition. Promoters or activators are used to improve the cure still further. Zinc oxide is a common example, particularly in conjunction with stearic acid.
Nonsulfur cures are used occasionally. Free-radical initiators can provide crosslinks, as discussed in Section 18.4, and zinc oxide can crosslink polymers that contain chlorine.
19.3.5 Antioxidants or Stabilizers
These are particularly important with natural rubber and the many synthetic rubbers that contain a major proportion of butadiene or isoprene. These polymers are highly unsaturated and the double bonds are extremely susceptible to attack by oxygen and ozone, resulting in embrittlement, cracking, and general degradation. Since the degradation reactions take place by free-radical mechanisms, antioxidants work by scavenging free radicals.
19.3.6 Pigments
Where great mechanical strength is not required, and thus carbon black not used, rubbers can be colored with pigments, just as plastics. A typical radial passenger-tire tread formulation is shown in Table 19.1. Notice that the additives (everything except SBR polymer and cis-polybutadiene) make up 122.25 parts per hundred parts polymer or more than half of the tire!
Table 19.1 Radial Passenger-Tire Tread Formulation.
Ingredient | phra | Function |
SBR 1712b | ||
Polymer | 45 | Rubber polymer |
Aromatic oil | 37.5 | Extending oil |
cis-Polybutadiene 1252 | 55 | Rubber polymer |
Carbon black N-234 | 70 | Reinforcing agent |
Oil-soluble sulfonic acid | 1 | Processing aid |
Sulfur | 1.75 | Vulcanizing agent |
Stearic acid | 2 | Promotor |
Zinc oxide | 3 | Promotor |
N-Cyclohexyl-2-benzotliiazole sulfenamid | 1 | Accelerator |
Polymerized 1,2-dihydrotrimethylquinoline | 2 | Antioxidant |
N-(l,3-dimethylbutyl)-N′-Phenyl-p-phenylene diamine | 1 | Antiozonant |
Blended petroleum wax | 3 | Crack inhibitor and antiozonant |
Total | 222.25 | |
aParts per hundred parts rubber, by weight. | ||
bOil-extended master batch. Cold emulsion polymer ≈75% butadiene, 25% styrene extended with highly aromatic oil. | ||
Source. H. L. Stephens [7]. |
19.4 Rubber Compounding [7, 8]
The ingredients added to a rubber (such as those in Table 19.1) must be compounded with the rubber polymer to produce the final rubber compound for molding, extrusion, etc. This is usually done in two-roll mills or Banbury mills (Chapter 17). Both devices are driven by relatively large electric motors and put a lot of energy per unit time and volume into the polymer. This energy input serves two purposes. First, it breaks down the polymer and reduces its “nerve” to the point where it can be easily compounded and processed. Nerve is a term used to describe the difficult-to-handle highly elastic response caused by a molecular weight too high. This mastication step mechanically degrades the polymer, lowering its molecular weight and, therefore, increasing its viscous response. Premastication is particularly important with natural rubber, since its molecular weight cannot be controlled during polymerization. Second, the high energy input breaks up and disperses the compounding ingredients evenly throughout the polymer.
1. Legge, N.R., G. Holden, and H.E. Schroeder (eds), Thermoplastic Elastomers, Hanser, Munich, Germany, 1987.
2. Walker, B.M., and C.P. Rader (eds), Handbook of Thermoplastic Elastomers, 2nd ed., Van Nostrand-Reinhold, New York, 1988.
3. Rosen, S.L. and F. Rodriguez, J. Appl. Polym. Sci. 9, 1601 (1965).
4. Rosen, S.L. and F. Rodriguez, J. Appl. Polym. Sci. 9, 1615 (1965).
5. Byers, J.T., Fillers, Part I: Carbon black, Chapter 3 in Rubber Technology, 3rd ed., M. Morton (ed.), Van Nostrand-Reinhold, New York, 1987.
6. Schmidt, A.X. and C.A. Marlies, Principles of High Polymer Theory and Practice, McGraw- Hill, New York, 1948, p. 537.
7. Stephens, H.L., The compounding and vulcanization of rubber, Chapter 2 in Rubber Technology, 3rd ed., M. Morton (ed.), Van Nostrand-Reinhold, New York, 1987.
8. Barlow, F.W., Rubber Compounding, Principles, Materials and Techniques, Dekker, New York, 1988.