Introduction
The overall quality of commercial copper sulphide concentrates has steadily decreased over time, with higher levels of contaminants, such as As, Hg, Sb and Bi, and lower copper and sulphide sulphur concentrations. With ever tightening environmental emission standards, lower quality concentrates impose a significant strain on the off-gas handling facilities in smelting operations, while import/export restrictions on such concentrates make the marketing of concentrates with an arsenic concentration greater than 0.5% difficult. The management of impurities, and in particular arsenic, is increasingly important to large copper producers, particularly as they enter into more complex ore zones to extend the lives of their operations.
Hydrometallurgical treatment represents a potential alternative for the processing of arsenical copper concentrates, as it offers the prospect of both eliminating gaseous emissions and producing environmentally stable arsenic solids, while generating acid that can be used in existing heap leach operations.
Background
Sherritt has evaluated the hydrometallurgical recovery of copper from sulphide concentrates since the 1960s [1–4], including from arsenical copper concentrates [5, 6], as have other parties. Despite such efforts, pressure oxidative leaching of copper concentrates has so far not found a distinct area of application on a par with pyrometallurgical refining, with clear economic or process advantages that are generally valid across the industry. It has however been operated commercially [7], with high copper recoveries. Precious metals do not leach to an appreciable extent during pressure leaching in the sulphate system, and may be recovered from the leach solids. Leach residues have generally been found to be environmentally stable, as tested by the TCLP procedure, and arsenic, when present in the pressure leach feed, has been reported to deport largely to the stable leach residue [6].
Minimize gaseous emissions. Using pressure oxidation, gaseous emissions of sulphur dioxide or arsenic are negligible. Legal and regulatory emissions restrictions are therefore less of a factor than in the permitting of pyrometallurgical projects;
High copper recoveries from arsenical concentrates and other arsenical materials, such as metallurgical dusts and waste solutions, while fixing their arsenic content as a stable leach residue;
Pregnant leach solution (PLS) has to be integrated with solvent extraction/electrowinning (SX/EW) operations, and in doing so, its acid content can be valorised in heap leach operations; and
Precious metals, present in the pressure leach feed materials, can be recovered by cyanidation of the pressure leach solids.
With the recovery of sulphuric acid at a strength suitable for heap leaching, precious metals recovery, negligible generation of gaseous emissions and the absence of hazardous waste products, such as metallurgical dust, pressure leaching presents an interesting alternative to conventional, pyrometallurgical process technology.
Pressure oxidative leaching produces PLS with relatively high copper and free acid concentrations. In order for the acid and copper concentrations in PLS to be brought within ranges required for SX/EW, neutralization and/or dilution of the autoclave process PLS before solvent extraction would be required, such as described in patents by Placer Dome [8], now Barrick, and Phelps Dodge [9], now Freeport.
For pressure leaching of sulphide concentrates, three main temperature ranges are reported in the literature: low temperature (90–120 °C), such as the Activox process [10], medium temperature (150–160 °C), such as the Dynatec [3] or CESL [11] processes, and high temperature (>200 °C), such as practised by Freeport [7]. At higher temperatures, sulphide is fully oxidized to sulphate, while elemental sulphur is generated at lower temperatures:
Elemental sulphur tends to react with cyanide during gold/silver recovery, increasing reagent costs. Also, leach residues containing significant amounts of elemental sulphur have as yet not been proven to be environmentally stable over long periods of time on an industrial scale, in respect of their potential for acid generation and/or releaching of arsenic compounds produced under pressure leaching conditions. Naturally, elemental sulphur formation also leads to a lower yield of acid from the leaching process.
Because of the concerns around long term residue stability and the desire to recover precious metals by cyanidation and generate acid for heap leaching, high temperature pressure leaching conditions were selected for this test program, with process parameters set to simulate the operation of a commercial autoclave, to leach copper from the feed materials and to fix the arsenic as an environmentally stable residue.
Feed Materials
Feed analyses
Analysis, wt% | Analysis, g/t | |||||||||
---|---|---|---|---|---|---|---|---|---|---|
Al | As | Cu | Fe | Pb | Si | S2− | Zn | Au | Ag | |
Concentrate 1 | 0.71 | 1.10 | 25.6 | 24.2 | 0.10 | 3.01 | 35.3 | 3.04 | 1.39 | 158 |
Concentrate 2 | 1.20 | 5.61 | 32.0 | 14.8 | 0.05 | 3.52 | 29.5 | 2.08 | 0.59 | 470 |
Metallurgical Dust | 5.06 | 8.34 | 22.3 | 9.99 | 0.10 | 11.1 | 4.66 | 0.53 |
Copper in the first concentrate was primarily present as chalcopyrite (CuFeS2), with lesser quantities of enargite (Cu3AsS4), covellite (CuS) and bornite (Cu5FeS4), while the second concentrate contained copper primarily as enargite and tennantite (Cu12As4S13), with lesser quantities of chalcopyrite. Pyrite was present in significant quantities in both concentrates. Copper in the metallurgical dust was mainly present as chalcocite (Cu2S) and copper sulphate. Almost 19% of the overall dust, and about 65% of its arsenic content, was water soluble, presumably in the form of arsenic trioxide.
The process water used throughout the test work was made up to correspond with locally available water, containing 1.5 g/L chloride, using chloride salts. An acid plant effluent containing 13.0 g/L arsenic and 22.9 g/L H2SO4 was also tested, at up to 16% of process water requirements.
Experimental
Batch pressure leach test work was conducted in 4 L autoclaves. Various compositions of feed solids, including both concentrates and/or the arsenic dust described above, and quench solutions (process water and acid plant effluent) were tested over a range of operating temperatures (200–230 °C) to select the conditions for pilot plant testing. The pressure leach tests generally included collection of multiple samples at pre-determined time intervals to allow generation of rate curves, as well as a “conditioning” sample at the end of each test to evaluate expected changes in slurry composition in commercial pressure letdown and holding vessels. Feed pulp solids contents were selected so as to correspond with commercial, autothermal autoclave operation.

Pilot plant testing arrangement
The autoclave was operated continuously, with high pressure oxygen added for sulphur oxidation and process water added for temperature control. Samples of the final thickener underflow were tested for environmental stability using the Toxicity Characteristic Leaching Procedure (TCLP).
At the end of the pilot plant campaign, selected samples of pressure leach discharge slurry and final thickener underflow were taken and treated for gold and silver recovery, both by direct cyanidation and by cyanidation after lime boil pretreatment of the solids.
Results and Discussion
Copper Extraction
An early finding of the batch pressure leach tests was that copper extraction from various feed blends was typically lower than sulphide oxidation, and the difference was more pronounced with increasing levels of arsenic in the feed. This was believed to be due to the formation of (basic) copper arsenate precipitates during leaching. Kinetic sampling during batch and pilot plant testing indicated that these copper phases form relatively early in the leaching process. Once formed, these compounds are stable under acidic conditions at atmospheric pressures and temperatures, such that hot curing of pressure leach residues, while showing dissolution of iron phases, did not result in appreciable copper dissolution. Copper extraction was relatively consistent for a given feed blend, regardless of the leaching temperature (200–230 °C), indicating that the formation of copper arsenates does not depend significantly on temperature, but rather on the amount of arsenic and iron in the feed solids and solution.

Copper extraction in pressure oxidative leaching as a function of feed iron/arsenic mole ratio. Pressure leach temperature 220 °C, 500 kPa oxygen overpressure
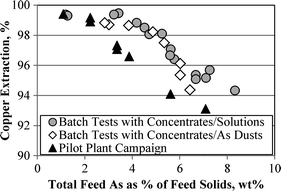
Copper extraction in pressure oxidative leaching as a function of feed equivalent arsenic content. Pressure leach temperature 220 °C, 500 kPa oxygen overpressure
Copper extraction was found to be consistently a function of the overall leach feed Fe:As mole ratio, which, for the tested range of feed material blends, translates into a distinct trend between overall feed arsenic content and copper extraction. In continuous piloting, the sensitivity of copper extraction towards arsenic was greater than in batch test work.
The important insight from these results is that the correlation between copper extraction and arsenic content in the feed blend is consistent, regardless of how and in what form the arsenic is present in this blend. This feature allows for the incorporation of arsenic bearing materials into the flowsheet, such as metallurgical dust, and the generation of a stable residue, containing the bulk of the arsenic present in the combined feed materials. In practical terms, based on the continuous test work, the Fe:As molar ratio in the overall feed blend needs to be greater than 4:1 to achieve a copper extraction of greater than 95% and greater than 5:1 to achieve copper extractions greater than about 98%.
Arsenic Extraction
Arsenic concentrations in solution after leaching and conditioning—batch testwork
Leaching temperature, °C | ||||
---|---|---|---|---|
200 | 210 | 220 | 230 | |
Arsenic in solution, g/L | ||||
After leaching | 0.27–0.29 | 0.33–0.40 | 0.44–0.53 | 0.62 |
After conditioning | 0.53–0.59 | 0.64–0.97 | 0.86–1.07 | 1.90 |
In commercial practice, a certain holdup time of the hot, acidic autoclave pulp between exiting the autoclave and the execution of liquid-solids separation is unavoidable. While arsenic concentrations in the final autoclave compartment were consistent at 0.15–0.20 g/L throughout the piloting campaign, it was found that, at higher feed arsenic contents, re-dissolution of arsenic over the period between exiting the autoclave and entering the CCD circuit could lead to arsenic concentrations in PLS of over 0.5 g/L. Lower Fe:As mole ratios in the autoclave feed resulted in a residue more prone to arsenic re-dissolution, continuing right through the CCD operation, until the final pulp was filtered and washed.
Arsenic re-dissolution from the pressure leach solids was found to be notably reduced when minimizing the contact time between pressure leach solids and the leach solution after exiting the autoclave, as well as by bringing down the slurry temperature during this holdup time [5]. During the latter periods of the pilot plant campaign, when higher arsenic feeds were tested, the autoclave slurry was cooled to about 50 °C, resulting in reduced re-dissolution of arsenic within the autoclave discharge equipment.
Precious Metals Extraction
Silver extraction by direct cyanidation of the pressure leach solids from the pilot plant campaign was minimal, at less than 9%. After lime boil treatment, as indicated by Berezowsky and Weir [12] and Collins et al. [13], silver extraction by cyanidation increased to around 95% for the lower arsenic feeds (i.e., greater than a 12:1 Fe:As mole ratio) and to about 80% for higher arsenic feeds (i.e., less than an 8:1 Fe:As mol ratio). Gold extraction after lime boil treatment was generally over 95%.
The formation of argentojarosite during pressure leaching is well documented in the literature [13], and the presence of argentojarosite in the pressure leach solids from this test program explains the refractory nature of the solids towards silver recovery by cyanidation, requiring the breakdown of the argentojarosite to render silver soluble in cyanide solutions.

Pressure leach residue copper content as a function of feed Fe:As ratio. Pressure leach temperature 220 °C, 500 kPa oxygen overpressure, piloting results
Composition and Stability of the Pressure Leach Solids
The presence of sulphate phases, in particular jarosite and basic ferric arsenate sulphate (BFAS), in the pressure leach solids generated during this work was confirmed by XRD, and chemical analysis indicated sulphate sulphur contents of up to 16%, and more typically up to 11%, in these materials. The formation of BFAS (Fe(AsO4)1−x(SO4)x(OH)x) under the conditions tested (i.e., an Fe:As mol ratio greater than 4, 220 °C) is consistent with studies by Gomez, Becze and Demopoulos [14], describing the Fe(III)–AsO4–SO4 system, explaining the high residue sulphate contents found when pressure leaching these arsenical copper concentrates.

Pressure leach residue stability, as measured by As in the leachate from the US EPA TCLP test. Pressure leach temperature 220 °C, 500 kPa oxygen overpressure
While a lime boil treatment is effective in rendering the silver in pressure leach solids soluble in cyanide solutions, the residues that passed the TCLP test after leaching failed the TCLP test for arsenic after lime boil and cyanidation, due to the reaction of BFAS with lime to produce gypsum (CaSO4·2 H2O), ferric hydroxide (Fe(OH)3), and calcium arsenate (Ca3(AsO4)2) and/or less stable iron arsenates.
The lime boil step that is required to maximize silver recovery, therefore, adds an environmental concern to precious metals recovery, and can only be justified when precious metals values are sufficient to compensate for adequate, additional measures required to address the stabilization of the process residue. As an alternative, other researchers have proposed breaking down argentojarosite by high temperature (220 °C) decomposition in the presence of low acid and ferric iron concentrations [15]. However, in Sherritt testwork, the decomposition of argentojarosite under high temperature, low acid conditions was found to be slow, and therefore of limited, if any, commercial value.
Another method to eliminate the need for a lime boil residue treatment, while still achieving high silver recoveries, is Newmont’s pressure oxidation process for gold/silver sulphide concentrates [16], according to which the free acid concentration in the pressure leach is controlled to between 12 and 22 g/L by the addition of limestone, directly to the autoclave. The resulting solids are amenable to silver recovery by direct cyanidation. However, this process has the disadvantages of the cost of limestone for acid neutralization; a reduced oxygen utilization in pressure oxidation, because of the carbon dioxide formation in the autoclave; and scaling (e.g. on the agitators and compartment walls) due to anhydrite (CaSO4) formation, requiring more frequent shutdowns and increased autoclave downtime. If applied to the processing of copper feeds, this process would have the added disadvantage of neutralizing a significant amount of the acid generated during pressure leaching, reducing the quantity of acid that could be made available for leaching copper (e.g. in a copper oxide heap leach operation).
Conclusions
Hydrometallurgical treatment of arsenical sulphide concentrates presents an environmentally credible alternative to pyrometallurgical processing. In contrast with pyrometallurgical methods, pressure oxidative leaching does not generate hazardous residues or gaseous emissions, while achieving high copper extractions. The leach solids generated respond well to precious metals recovery by cyanide leaching, provided that they are pre-treated by a lime boil.
Copper extractions were found to be sensitive to the arsenic content of the feed, and in particular to the Fe:As mole ratio of the feed blend composition, with continuous piloting extractions dropping below 98% at arsenic contents of about 2.5–3.0 wt%, and below 95% at arsenic contents above about 5%, for the concentrate composition range tested. This behaviour is independent of the form in which arsenic is present in the feed blend, whether it is in the form of a sulphide concentrate, metallurgical dust, or acid plant waste solution. The indication from current work is that feed concentrates that contain higher levels of arsenic would not allow copper extractions above about 95%, when using the process that has been described.
It was found that leach residues generated from copper concentrate feeds containing up to 4–5% arsenic are environmentally stable, passing the TCLP test for arsenic, provided that they are not subjected to a lime boil treatment. The relatively high PLS acidities require care in managing the discharge and liquid-solids separation of pressure leach discharge slurry, particularly at higher arsenic contents and/or lower Fe:As mole ratios in the feed, to minimize redissolution of the arsenic from the residue and/or to avoid producing residues with lower stabilities (i.e. As in TCLP leachate approaching or exceeding 5 mg/L). To limit the amount of arsenic in the resulting solution forwarded to copper recovery (e.g. by solvent extraction and electrowinning) and to maintain the environmental stability of the solids, a number of measures may need to be taken to limit the time, temperature and/or solution acidity while the pressure leach solids are in contact with the pressure leach solution prior to solid-liquid separation.
The recovery of silver values from autoclave solids produced as described above requires a lime boil pre-treatment before cyanide leaching. Autoclave solids generated from feed blends with higher levels of arsenic are not stable when subjected to such a pre-treatment, and lead to cyanidation residues that do not pass the TCLP test. Also, the presence of copper arsenate species in such materials leads to high cyanide consumptions and cyanide leach liquors with elevated copper concentrations.
Further Process Development
In light of the negative correlation between copper extraction and feed arsenic content identified in pressure leaching arsenical copper concentrates, further process development at Sherritt has continued to reduce the sensitivity of copper extraction and residue stability to the arsenic content in the feed. With appropriate pressure leach process modifications, this work demonstrated excellent copper extractions and environmentally stable cyanidation residues. Autoclave solids produced according to this process are more amenable to silver recovery by direct cyanidation than conventionally produced autoclave solids, without lime boil pre-treatment. The new process can handle a significantly expanded range of feed materials and feed material compositions as compared to the results presented in the current paper, without sacrificing copper extractions or environmental stability of the process residue.
Continuous piloting results will be presented in a future paper. A patent application has been filed describing the proposed modified pressure leach process.