Introduction
Cementite is a highly valuable charge material for the electric arc furnace (EAF) steelmaking . It was produced by Nucor in Trinidad in 1990s, although the full capacity was not reached, and operation lasted for only four years [1]. In that process, the reducing gas was made from natural and hydrogen . Natural gas is also used directly (unreformed) in HYL/Energiron processes, in which produced DRI can contain a significant fraction of cementite (1.4–4.0 wt% [2]).
Cementite (iron carbide Fe3C) is formed in the reduction of iron oxides or by cementation of iron in the gas atmosphere (CO–CO2–H2 or CH4–H2) with high carbon activity. When carbon activity in the system is equal to or below one (standard state is graphite), cementite decomposes to graphite (carbon black or soot) and hydrogen .
Can be cementite formed directly from wüstite or magnetite in the reduction of iron oxides by CO–CO2–H2 gas mixture passing by the reduction to metallic iron ? Literature gives a negative answer to this question.
Mechanisms of cementite formation have been discussed in [3–16] and other papers. Zhang and Ostrovski [3–5] demonstrated that formation of cementite by CH4–H2 gas includes reactions of iron oxides reduction to metallic iron by hydrogen and cementation of iron by methane . Reduction of iron oxides and cementation by CO–CO2 gas mixtures was studied only in a few works [13–15]. Sato et al. [14] established that an effect of hydrogen on cementite formation depends on temperature and gas composition. Satoh et al. [13] suggested that at 600–833 K, magnetite was reduced to “active” iron which was converted to cementite by reaction with CO.
Kim et al. [15] analysed formation of cementite in the reduction of magnetite by CO–CO2 gas mixture under conditions when thermodynamically stable cementite (in the gas with high carbon activity) can be formed by carburisation of iron and directly from wüstite. Experimental results obtained in [15] indicated that Fe3C was formed by carburisation of iron ; under condition of high carbon activity and high oxygen partial pressure, when cementite was stable but formation of iron was thermodynamically impossible, cementite was not observed.
Gudenau et al. [16] also concluded that the precondition for the formation of Fe3C is a complete reduction of iron oxides to metallic iron and consecutive iron carbonisation.
Thus, investigations of reduction of iron oxides and iron ores by CO–H2 gas in [13–15] and other works demonstrated that iron oxides are reduced to metallic iron which is carburised by CO.
In situ study of metallurgical processes using High-Temperature XRD (HT XRD) analysis provides valuable information on the materials structure and mechanisms of metallurgical reactions at high temperatures [17–20]. This technique was used by the authors of this paper in a study of reduction of magnetite doped with alumina [21]. Lattice parameters of iron obtained from the HT XRD spectra were used to find carbon concentration in the reduced iron at the experimental temperature . These data are important for understanding of mechanisms of reduction /cementation reactions.
The aim of the present work is an experimental investigation of the reduction /cementation reactions in CO–CO2 gas atmosphere and cementite stability in this gas and in argon using in situ high temperature XRD analysis.
Experimental

Schematic of the HT XRD system
The HT XRD system is composed of an X-ray source (copper ) and an X-ray diffraction detector, a disk-shape high temperature chamber (height 92 mm and diameter 130 mm, Anton Parr Co. Ltd.) with a Pt heater, and a gas delivery system. The plate heater is located along the side wall of the chamber. The gas (CO, CO2 and Ar) flow rates were controlled by mass flow controllers. A pellet of hematite was placed on an alumina sample holder in the high temperature chamber. One thermocouple (type K) in the chamber is located just underneath the sample in the sample holder and another (also type K) is near the heater to control the chamber temperature . Samples were scanned with 2θ in the range of 10–90° with a step size of 0.02° and 0.6 s scanning time at each step. One X-ray spectrum was determined in approximately 15 min. Changes in the XRD spectra during the 15-min measurements can be ignored as the reduction /cementation reactions are relatively slow [21]. Some experiments were performed with scanning in the range of 28–48°; these measurements took about 8 min.
First XRD measurement was taken at room temperature before the reduction experiment. The first high temperature XRD measurement was carried out in Ar gas after reaching the experimental temperature . Then the gas composition was changed to CO–CO2 gas mixture with high carbon activity (cementite stable gas composition) to start the reduction /cementation of the sample. HT XRD spectra were taken in the progress of reduction /cementation with 15 min intervals at the early stage and 60 min intervals at the late stage. After the last high-temperature measurement, the chamber temperature was decreased to room temperature in the reducing gas. The final XRD measurement was carried out at the room temperature . Afterwards, the samples were subjected to SEM analysis.
Thermodynamic Analysis
Iron Cementation
Reduction /cementation of hematite was studied at temperatures 873–1173 K using CO–CO2 gas mixtures with different carbon activities.




Activity of carbon in equilibrium with cementite and ferrite, and cementite and austenite
Temperature , K | Equilibrium with Fe3C and α-Fe | Equilibrium with Fe3C and γ-Fe | ||||
---|---|---|---|---|---|---|
873 | 973 | 1000 | 1000 | 1073 | 1173 | |
Equilibrium constant for reaction (1) | 0.533 | 0.804 | 0.886 | 0.994 | 1.066 | 1.187 |
xC (γ-Fe) | 0.0356 | 0.0442 | 0.0580 | |||
a Fe | 1 | 1 | 1 | 0.959 | 0.948 | 0.930 |
a C | 1.876 | 1.243 | 1.128 | 1.166 | 1.100 | 1.047 |
(PCO)2/(PCO2) | 0.173 | 1.210 | 1.914 | 1.977 | 7.285 | 34.00 |
PCO | 0.339 | 0.651 | 0.730 | 0.730 | 0.889 | 0.972 |

![$$ \Delta {\text{G}}_{5}^{0} = { - }166,406 + 170.8{\text{T}}\,\left( {{\text{J}}/{\text{mol}}} \right)\,[23] $$](../images/468727_1_En_54_Chapter/468727_1_En_54_Chapter_TeX_Equ6.png)


Composition of gas in equilibrium with cementite and iron (total pressure 1 atm) is also given in Table 1.
Reduction of Wüstite
CO partial pressure and activity of carbon in CO–CO2 gas (total pressure 1 atm) in equilibrium of wüstite with cementite and iron
Temperature , K | 873 | 923 | 973 | 1000 |
---|---|---|---|---|
Equilibrium with wüstite and cementite | ||||
PCO, atm | 0.445 | 0.528 | 0.603 | 0.639 |
a C | 3.87 | 1.85 | 1.11 | 0.667 |
Equilibrium with wüstite and iron | ||||
PCO, atm | 0.532 | 0.564 | 0.593 | 0.606 |
a C | 6.55 | 2.28 | 0.887 | 0.549 |

![$$ \Delta {\text{G}}_{9}^{0} = 458,181{-}460.3{\text{T}}\,\left( {{\text{J}}/{\text{mol}}} \right)\,[23] $$](../images/468727_1_En_54_Chapter/468727_1_En_54_Chapter_TeX_Equ10.png)

![$$ \Delta {\text{G}}_{11}^{0} = 149,184{-}150.0{\text{T}}\,\left( {{\text{J}}/{\text{mol}}} \right)[23] $$](../images/468727_1_En_54_Chapter/468727_1_En_54_Chapter_TeX_Equ12.png)
Reduction of wüstite to metallic iron at 873 and 923 K proceeds at higher CO partial pressure and carbon activity than reduction to cementite . However, in the reduction of wüstite to iron at 973 K, carbon activity in the system is below 1. These results indicate, that at 873 and 923 K, reduction of wüstite to cementite is thermodynamically more favourable in comparison with the reduction to iron , while in the reduction at 973 K, wüstite can be reduced to iron which is converted to cementite under conditions specified in Table 1.
The effect of temperature in the range 873–1123 K on the reduction /cementation reactions was experimentally studied at constant carbon activity in the gas phase.
Results
Effects of Temperature and Carbon Activity
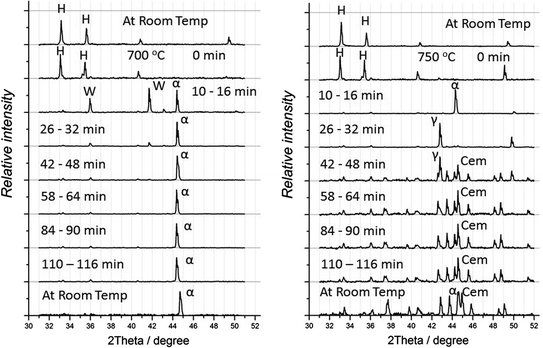
HT XRD spectra obtained in the reduction of hematite by CO–CO2 gas mixture with aC = 1.5 at 973 (left) and 1023 K
In the reduction of hematite at 973 K, α-Fe was formed after 10-min reaction; XRD spectrum after 10-min reduction also included wüstite peaks, which became very weak after 26 min reaction. Cementite was not observed in this experiment although its formation in CO–CO2 gas with aC = 1.5 is thermodynamically feasible.
In the reduction at 1023 K, α-Fe was also formed after 10 min reaction; it was converted to γ-Fe after 26 min reaction; formation of Fe3C was observed after 42 min. Cementite was stable during this experiment which lasted 110 min. Intensity of cementite peaks in the HT XRD spectra significantly decreased with increasing reduction temperature to 1073 K; the cementite peaks were not observed in the experiment at 1123 K. In the reduction at both temperature , oxides were reduced to γ-Fe within 10-min reaction.

HT XRD spectra obtained in the reduction of hematite by CO–CO2 gas mixture with aC = 3.0 at 923 (left) and 973 K
In the reduction at 923 K (Fig. 3), a small amount of α-Fe was formed after 19 min reaction; HT XRD spectra taken after 38 min reaction included cementite peaks. Results of this experiment are inconclusive; Fe3C could be formed directly from wüstite after 38 min reaction, although reduction of wüstite to α-Fe which was further converted to cementite cannot be excluded. In the reduction at 973 K, α-Fe was formed after 5 min reaction; it was converted to Fe3C after 19 min reaction. Traces of wüstite were observed through the reduction process. A weak peak of graphite was also observed by the end of the experiment. Reduction at 1023 K started with formation of α-Fe after 5 min reaction; which was converted to γ-Fe and further to Fe3C after 19 min reaction. A weak peak of graphite was also observed by the end of the experiment.
In the experiment at 1073, hematite was converted to magnetite upon heating in argon to this temperature . γ-Fe was observed after 5 min reaction; it was converted to Fe3C after 19 min reaction. Conversion was incomplete. Graphite peaks were observed after 38 min reaction.
Cementite was not observed in the experiment at 1123 K. Hematite was also converted to magnetite in the process of heating; magnetite was reduced to γ-Fe within 5-min reaction.
Cementite was stable in all experiments at 923–1073 K in the gas atmosphere with aC = 3.0. Weak peaks of graphite were observed in these experiments; time of their appearance decreased with increasing temperature ; it was 115 min at 973 K, 86 min at 1023 K, and 38 min at 1073 K. Graphite peaks were not seen in the HT XRD spectra of samples in the reduction /cementation at 923 K.

HT XRD spectra obtained in the reduction of hematite by CO–CO2 gas mixture with aC = 5.0 at 923 K (left) and by CO–CO2 gas mixture with aC = 10.0 at 873 K
In experiment at 1073 with CO–CO2 gas with carbon activity 10, cementite peaks were not observed at 1073 K; weak graphite peaks appeared in the XRD analysis starting with scans 38–47 min.
In the reduction of hematite at 1123 K with aC = 5.0, only austenite and graphite were observed in the HT XRD spectra (as in experiments with aC = 3.0); no cementite was formed. In both cases, graphite peaks appeared in the spectra after 86 min reaction.
Two HT XRD experiments were conducted at lower temperatures; at 803 K using gas with aC = 60.0 and 873 K with aC = 10.0. In the experiment at 803 K, reduction did not go further magnetite; no metallic iron nor cementite was formed (wüstite is unstable at this temperature ).
Hematite at 873 K (Fig. 4) was reduced to wüstite which was converted further to cementite . Cementite started to form from wüstite after 38 min reaction, although conversion of wüstite to cementite was incomplete.
Cementite Instability in Argon
Results obtained in the reduction /cementation of iron oxides in CH4–H2 and CO–CO2 gas atmospheres in [3–11] showed that cementite was unstable even in the gas with high carbon activity and decomposed to metallic iron and graphite. The main reason of cementite instability was deposition of carbon black which decreased carbon activity in the system down to 1. The rate of cementite decomposition in CH4–H2–Ar gas mixture was close to that in argon [3–8].

HT XRD spectra obtained in the reduction of hematite by CO–CO2 gas mixture with aC = 10.0 at 873 K and in argon (left) and in the reduction by CO–CO2 gas mixture with aC = 3.0 at 1,023 K and in argon
In experiment at 873 K, cementite was stable in CO–CO2 gas with high carbon activity aC = 10. Switching gas atmosphere to argon after approximately 200 min reaction caused cementite decomposition to α-Fe and amorphous form of carbon (graphite peaks are not seen in the HT XRD spectra). Similar pictures were observed in experiments at 923 and 973 K; cementite decomposed with formation of α-Fe after switching the gas atmosphere with high carbon activity to argon.
In experiments at 1023 K with carbon activity 3.0 (Fig. 5), cementite decomposed to γ-Fe and amorphous carbon after switching CO–CO2 gas mixture to argon. γ-Fe was converted to α-Fe with further exposure in argon as a result of iron decarburisation in argon which contained 5 ppm oxygen. Increase in the carbon activity to 25.0 at this temperature accelerated formation of cementite , however, had no effect on cementite decomposition in argon.
Discussion
Thermodynamic activity of carbon defined by the composition of CO–CO2 gas in all experiments was above the equilibrium value needed for the formation of cementite .
In the reduction /cementation experiments with aC = 1.5 at 973–1123 K, hematite was reduced to metallic iron , however cementation of iron was not observed at 973 and 1123 K. Cementite was formed at 1,023 K (Fig. 3), low-intensity XRD peaks associated with cementite planes were seen at 1,073 K.
In the reduction of hematite at 973–1123 K with carbon activities 3 and 5, iron oxides were reduced to metallic iron which was converted to cementite .
In experiments at 873 with aC = 10 and 923 K with aC = 5, HT XRD spectra did not include iron ’s peaks; apparently, wüstite was directly reduced to cementite without formation of metallic iron . In general, these results are in agreement with the thermodynamic analysis, which shows that carbon activity for conversion of wüstite to cementite should be above 3.87 at 873 K and above 1.85 at 923 K (Table 2). At both temperatures 873 and 923 K, carbon activity in CO–CO2 gas for the direct reduction of wüstite to cementite is lower than that for the reduction of wüstite to iron . Nevertheless, formation of metallic iron in the reduction of hematite at these temperatures cannot be excluded; cementation of iron could be faster than reduction of wüstite to iron , what made iron ‘invisible” in the HD XRD analyses.

Lattice constants of austenite were calculated from the HT XRD spectra of samples in the process of reduction /cementation at 1073 K using CO–CO2 gas with carbon activities 3 and 10. In the experiment with aC = 3, only diffraction peaks for austenite’s planes appeared in the XRD spectrum in the 5–14 min scan. With extension of the reaction time, austenite was partially converted to cementite . Cementite was not observed in the experiment at 1073 with aC = 10; weak peaks of graphite appeared in this experiment in the scan 38–47 min.
Lattice constants of austenite and concentration of carbon in austenite in the reduction /cementation of hematite at 1073 K using CO–CO2 gas with carbon activities 3 and 10
Activity of carbon in CO–CO2 gas | Scanning time, min | d, Å | C, mass% |
---|---|---|---|
aC = 3 | 5–14 | 3.654177 | 0.486 |
19–28 | 3.675706 | 1.11 | |
aC = 10 | 5–14 | 3.658213 | 0.605 |
19–28 | 3.67633 | 1.13 |
The effective depth of X-ray penetration in the HT XRD analysis of iron powder (50 μm) obtained by the gaseous reduction of hematite assessed by Seki and Nagata [19, 20], was 1,010 μm at 2θ = 45 degrees and 2,440 μm at 2θ = 135 degrees. The thickness of pellets used in the reduction experiments was 3 mm; therefore, HT XRD analysis was representative for the whole sample; carbon concentrations assessed from the (111) spacing in Table 3, present average values of carbon concentrations in the sample.
In accordance with Grabke’s mechanism of cementite formation [12], cementation of iron requires supersaturation with carbon. Concentration of carbon in austenite in experiments at 1073 K with aC = 3, measured in 5–14 min scan, was 0.486 mass%; further iron carburisation increased carbon concentration to 1.11 mass% (19–28 min scan), what is over carbon concentration of 0.94 mass% for austenite in the equilibrium with cementite [22]. These results confirmed Grabke’s mechanism of cementite formation.
In the reduction /cementation experiment at 1073 with aC = 10, carbon concentration in austenite measured in the 5–14 min scan was 0.605 mass%. It increased above the saturation level to 1.13 (19–28 min scan), however, cementite was not observed in this experiment. Experimental conditions were more favourable for graphite (soot) deposition.
Iron cementation and soot deposition are two competing reactions in the reduction by gas with high carbon activity. Deposition of solid carbon on the sample surface blocks an access of gas with high carbon activity to the sample interior, lowering the carbon activity in the system down to one, and triggering cementite decomposition, which was observed by Zhang and Ostrovski [3–5].
However, in these HT XRD experiments, intensity of cementite peaks did not change visibly with the extension of the reaction time, and only traces of graphite were seen in the XRD analyses.
Conclusions
When carbon activity in the system was 1.5, cementite was formed only at 1023 K (750 °C); it was not observed in experiments at 973, 1073 and 1123 K (700, 800 and 850 °C).
When carbon activity was 3, cementite was formed at 923, 973, 1023 and 1073 K (650, 700, 750 and 800 °C).
Results of experiments with carbon activity 5 were similar to those obtained in experiments with carbon activity 3. The main difference was in the appearance of weak peaks of graphite.
Cementite was not observed in the reduction of hematite at 1073 K (800 °C) by CO–CO2 gas mixture with carbon activity 10.
In experiments at 923 K (650 °C), cementite was apparently formed from wüstite.
Cementite was not formed at 803 K (530 °C) (carbon activity 60) but it was observed at 873 K (600 °C) (carbon activity 10). Cementite was apparently formed from wüstite as at 923 K (650 °C).
Cementite was stable in CO–CO2 gas atmosphere; it decomposed in argon in all experiments. γ-Fe formed in the process of cementite decomposition was converted to α-Fe as a result of iron decarburisation in argon which contained 5 ppm oxygen.
In situ HT-XRD analysis provides unique data on iron carburisation/cementation.