Introduction
Lead is a toxic rather versatile and important metal due to its intrinsic association primarily with the automobile, energy storage, and nuclear industry [1]. The lead accumulator industry is the biggest consumer (~80% of total lead produced worldwide) of this non-ferrous metal in manufacturing of lead -acid batteries . Galena (PbS) is the major ore of lead along with minor contributions of other minerals like, anglesite (PbSO4) and cerussite (PbCO3) [2]. The production of lead from secondary resources by recycling is also gradually becoming the major source of lead worldwide, whose contribution in developed countries often exceeds that of the primary lead . Additionally, the occurrence of zinc-bearing ores (ZnS, ZnCO3, and Zn2SiO4) is also deplete with the significant amount of lead , and becomes rich in lead after processing the ores for recovering the primary metal, zinc from its ore bodies [3]. The lead content in the secondary materials generated is often dependent on the route adopted for the primary ore processing (pyrometallurgy or, hydrometallurgy ). Approximately 80% of zinc is produced via roasting followed by sulfuric acid leaching and electrowinning route [4], the lead forms insoluble sulfate during the hot H2SO4 acid leaching . This lead sulfate remains in the zinc -plant residue (ZPR) which is a major stockpile in the zinc producing companies, and is available to recover the valuable metals [5]. Notably, the residue generated via the top submerged lancing (TSL ) technology in zinc production contains very large amount of lead . Recovery of lead from such residue by smelting is usual practice with a higher consumption of energy because of high operating temperature ~1300 K [6]. Hydrometallurgical processing of ZPR is mainly employed to low-contents of targeted metals, and no report exists for processing of residues with high lead contents therein. In most of the cases, lead accumulated by sulfuric acid leaching as lead sulfate concentrate is also sent to the lead -smelter for its final recovery [7].
Due to the low energy requirements and lesser environmental pollution caused, many researches have been carried out to optimize the recovery of metals from the secondary resources using different lixiviants. These include sulfuric/hydrochloric acid , alkaline solutions of ammonia or caustic, brine or other chloride solutions [7–18], however no attempt seems to be made for processing of the ZPR with very high lead content. Hence in this study, leaching behavior of a TSL processed zinc-plant residue of Young Poong Zinc (South Korea) has been investigated using the NaCl solution as a lixiviant. For this, the parameters like, NaCl concentration, pulp density, and time were varied and the optimal leaching condition for maximum dissolution of lead in chloride solution was obtained. The recovery obtained at each stage of leaching was balanced with lead mass distribution between the leach liquor and residue.
Experimental
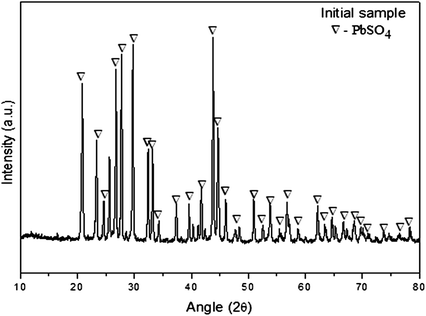
XRD pattern of the ZPR sample used in this study
Results and Discussion
Prior Extraction of Soluble Zinc from ZPR

Effect of acid concentration on zinc extraction as a function of pulp density (variation of acid cocnetration, 0−4 M H2SO4; variation of pulp density, 10−40%; stirring speed, 300 rpm; temperature , 20 °C; and time, 120 min)
Effect of Pulp Density on Lead Extraction in Brine Solution

Lead dissolution behaviour in brine solution as a function of pulp density (variation of pulp density, 10−20%; NaCl concentration, 250 g/L; stirring speed, 300 rpm; temperature , 80 °C; and time, 120 min)
Effect of NaCl Concentration on Lead Extraction

Effect of NaCl concentration on lead extraction as a function of leaching time (variation of NaCl cocnetration, 50−300 g/L NaCl; pulp density, 10%; stirring speed, 300 rpm; temperature , 80 °C; and time, up to 120 min)




As can be seen the extraction of lead increased with increasing concentration of NaCl in solution up to 250 g/L, thereafter it declined slightly. Also the leaching with ≤150 g/L NaCl was found to be totally independent to time, but at ≥200 g/L NaCl, the effect of time is visible on the leaching efficiency . The highest efficiency was achieved with 250 g/L NaCl in lixiviant and within 60 min of leaching time, however the maximum lead obtained in solution was below 50%. This limited efficiency of lead solubilization in the brine solution can be ascribed to the solubility limit of PbCl2 under the studied conditions. A limited leaching above 60 min indicates the hindrance caused by the dissociated sulfate ions from anglesite (PbSO4) minerals . With the maximum efficiency obtained with 250 g/L NaCl solution and 60 min time, the further leaching experiments were performed at the same condition.
Multi-step Leaching for the Maximum Lead Extraction
Stepwise extraction efficiency of lead from the ZPR leached in 250 g/L NaCl solution at 10% pulp density and 80 °C for 60 min
Leaching (with water washing) | Pb extraction (%) | Overall Pb extraction (%) |
---|---|---|
1st step | 57.36 | 92.03 |
2nd step | 27.84 | |
3rd step | 6.83 |
It needs to be mentioned here that only <4% of silver was analyzed in leach liquor (that too in only first step of leaching ) and no other metal get dissolved in the brine solution, showing the selectivity of this process. Furthermore, the processing of obtained leach liquor can be easily processed to recover the lead metal via cementation with metallic iron or aluminum . The applicability of cementation using (Fe0/Al0) will also be worthy by looking on the cost of the process and value of the metal recovered.
Conclusions
The simple brine leaching for lead extraction from ZPR has been investigated in the present study. The prior extraction of zinc in 0–4.0 M acid solutions was not influenced by the acid concentration in solution, and almost a similar amount of soluble zinc (56.5–60.5%, respectively) could be obtained from the ZPR. For brine leaching of the water washed ZPR, a low pulp density of 10% showed the highest lead extraction of 43.6% that also decreased with increase in the pulp density (20.4% lead extraction at 20% pulp density). The extraction of lead in the brine solutions of lower NaCl concentrations (50–150 g/L) was as low as <20%, thereafter it increased significantly up to ~48% at 250 g/L NaCl. This clearly indicates the major influence of chloride ions on the lead extraction which participated in metal complexation. A prolonged leaching however, adversely affected the lead extraction , which revealed the role played by the dissociated sulfate ions through the leaching of anglesite in brine solution. Thus optimized conditions for the maximum extraction of lead (250 g/L NaCl solution, 10% pulp density, and time 60 min) was also maintained in multi-step brine leaching , while yielding the overall Pb leaching efficiency of 92% in 3-steps. The XRD analysis of the final leach residue revealed the presence of refractory minerals of lead (Pb3O2SO4 and PbS) and zinc (ZnFe2O4, Zn3O(SO)4 and ZnS) that could not be leached in the brine solutions, leaving ~8% Pb in final residue; the residue can be sent for roasting with the primary sphalerite .
Acknowledgements
The paper is based on the Basic Research Project of the Korea Institute of Geoscience and Mineral Resources (KIGAM).