Introduction
The output of zinc was 6.15 million tonnes in China in 2015, which accounted for approximately 43% of global zinc output [1]. And in China, about 85% zinc was produced by zinc hydrometallurgy [2]. Zinc hydrometallurgy has developed rapidly in China, almost all zinc hydrometallurgy technologies have been applied in Chinese zinc smelting plants. These technologies have their own advantages and disadvantages [3]. Until now, zinc hydrometallurgy mainly consists of the traditional roast-leach-purifying-electrowinning process. Only a few enterprises leach zinc sulfide concentrate directly to produce zinc. In the leaching process, zinc oxide and zinc sulfate in calcine are dissolved into solution, the leaching rate of zinc could reach 80–85%. And almost all Pb, Au, Ag, In, Ge, ZnFe2O4 and 60% Cu enter the leaching residue [4]. Consequently, hydrometallurgical zinc residues not only contain 18–26% zinc, but also contain valuable metals such as Pb, Ge, In. To improve the effect of comprehensive utilization of resources, zinc residues will be treated by a fuming method through vaporization in rotary kiln (also called the Waelz process) [5], in which coke serves as the fuel and reductant. Pb, Cd, In, Ge, Ga in zinc residues volatilize into the gas phase at temperature of 1100–1300 °C and enrich in zinc oxide powders for recovery subsequently. Meanwhile, involatile matter such as Fe, Cu, SiO2, are left in the kiln slag.
At present, physical separation is the main method for handling kiln slag. Typical physical separation methods include crushing-ball milling-magnetic and gravity separation [4], or flotation-magnetic separation-flotation [6]. Among these physical separation methods, the most representative and widely used one is “separation of carbon by flotation-separation of iron by magnetic separation” [7–11]. Coke, iron concentrate and tailings can be obtained using this process. When the iron content in the iron concentrate recovered from zinc kiln slag reaches the minimum standard (TFe ≥ 55%) of “GB/T 25953-2010 Recovery of iron concentrates by beneficiation of nonferrous metals”, enterprises usually sell the qualified iron concentrate to the iron works for the use of ore proportioning [12], or sell the concentrate to lead smelters for replacing pyrite cinder, or it can be used as sulfur-capturing agent in reduction-matting smelting [13]. Among these applications, the concentrate is widely used as an iron-making raw material. Because FeS, CuS and other sulphur-containing compounds in the kiln slag are tightly intermingled with unreacted Fe3O4. The iron concentrate separated by magnetic separation contains high content of sulphur, and the sulphur content is well above quality standards of iron concentrate for using in iron-making raw material, which requires the content of impurity sulphur to be lower than 0.8%. The high sulphur-containing concentrate could make steels hot short and decrease in ductility and toughness [14]. Besides, the energy used by desulphurization will increase due to high content of sulphur in raw materials. Experience shows that coke ratio would increase 5% when the sulphur content in raw materials increases 1% [15]. The content of arsenic is about 0.4–1.5% in the iron concentrate recovered from zinc kiln slag, which also restricts the concentrate’s application in iron and steel industry [16]. Silver occurs mostly as silver sulfide with a fine particle size in zinc kiln slag, and the silver sulfide is usually encapsulated in FeS and Fe3O4. Besides, a small amount of silver can substitute metal atoms of metallic iron and other sulfide phases to form isomorphous compounds [17]. Silver mainly deports to the iron concentrate separated by physical separation. There is no detrimental effects for ironmaking process with silver-containing iron concentrates. But it will waste the precious metal resources, if the silver is not recovered.
Based on the present situation, a new process for the treatment of the iron concentrate was developed, which consists of the following steps: hydrochloric acid leaching, recovering Cu and Ag by iron powder cementation, recovering Pb and Zn by sulfide precipitation, and preparing iron powders by spray pyrolysis. In the process, the effective recoveries of Ag, Cu, Zn, Pb and the high value utilization of iron from the iron concentrate can be realized.
Experiment
Experimental Material
The main chemical compositions of iron concentrate used in the present study (wt%)
Fe | Zn | Cu | Pb | S | SiO2 | Al2O3 | MnO | Ag |
---|---|---|---|---|---|---|---|---|
56.4 | 2.51 | 2.51 | 0.99 | 4.75 | 4.61 | 1.85 | 1.28 | 265 g/t |

The XRD pattern of iron concentrate used in the present study
Experimental Process and Principle

The process scheme for comprehensive utilization of iron concentrate
Experimental Method
Hydrochloric Acid Leaching
One liter of certain concentration of hydrochloride acid solution was put into a three neck flask (2 L). Experimental apparatus were assembled properly and then the hydrochloride acid solution was heated and agitated. When the reaction temperature reached 60 °C the iron concentrate (100 g) was added into the three neck flask and the leaching reaction began. In the leaching process, the reaction solution was sampled at 30 min intervals and its chemical compositions were analyzed. The total leaching time was 120 min. When the leaching experiment was finished, the solid and liquid in the reaction system were separated and analyzed.
Leaching Solution Treatment
The leaching solution (0.5 L) was put into a three neck flask (1 L), and then the solution was heated and agitated. When the reaction temperature reached 30 °C a certain amount of iron powder was added into the flask. The residue and solution in this system were separated by filtration and analyzed after a certain reaction time. Finally, the solution, obtained from iron powder cementation process, was put into a three neck flask again and reacted with FeS at target temperature. The sulfide residues and solution in this system were separated by filtration and analyzed after a certain reaction time.
Spray Pyrolysis
The main equipment of spray pyrolysis experiment was self-made ultrasonic atomization spray pyrolysis furnace. The experimental methods were listed as follows:
First, the furnace was heated to 500–900 °C, and carrier air was introduced to the furnace for 30 min to ensure temperature uniformity. Then the solution, obtained from sulfide precipitation, was atomized by ultrasonic. The atomized droplets, carried by air, went into the furnace and started the thermal decomposition reaction. Finally, the reaction products were collected and analyzed. In this study, the atomizing power and flow rate of carrier air were 2.0 W and 125 L/h respectively.
Sample Characterization
The total iron and ferrous iron contents were determined by potassium dichromate titration. ICP-AES was applied to determine the content of Ag, Cu, Pb, Zn, Si in the leaching solution and purified solution. The iron concentrate, leaching residue, and spray pyrolysis product were characterized via powder XRD analysis (RIGAKU-TTRIII, Cu/Kα, λ = 1.5406Å). Morphological studies of the synthesized products were carried out directly by a JEOL jsm-6360 scanning electron microscope.
Results and Discussion
Tow-Stage Countercurrent Leaching
The leaching rates in two-stage countercurrent leaching process
Elements | Fe | Ag | Cu | As | Pb | Zn |
---|---|---|---|---|---|---|
Low-acid leaching rates (%) | 60.38 | 79.22 | 80.39 | 49.61 | 83.81 | 57.56 |
High-acid leaching rates (%) | 34.13 | 17.56 | 17.33 | 46.19 | 11.33 | 30.18 |
Total leaching rates (%) | 94.51 | 96.78 | 97.72 | 95.80 | 95.14 | 87.74 |
Final concentration (g/L) | 121.17 | 0.067 | 6.26 | 1.12 | 1.92 | 5.69 |
The final acid concentration in two-stage countercurrent leaching process
Acid leaching types | High-acid leaching | Low-acid leaching |
---|---|---|
Final acid concentration (mol/L) | 3.57 | 0.19 |

The XRD patterns of low-acid leaching residues (a) and high-acid leaching residues (b)
Separation and Extraction of Valuable Components
Iron Powder Cementation
On the basis of standard reduction potential, Cu2+, Ag+, Pb2+, H+ except for Zn2+ can react with iron.

Thermodynamics calculation results of the main displacement reactions

The effect of reaction time on the recovery rates of Cu, Ag and Pb
Figure 5 indicates the cementation rates of Ag and Cu could reach 99.97% and 99.62% respectively, when the reaction time is 20 min. At 20–40 min, there is little influence on the cementation rates of Cu, Ag with the increase of reaction time. But the cementation rate of Cu would decrease if the reaction time is over 45 min, probably due to the re-dissolution of copper. And iron can also replace lead in the solution, but the cementation rate (around 5%) is quite low. Considering the recovery efficiency of Ag, Cu, the reaction time should be set as about 30 min.
Recovery of Lead by FeS

Log C–pH relationship in MxSy-H2O system(298.15 K)
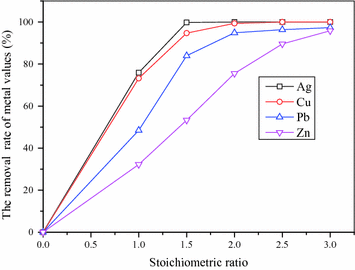
The effect of stoichiometric ratio of FeS on the removal rate of Cu, Ag, Pb and Zn
Figure 7 indicates the removal effects of Cu, Ag, Pb, Zn are distinguished, and the removal order is Ag, Cu, Pb, Zn, which is consistent with theoretical calculations in Fig. 6. The removal rates of Cu and Ag can reach above 96%, with 1.5 times theoretical amounts of FeS, and the concentrations of Cu, Ag in the purified solution are lower than 1 ppm. And 97.33% Pb and 96.00% Zn can be removed, when 3 times theoretical amounts of FeS are added into the solution. Finally, impurities in the purified solution are less than 500 mg/L, which lays a good foundation for preparing subsequent iron oxide product.
Spray Pyrolysis


The SEM image and XRD pattern of Fe2O3 obtained at 700 °C
The XRF results of Fe2O3 product
Elements | Zn | Pb | Si | Mn | Ca | Mg | Al | O | Fe |
---|---|---|---|---|---|---|---|---|---|
Content (%) | 0.029 | 0.012 | 0.027 | 0.063 | 0.0166 | 0.0024 | 0.0067 | 31.16 | 68.68 |
Conclusions
- (1)
The leaching effect of the iron concentrate recovered from zinc kiln slag is good in hydrochloric solution, due to the coordination ability of chlorine ion. The leaching retes of Ag, Pb, Cu, Fe and Zn can reach 96.78%, 95.14%, 97.72%, 94.51% and 87.74% respectively by use of two-stage countercurrent leaching method.
- (2)
The Cu and Ag in the leaching solution can be effectively enriched through iron powder cementation, but the remove effects are bad for Pb and Zn. The recovery rates of Cu and Ag could reach above 99%, with one point twenty-five times theoretical amount of iron powder in the iron powder cementation unit.
- (3)
The solution, obtained from iron powder cementation, can be deeply purified by FeS. More than 96% of Pb and Zn could be recovered in the sulfide precipitation process, when three times theoretical amount of FeS were added into the solution. Finally, impurities in the purified solution were less than 500 mg/L.
- (4)
When the spray pyrolysis temperature is 700 °C, near-spherical Fe2O3 powder with D50 = 12 μm and purity > 99% could be produced.
Acknowledgements
This work was supported by the National Natural Science Foundation of China [grant numbers: 51404307].