This chapter is dedicated to contacts between a rigid, rotationally symmetric indenter and an elastic half-space, which are subjected to a twisting moment along the z-axis in the normal direction of the half-space. The fundamental equations of elastostatics exhibit an interesting property; that purely torsional problems are generally elastically decoupled in cases of rotational symmetry. This means that the tangential displacements in no way affects the radial and normal displacements. (Note regarding the notation in this chapter: contrary to the previous chapter, the word “tangential” refers to “circumferential direction” in this chapter. With this in mind, all tangential displacements will be denoted by u with the corresponding index of the tangential direction, i.e.,
,
,
, etc. Normal displacements will retain the notation w.) However, in spite of the elastic decoupling, there exists the coupling caused by friction. We initially consider contacts without slip, which accordingly are decoupled from the normal contact problem, and we subsequently examine finite coefficients of friction.
5.1 No-Slip Contacts
5.1.1 The Cylindrical Flat Punch




![$$\begin{aligned}\displaystyle\sigma_{\varphi z}(r)&\displaystyle=-\frac{4G\varphi}{\pi}\frac{r}{\sqrt{a^{2}-r^{2}}},\quad r\leq a,\\ \displaystyle u_{\varphi}(r)&\displaystyle=\frac{2}{\pi}\varphi\left[r\arcsin\left(\frac{a}{r}\right)-a\sqrt{1-\frac{a^{2}}{r^{2}}}\right],\quad r> a,\end{aligned}$$](../images/459405_1_En_5_Chapter/459405_1_En_5_Chapter_TeX_Equ2.png)
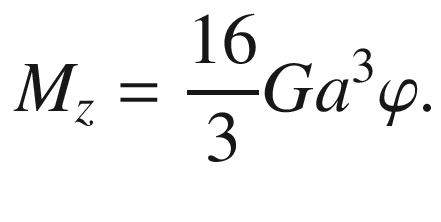

Torsional contact between a rigid flat punch and an elastic half-space

Normalized torsional stresses as a function of the radial coordinate for torsion by a flat cylindrical punch

Normalized tangential displacements as a function of the radial coordinate for torsion by a flat cylindrical punch
5.1.2 Displacement from Torsion by a Thin Circular Ring



![$$\begin{aligned}\displaystyle u_{x}&\displaystyle=\frac{F_{x}}{2\pi G}\left[\frac{1}{s}\left(1-\nu\right)+\nu\frac{x^{2}}{s^{3}}\right],\\ \displaystyle u_{y}&\displaystyle=\frac{\nu F_{x}}{2\pi G}\frac{xy}{s^{3}},\end{aligned}$$](../images/459405_1_En_5_Chapter/459405_1_En_5_Chapter_TeX_Equ5.png)
![$$\begin{aligned}\displaystyle u_{\varphi}(r;a)&\displaystyle=\frac{1}{2\pi G}\int_{0}^{2\pi}\frac{M_{z}}{2\pi a}\frac{\cos\varphi\mathrm{d}\varphi}{\sqrt{a^{2}+r^{2}-2ar\cos\varphi}}\\ \displaystyle&\displaystyle=\frac{M_{z}}{2\pi^{2}Ga^{2}}\left[\frac{r^{2}+a^{2}}{r^{2}+ar}\mathrm{K}\left(\frac{2\sqrt{ra}}{r+a}\right)-\frac{(r+a)^{2}}{r^{2}+ar}\mathrm{E}\left(\frac{2\sqrt{ra}}{r+a}\right)\right],\end{aligned}$$](../images/459405_1_En_5_Chapter/459405_1_En_5_Chapter_TeX_Equ6.png)
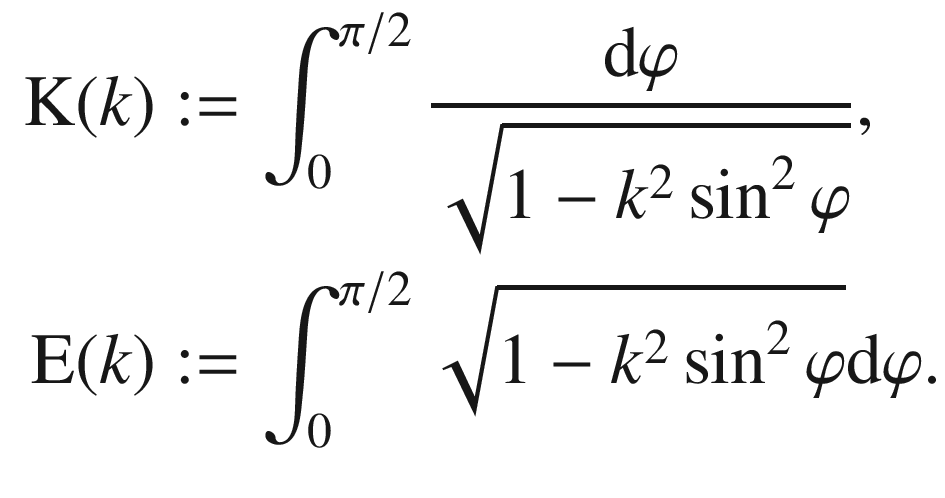

Tangential displacement of the surface from torsion by a thin circular ring
5.2 Contacts with Slip
















![$$\begin{aligned}\displaystyle M_{z}(c,a)&\displaystyle=16G\left(\varphi\frac{c^{3}}{3}+\int_{c}^{a}x^{2}\tilde{\phi}(x,a)\mathrm{d}x\right)\\ \displaystyle&\displaystyle=16G\varphi\frac{c^{3}}{3}-4\mu\int_{c}^{a}\left[c\sqrt{r^{2}-c^{2}}+r^{2}\arccos\left(\frac{c}{r}\right)\right]\sigma_{zz}(r)\mathrm{d}r,\end{aligned}$$](../images/459405_1_En_5_Chapter/459405_1_En_5_Chapter_TeX_Equ12.png)

![$$u_{\varphi}(r)=r\left[\varphi-\frac{4}{\pi r^{2}}\int_{c}^{r}x^{2}\left[\varphi-\tilde{\phi}(x;a)\right]\frac{\mathrm{d}x}{\sqrt{r^{2}-x^{2}}}\right],\quad c<r\leq a.$$](../images/459405_1_En_5_Chapter/459405_1_En_5_Chapter_TeX_Equ14.png)


5.2.1 The Cylindrical Flat Punch






![$$\begin{aligned}\displaystyle\varphi&\displaystyle=\frac{\mu E^{*}d}{2\pi Ga}\mathrm{K}\left(\sqrt{1-\frac{c^{2}}{a^{2}}}\right),\\ \displaystyle M_{z}&\displaystyle=16G\varphi\frac{c^{3}}{3}+\frac{8\mu E^{*}d}{\pi a}\int_{c}^{a}x^{2}\mathrm{K}\left(\sqrt{1-\frac{x^{2}}{a^{2}}}\right)\mathrm{d}x,\\ \displaystyle\sigma_{\varphi z}(r)&\displaystyle=-\frac{4Gr}{\pi}\left[\int_{c}^{a}\frac{\mathrm{d}\tilde{\phi}(x,a)}{\mathrm{d}x}\frac{\mathrm{d}x}{\sqrt{x^{2}-r^{2}}}+\frac{\tilde{\phi}\left(a,a\right)}{\sqrt{a^{2}-r^{2}}}\right],\quad r\leq c\\ \displaystyle&\displaystyle=-\frac{2\mu E^{*}dr}{\pi^{2}a}\\ \displaystyle&\displaystyle\quad{}\cdot\Bigg\{\int_{c}^{a}\left[x\mathrm{K}\left(\sqrt{1-\frac{x^{2}}{a^{2}}}\right)-\frac{a^{2}}{x}\mathrm{E}\left(\sqrt{1-\frac{x^{2}}{a^{2}}}\right)\right]\frac{\mathrm{d}x}{\left(a^{2}-x^{2}\right)\sqrt{x^{2}-r^{2}}}\\ \displaystyle&\displaystyle\qquad{}+\frac{\pi}{2\sqrt{a^{2}-r^{2}}}\Bigg\},\end{aligned}$$](../images/459405_1_En_5_Chapter/459405_1_En_5_Chapter_TeX_Equ18.png)



Torsion angle, normalized to the critical value for complete stick, as a function of the normalized radius of the stick zone for the torsional contact with a flat punch

Torsional moment, normalized to the critical value for complete stick, as a function of the normalized radius of the stick zone for the torsional contact with a flat punch

Torsional stresses normalized to the average pressure multiplied with the coefficient of friction
for the torsional contact with a flat cylindrical punch. The thin solid line represents the stress distribution for complete slip

Normalized tangential displacements for the torsional contact with a flat cylindrical punch. The thin solid line represents the displacement caused by the rigid body rotation
5.2.2 The Paraboloid





![$$\tilde{\phi}(x;a)=\frac{\mu E^{*}a}{\pi GR}\left[\mathrm{K}\left(\sqrt{1-\frac{x^{2}}{a^{2}}}\right)-\mathrm{E}\left(\sqrt{1-\frac{x^{2}}{a^{2}}}\right)\right],$$](../images/459405_1_En_5_Chapter/459405_1_En_5_Chapter_TeX_Equ23.png)

![$$\begin{aligned}\displaystyle\varphi&\displaystyle=\frac{\mu E^{*}a}{\pi GR}\left[\mathrm{K}\left(\sqrt{1-\frac{c^{2}}{a^{2}}}\right)-\mathrm{E}\left(\sqrt{1-\frac{c^{2}}{a^{2}}}\right)\right],\\ \displaystyle M_{z}&\displaystyle=16G\varphi\frac{c^{3}}{3}\\ \displaystyle&\displaystyle\quad{}+\frac{16\mu E^{*}a}{\pi R}\int_{c}^{a}x^{2}\left[\mathrm{K}\left(\sqrt{1-\frac{x^{2}}{a^{2}}}\right)-\mathrm{E}\left(\sqrt{1-\frac{x^{2}}{a^{2}}}\right)\right]\mathrm{d}x,\\ \displaystyle\sigma_{\varphi z}(r)&\displaystyle=-\frac{4\mu E^{*}ar}{\pi^{2}R}\int_{c}^{a}\mathrm{E}\left(\sqrt{1-\frac{x^{2}}{a^{2}}}\right)\frac{\mathrm{d}x}{x\sqrt{x^{2}-r^{2}}},\quad r\leq c.\end{aligned}$$](../images/459405_1_En_5_Chapter/459405_1_En_5_Chapter_TeX_Equ25.png)




Torsional contact between a rigid paraboloid and an elastic half-space

Normalized torsion angle as a function of the normalized radius of the stick zone for the torsional contact with a parabolic indenter

Normalized torsional moment as a function of the normalized radius of the stick zone for the torsional contact with a parabolic indenter

Torsional stresses normalized to the average pressure multiplied by the coefficient of friction
for the torsional contact with a flat cylindrical punch. The thin solid line represents the stress distribution for complete slip

Normalized tangential displacements for the torsional contact with a parabolic indenter. The thin solid line represents the displacement caused by the rigid body rotation
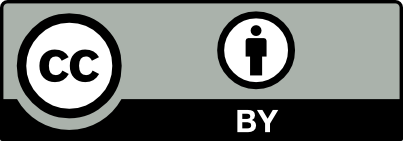
Open Access This chapter is licensed under the terms of the Creative Commons Attribution 4.0 International License (http://creativecommons.org/licenses/by/4.0/), which permits use, sharing, adaptation, distribution and reproduction in any medium or format, as long as you give appropriate credit to the original author(s) and the source, provide a link to the Creative Commons license and indicate if changes were made.
The images or other third party material in this chapter are included in the chapter's Creative Commons license, unless indicated otherwise in a credit line to the material. If material is not included in the chapter's Creative Commons license and your intended use is not permitted by statutory regulation or exceeds the permitted use, you will need to obtain permission directly from the copyright holder.