Opportunities for Process Improvements
The following section highlights the importance of the pyrometallurgy within industrialised society, the issues facing pyrometallurgy , drivers for changes, importance of modelling and profits that can be achieved from transfer towards knowledge-based computer-aided smart-decision-making strategies.
Pyrometallurgy plays a significant role in supporting our industrialised society.
The present paper summarises some views by a university-based research academic on opportunities for technology development in pyrometallurgy . The suggestions on ways in which these can be realised are based on a number of years experience in fundamental and applied research, and collaborations with many academics, industrial technologists, researchers and production staff. The intention is to facilitate discussions and develop common approaches to these issues.
Pyrometallurgical operations have large asset base, inventory (work-in-progress), fixed capital and labour costs. Significant improvements to process profitability can be facilitated in pyrometallurgy through increasing throughput, improving recovery , decreasing work-in-progress (inventory), increasing the “premium” from complex feed sources, decreasing operating costs. These improvements are directly dependent on, and can be achieved by, improved process stability, process optimisation, advanced planning, feed optimisation (e.g. blending, complex feeds), wider introduction of feed-forward process control —all of these advances can be facilitated by the accurate process modelling.
- 1.
Value chain optimisation (the optimisation of the operations across the extraction chain from mining through mineral processing to hydrometallurgical, pyrometallurgical and metal production stages),
- 2.
The optimisation of mining plans, incorporating downstream operations through to the pyrometallurgical step,
- 3.
The optimisation of blending of available feed sources,
- 4.
The optimisation of raw materials purchasing/marketing (optimisation of the company marketing based on the downstream steps—up to the pyrometallurgical processing),
- 5.
The development of synergetic approaches (combining and optimising energy requirement/generation of various processing routes such as hydro- and pyro-metallurgy, e.g. [1, 2]),
- 6.
New process developments,
- 7.
Scale-ups,
- 8.
New process commissioning,
- 9.
Staff metallurgical training and professional education,
- 10.
Process optimisations,
- 11.
Trouble-shooting, and many others.
Virtual Reactors—computerised models of individual pyrometallurgical reactors accurately describing the output of the process as a function of input and process conditions, and
Pyro-GPS—computerised systems for optimisation of integrated process operations.
The development of such systems for pyrometallurgy has now become possible and has the potential to deliver substantial benefits.
Virtual Reactors and Pyro-GPS—Systems for Improved Control and Process Optimisation
The following section outlines components of the knowledge-based computer-aided smart-decision-making system—Virtual Reactor and Pyro-GPS—for improved control and process optimisation.

Key components of GPS (General Positioning System)
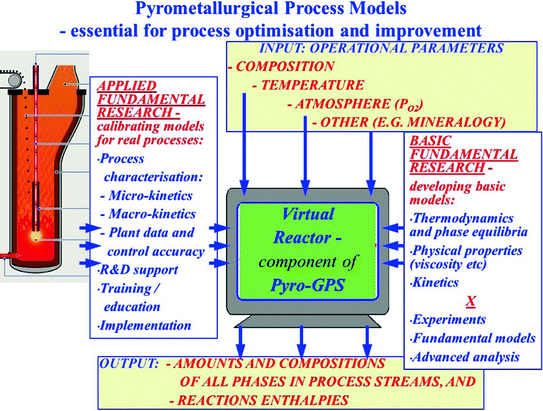
Virtual reactor and Pyro-GPS
Key components of the proposed pyrometallurgical Virtual Reactor
Virtual reactor and Pyro-GPS components to be predicted or improved | Possible solutions/actions |
---|---|
1. Thermodynamic models predicting thermodynamic direction, driving force and extent and enthalpies of reactions (the latter defining the heat balance ); and Phase equilibria —describing the states (liquid, solid or gaseous) and chemical compositions of the phases present | Integrated computer—based thermodynamic modelling and experimental research |
2. Physical property models to predict viscosities, surface tension, densities and other | Focused integrated laboratory-based experimental and modelling studies |
3. Micro-kinetic models (at a scale up to 20–100 μ) to predict mechanisms and rates of heterogeneous gas/solid/liquid reactions | Elemental reactions characterisation, advanced micro-analysis, modelling |
4. Macro-kinetic models to describe fluid flow and heat transfer at full multi-meter reactor scale | Fluid flow modelling, CFD model development including turbulent flow and incorporation in reaction models |
5. Plant data accuracy verification/improvement | Snap shot sampling of processes/operations with independent laboratory measurements and modelling of input—output results |
6. Plant control accuracy verification/improvement | Instrumental factors—improved on-line measurements and process control equipment, and human factor—motivation, education, Business Intelligence BI systems |
7. Performance of the reactor within overall multi-reactor flowsheet | Flowsheet modelling |
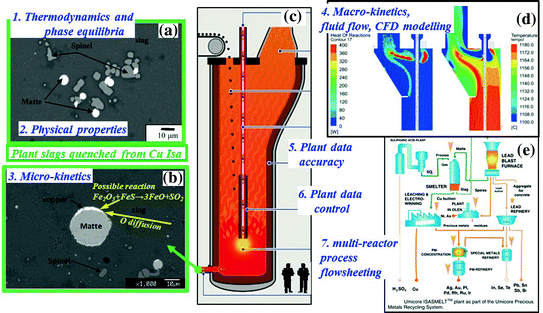
Schematic illustrations of the critical components for the Virtual Reactor and Pyro-GPS—for pyrometallurgical process characterisation, control , modelling and optimisation. a and b—plant slag samples quenched from Cu IsaSmelt [3]; c—IsaSmelt schematic; d CFD predictions for TSL furnace ; e a plant flowsheet
Thermodynamics and Phase Equilibria
The control of any pyrometallurgical smelting process involves minimum three output parameters—chemical target, heat balance and liquidus (or proportion of solids)—all three are described by chemical thermodynamics and phase equilibria .
Many pyrometallurgical processes are operated close to chemical equilibrium conditions. Using thermodynamic predictions it is possible to identify the direction, driving force and maximum extent of reactions, as well as thermal balance. Thermodynamics information is also essential to quantify the direction and driving force of the reactions for non-equilibrium processes.
Slag and other large-volume fluid streams in pyrometallurgy frequently have some solids. An example of a multi-phase reaction system is shown in Fig. 3a and b. Micrographs of a slag sample quenched from the Cu TSL furnace [3] show the presence of solid spinels (magnetite solid solution) and suspended matte droplets of approximately 10 μ in size. The physical properties of slag depend critically on the proportion of solids and composition of the remaining liquid matrix—these can be described by phase equilibria .
In summary— thermodynamic and phase equilibria predictions therefore are essential foundation for quantitative and reliable prediction of pyrometallurgical processes.
The physical properties of the condensed fluid streams, such as viscosities, surface tension, densities, are important in determining the rate and extent of separation of phases. For example, the separation of the matte from slag in copper smelting depends on the settling of the matte droplets (see Fig. 3a and b) depend on relative densities of slag and matte, slag viscosity , surface tension.
Micro-kinetic phenomena are important for all heterogeneous processes that are common in pyrometallurgy —although furnaces are usually several meters in size, the actual heterogeneous gas/solid/liquid reactions take place at the microscopic scale of approximately ~20–100 μ. For example, in a TSL copper smelting the oxidation of iron from sulphide FeSx (matte) to oxide FeOy (slag ) form by the oxygen blasted through the lance involves a number of mechanisms including the oxygen mass transfer from the large gas bubbles through the slag to the matte phase—the presence of this mechanism is demonstrated in Fig. 3b by the formation of the liquid copper rim on the surface of the matte particle. The recovery of value metals from slag are directly dependent on the separation from slag of the suspended liquid matte or metal micro-sized droplets, such as the matte droplets in Fig. 3a and b. Appropriate description of these phenomena need to be incorporated in the Virtual Reactor model .
Macro-kinetic factors at the reactor scale strongly influence pyrometallurgical processes. For example, in the TSL copper smelting (Fig. 3c), the movements of the large gas bubbles , liquid slag and matte in the turbulent bath and in the upper gas areas of the furnace are critical for the operation.
Plant data accuracy on process inputs and outputs is an essential component for the quantitative prediction and optimisation of the pyrometallurgical operations. For example, the accurate information on the composition and temperature of the feed and output streams is critical for prediction and optimisation of the process thermochemistry, however absolute values currently available for many important industrial parameters are not sufficiently accurate for quantitative predictions or are not available at all.
Plant control accuracy is crucial to maintain stable process. For example, the control of the feed rates is not always accurate, introduction of the modern weight discharge systems should be used to improve that. Variability of input, response time, precision and a number of other key characteristics are important for accurate control of process.
Performance of individual reactors within multi-reactor flowsheet is a logical next stage to obtain the maximum value from the improved control and optimisation of the overall process. The development of Pyro-GPS will enable the optimisation of the larger multi-unit operations or even whole value chain from mining through mineral to pyrometallurgical processing.
Advances in analytical, control and computer technologies have enabled significant progress to be achieved in all of these seven groups. This now provides substantial opportunities for the development of the next stage of advanced modelling tools in the form of Virtual Reactors and Pyro-GPS.

Components and stages of development and implementation of pyrometallurgical process
Virtual Reactor and Pyro-GPS Are Possible
The following section outlines recent advances and current status of capabilities for the development and implementation of Virtual Reactors and Pyro-GPS.
Recent Progress in Thermodynamics and Phase Equilibria Experimental and Modelling Capabilities
Microanalysis for Experimental Phase Equilibria and Thermodynamic Studies
- (i)
electron probe X-ray microanalysis (EPMA) [4]—this technique enables accurate composition measurements to be undertaken with minimum detection limit down to 300 ppm and even better with spatial resolutions of the order of ~0.5–1 to a few microns depending on the matrix and conditions, and
- (ii)
laser ablation inductively coupled plasma mass spectrometry (LA-ICPMS) [4]—the technique that achieves the minimum detection limit down to ppb level with the spatial resolution of several dozen microns.
These microanalysis techniques provide breakthrough capabilities in phase equilibrium studies greatly extending the range of systems and the accuracy of characterisation with very few limitations.

Thermodynamic Modelling and Computational Capabilities
Significant advances in thermodynamic predictive capabilities have been achieved through (i) developed complex theoretical solution models, (ii) more accurate self-consistent multi-component multi-phase thermodynamic databases, and (iii) increased speed and storage capacity of modern computers. Several commercial computer packages are currently available including MTDATA [11], ThermoCalc [12], FactSage [13, 14] and PANDAT [15]. These packages have powerful Gibbs free energy minimisation modules, flexible input and output interfaces for various types of calculations, and, most importantly, sophisticated solution models and comprehensive evaluated databases for wide ranges of phases and chemistries. The thermodynamic databases are developed through thermodynamic optimization that involves selection of appropriate thermodynamic models for each of the phases in a system, critical simultaneous evaluation of all available thermodynamic and phase equilibrium data, and optimization of thermodynamic model parameters to obtain one self-consistent set best reproducing all experimental data as functions of temperature and composition.
Importance of Complex Solution Models for Pyrometallurgy
Availability of the adequate solution models in the computer packages is particularly important for pyrometallurgy since the key phases such as slag , matte, spinel, melilite, olivine, pyroxene are all complex solutions characterized by (i) strong interactions and (ii) short- or long-range-ordering at atomic level. The Gibbs free energy functions for these phases therefore exhibit complex non-ideal behavior as a function of composition and temperature . It is not possible to describe the properties of these key solution phases with over-simplified models e.g. ideal, regular or sub-regular, dilute solutions, fixed activity coefficients or similar models. The development of the advanced theoretical models such as The Modified Quasichemical Formalism [16–19], The Compound Energy Formalism [20, 21], that take strong interactions and complex short- or long-range-ordering at atomic level into account, provide the important basis for significant further progress. Various complex solution models are incorporated in commercial computer packages CEQCSI [22], MTDATA [11], MPE [23], Thermo-Calc [12], FactSage [13, 14].
Importance of Experimental Data: No Experiments = No Interaction Parameters = Inadequate Unknown Uncertainties
Adequate description of these complex non-ideal behaviors in the key pyrometallurgical solutions such as slag and matte require binary and ternary model parameters, those in turn require experimental data. The absence of the data and, therefore, of the important binary and ternary parameters results in the incorrect ideal solution approximation with significant unknown uncertainties. The analogy to GPS would be to drive along the straight line without road coordinates (see Fig. 1).
Currently, for the majority of non-silicate systems, there is no or very limited experimental data available. There are significant uncertainties and gaps in experimental characterization for many silica -containing systems. Several types of data are needed to uniquely specify the Gibbs free energy functions including, but not limited to, phase equilibria , thermodynamic activities, enthalpies, entropies, heat capacity, Gibbs energies of reactions. To minimize uncertainties and to achieve reliable multi-component predictions it is essential to (i) systematically and accurately experimentally investigate all binaries and ternaries (systems with expected strong interactions of phase components given priority) and (ii) reoptimise these thermodynamic databases. This can best be done through the integrated experimental and thermodynamic modelling research programs.
Integrated Experimental and Thermodynamic Modelling for Large, Multi-component, Multi-phase Database Development in Pyrometallurgy
Examples of the development of large, multi-component, multi-phase databases involving experiments and thermodynamic modelling in pyrometallurgy include, but not limited to, studies of Decterov et al. [24–27] for extensive wide range of chemistries, Kang et al. [28] and Jung [29] for iron and steel industries, Chartrand et al. [30, 31] for aluminum and light alloy production, Gisby and Taskinen et al. [32] on MTOX database for ceramics and non-ferrous applications. The high temperature studies on copper -lead -zinc-containing gas/slag /matte/metal/speiss/solids oxide and sulphide systems with major “Cu2O”–PbO–ZnO–FeO–Fe2O3–SiO2–S, slagging Al2O3, CaO , MgO and selected minor elements , including As, Sn, Sb, Bi, Ag, Au is another example of the integrated experimental and modelling approach to the multi-component multi-phase database development [6, 7, 9, 10, 25, 26, 33–39]. The concurrent experimental and thermodynamic modelling studies are carried out simultaneously in parallel in one laboratory by an expert team of continuing research fellows—this is an important factor to ensure high productivity and quality of the overall research outcomes. Modelling helps to plan and carry out experiments. Targeted experiments on low order systems are essential for modelling to close gaps and resolve discrepancies, and on multi-component systems are essential to test the model close to real industrial conditions. Dozens of binary, ternary and higher-order phase diagrams have been experimentally investigated. The optimisation continuously performed in a number of cycles from binary and ternary to the multi-component systems and back ensures continuous availability and improvement of the database. Active engagement of technologists from consortia of leading international metallurgical, recycling and advanced materials companies supporting the program along with government ensures (a) focus on industrial needs and (b) fast direct implementation and technology transfer of fundamental research results to ensure high impact.
Since these fundamental data are intended for the development of key internationally-used thermodynamic databases, it is critical that both the experimental studies and the thermodynamic database development be undertaken to the highest professional standards. For example, a recent study of ZnO-containing slags systems by the author [39] clearly demonstrates the need for identification and critical analysis of elementary reactions, and reaction mechanisms and potential sources of uncertainties to be assessed before any experimental measurements are undertaken and before any data are incorporated into the databases.
Systematic experimental and modelling integrated research is important to develop accurate thermodynamic and phase equilibria description as a foundation for the future Virtual Reactors and Pyro-GPS.
Recent Progress in Other Areas Essential for the Pyrometallurgical Process Control, Modelling and Optimisation
Accurate thermodynamic and phase equilibria description of proportion of solids and the composition of the remaining liquid matrix provides important foundation for characterisation of other physical properties of the high-temperature systems (such as viscosity , surface tension, density, thermal and electrical conductivity).
The characterisation of micro-kinetic processes is greatly facilitated by the advances in the microanalysis (EPMA and LA-ICPMS) and other analytical techniques such as TEM, XPS , High-resolution SEM [4]. Fundamental elementary reactions in industrial reactors can now be investigated by analysing quenched industrial samples using these advanced microanalysis techniques, in particular EPMA. For example, the proportion and form of the physically entrained and chemically dissolved types of value metal losses can be readily determined with EPMA (see Figs. 3a and b).
Most reactions in pyrometallurgical systems are heterogeneous (i.e. involve several phases), take place at the interface between phases, and involve the mass transfer steps of reactants and products to and from the reaction interface in each phase involved. The EPMA analysis of compositional trends as a function of distance from the phase boundaries at the micron scale can be readily determined with EPMA and can greatly assist in the determination of the mechanisms of micro-kinetic processes.
The example of the EPMA application to investigate the micro-kinetic reaction can be demonstrated with reference to Fig. 3b [3]. The copper rim detected with EPMA confirms the oxygen mass transfer through the slag to the matte droplet. The compositional profile as a distance from the matte drop into the slag can assist in characterisation of the mass transfer .
The derivation of the micro-kinetic processes and elemental reactions from the microanalytical measurements requires special expertise and experience in pyrometallurgy , and requires operation of EPMA by trained expert pyrometallurgist. Examples of the EPMA application to determine the mechanisms of the reactions in pyrometallurgy can be found in literature [6, 38–43]. Example of the microanalysis use to identify an operational issue is given in Watt et al. [4].
The analytical and computer modelling tools, that have recently became available, can now significantly assist in prediction of the macro-kinetics at the whole reactor scale. The reactions taking place in various parts of reactors can be established using detailed microanalysis of industrial samples quenched from different reactor locations. The Computation Fluid Dynamics (CFD ) modelling with packages such as Fluent [44–46] can combine micro-kinetics, thermodynamics and phase equilibria to predict the processes over the whole reactor.
The advances in analytical, measurement and control equipment as well as in computer storage and computer data-analysis capabilities provide new opportunities to significantly improve plant data accuracy and plant control accuracy.
Accurate predictions of the individual pyrometllurgical reactor outputs as a function of various input parameters may further be incorporated into the multi-unit-operation flowsheet models of the groups of the reactors, parts of the pyrometallurgical operations as well as integrated models of the larger metallurgical operations using currently available commercial or specialised computer flowsheeting packages such as Aspen [47], SysCad [48], MetSim [49]. The modelling at the multi-unit-operation flowsheet level with recycling streams can bring significant financial advantage through optimisation of the control parameters of several furnaces or other operational units. The flowsheet models with recycling streams use numeric optimisation with multiple calculations, which makes the direct integration of the sophisticated thermodynamic packages into these flowsheet models problematic—this may be overcome at this stage by preliminary simplified polynomial descriptions of different pyrometallurgical reactors using accurate sophisticated models and then incorporation of the simplified description into the overall flowsheet model .
Virtual Reactor and Pyro-GPS—Future Scientific Development Needs and Possible Priorities
- (i)
basic fundamental research on further improvements of the models for basic properties such as thermodynamic, phase equilibria , physical properties,
- (ii)
applied fundamental research linking basic models to the prediction of processes in real reactor, and
- (iii)
programs to improve accuracy of the plant data and process control .
The thermodynamics and phase equilibria are essential foundation for industrial process predictions in pyrometallurgy . Significant further improvement of the thermodynamic databases is (a) critically needed; (b) challenging but (c) possible. An example of this type of extensive research program is given in several papers in this volume with focus on analysis and experimental work [35], detailed description of the thermodynamic database development for large 7-component “Cu2O”–PbO–ZnO–FeO–Fe2O3–SiO2 system [36] and the overall 15-component system with “Cu2O”–PbO–ZnO–FeO–Fe2O3–SiO2–S–Al2O3–CaO –MgO major and As, Sn, Sb, Bi, Ag, Au minor elements [37].
The progress in other fundamental pyrometallurgy knowledge areas, such as physical properties and kinetics, is also critical.
Basic fundamental models are not sufficient to accurately describe real industrial processes—many non-equilibrium and other factors must be incorporated—that work may progress in two streams including (i) applied fundamental research programs to characterise micro-kinetic and macro-kinetic processes in real furnaces, and (ii) special programs to improve accuracy of the plant data and process control . This is discussed in detail in this volume [50].
Characterisation of micro- and macro-kinetic processes in industrial furnaces can now be investigated through quenching of the samples from selected reactor locations with further detailed analytical characterisation using SEM , EPMA and LAICPMS and selected targeted laboratory studies.
Majority of pyrometallurgical processes at present are operated using feedback approach—adjustments are made after the material has been processed in the reactor. The feedback control does not require accurate absolute values to achieve relatively good stability of the operations. Many important thermochemical parameters of the pyrometallurgical processes are not measured at all or have limited accuracy. The feedback control approach limits capability to improve stability and optimise the process for complex and variable feed streams.
A possible approach to (a) better characterise industrial process and (b) improve industrial plant data accuracy can involve snap-shots campaigns—targeted sampling of all input and output streams synchronised to take into account residence time in the furnace , followed up by detailed analysis with a range of techniques in independent laboratories, and analysis of the data through modelling [50].
The development and implementation of modelling can be done as a staged process, progressively and concurrently (a) improving characterisation of the industrial process, (b) increasing accuracy of the industrial process models, (c) developing R&D and production staff skills, and (d) obtaining benefits and profits at each stage of development and implementation.
The level of industrial process models may be different depending on the needs as well as availability of necessary data and capabilities [50]. Simplified thermodynamically-based models with the kinetic “calibration” parameters valid for limited range of conditions (e.g. [51]) can be very effective as process advisers improving control of the process, in preparation of blends, in short and long term production planning, limited scale-up predictions, staff training. The simplified models can be used as a basis for development of the feed-forward control . More sophisticated multi-step reactor models require more data and efforts to develop, but can be more accurate and valid over wider ranges of conditions [50]. The Computer Fluid Dynamic modelling can provide significantly more detailed description of processes in various parts of reactors and can assist to resolve more complex operational and design issues.
Many of these improvement activities are under way in many companies. A lot of opportunities still exist in pyrometallurgy sector.
Virtual Reactor and Pyro-GPS Developers—Triple Helix Government, Industrial and Academic
The following section outlines views on the Virtual Reactor and Pyro-GPS developers—triple helix of government, industrial and academic research components of the knowledge-based society, importance of the University research, highlighting that the knowledge-based circular economy requires circular knowledge generation and therefore circular research funding strategies.
Further research is essential to generate the knowledge-base that is necessary to continue progress in the pyrometallurgy field. The research is delivered by the university, government and industrial sectors, which are linked into so called “triple helix” [52] of the knowledge-based economy “DNK” (see Fig. 6).

Triple helix of university, government and industrial research for knowledge-based circular economy (the triple helix and circular economy is taken from [52])
The knowledge-based circular economy requires the circular approach not only to the materials, but to the knowledge, that in turn requires the circular approach to the knowledge finance—that is to sustain and further develop the knowledge in a given sector, part of the profits achieved through the knowledge generation in the given sector (e.g. primary and recycling pyrometallurgy ) should be re-invested into the research in pyrometallurgy . There is an important role for university to ensure maintenance and further development of the knowledge base. There are finance issues that must be addressed by government and industry to ensure that university research capabilities in pyrometallurgy are maintained and further developed to provide ongoing support to industry and industrialised society.
Importance of Motivated Professional Staff for Industrial Implementation
Making and sustaining advances in industrial practice can only be made by active motivated expert professional staff. Targeted training and education programs are needed to prepare staff to make the most of the advanced characterisation and predictive methods. These programs should be specifically developed for all organisation levels from high through middle management, R&D, technical and production staff, to the operators. These programs should be reinforced with the development and implementation of clear production targets and plant control strategies. External experts can assist in implementation, but it is down to the operations staff to make these work and in doing so derive the benefits from improved performance.
Concluding Statements
More powerful and advanced research tools, in combination with the significant progress in control of the operations, offer new opportunities for process improvements. To realise these opportunities it is essential to accelerate (a) these research efforts, and in parallel (b) actively implement of research outcomes into practice.
There are opportunities for significant improvement in process efficiencies in pyrometallurgical processing through development of Virtual Reactor models and Pyro-GPS. The advances in technical, analytical, experimental and theoretical research capabilities are such that these are achievable goals.
The challenge is one of further development and implementation, these require support from industry and government.
Implementation requires systematic strategic plan that includes business, management and development of the skilled motivated workforce. The realisation of these opportunities requires high levels of expertise from the technologists in industry complemented by close involvement of and collaboration with researchers.
Improvements to process efficiencies and resource recovery are to the benefit of industry and to the society in general through reducing impacts on energy and resource utilisation, and facilitating the resolution of environmental, societal and geopolitical issues.
Acknowledgements
The author would like to thank many industrial sponsors including Umicore, Aurubis, Kazzinc Glencore, Nyrstar, BHP Billiton Olympic Dam Operation, Outotec (Espoo and Melbourne), PASAR Glencore, Anglo American Platinum , Atlantic Copper , Rio Tinto’s Kennecott operation, Altonorte Glencore and many others, as well as Australian Research Council Linkage program for the financial and technical support for this research. The author would like to acknowledge help of colleagues in preparation of this paper including Prof. P. C Hayes, Prof. Decterov, Dr Shishin, Dr Hidayat and others. Special acknowledgement and thanks to Prof. Hayes for the initiation and tireless continuous significant input over many decades into the research and education in the metallurgy sector.