1.1 Development of Power Systems and Required High-Voltage Test Systems
Within the last 125 years, the development of transmission voltages of power systems from 10 to 1200 kV has required a tremendous development of high-voltage (HV) engineering. This includes, e.g. the introduction of many new insulating materials and technologies, the precise calculation of electric fields, the knowledge about the phenomena in dielectrics under the influence of the electric field and the understanding of electric discharge processes. Nevertheless, as an empirical technical science, HV engineering remains closely related to experiments and verifications of calculations, dimensioning and manufacturing by HV tests. The reasons for that are, e.g. unavoidable defects of the structure of technical insulating materials, imperfections of technical electrodes, but also failures of production and assembling. Therefore, in parallel to the development of HV engineering, national and international standards for HV testing have been developed, as well as equipment for the generation of test voltages and for measurements of (and at) these voltages.


History of HVAC and HVDC transmission systems
Because at direct voltage, no surge impedance becomes effective; the limitation of the power transfer capability is mainly caused by the current losses. For identical rated voltages, the HVDC power transfer capability is about three times higher than that at HVAC. This means that one 800 kV HVDC line with an efficiency of 94% replaces three 800 kV HVAC overhead lines with an efficiency of only 88% (Swedish Power Cycle 2009). But HVDC transmission requires expensive converter stations. Therefore, the application of HVDC transmission has been limited to very long transmission lines, where the cost reduction for the line compensates the higher station cost. The present cost reduction of power electronic elements, efficient HVDC cable production and other technical advantages of HVDC transmission has triggered worldwide activities in that field (Long and Nilsson 2007; Gockenbach et al. 2007; Yu et al. 2007). The historical development (Fig. 1.1) shows that the 1000 kV level is reached in China now, but the next levels above 1000 kV or more are under preparation (IEC TC115 2010).
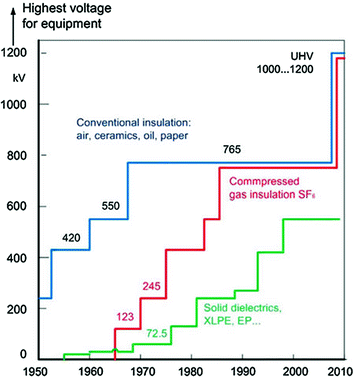
History of the application of insulating materials

The idea of a global-spanning super-grid
The basic principle of HV testing expresses that test voltages stresses shall represent the characteristic stresses in service (IEC 60071-1). When electric power transmission started, not all these stresses were known. Furthermore, the kind and height of stresses depend on the system configuration, the used apparatus, the environmental conditions and other influences. The historical development of HV testing is closely related to the development of and the knowledge on power systems. It can be characterized by the following steps:

Historical test voltage generators a world’s first 1000 kV cascade transformer (Koch and Sterzel Dresden 1923) b 1000 kV DC test voltage generator (Koch and Sterzel Dresden 1936) c 2000 kV LI test voltage generator (Koch and Sterzel Dresden 1929) d 7000 kV LI/SI test voltage generator (TuR Dresden 1979)
But independently on the performed HVAC tests, equipment has been destroyed in power systems, e.g. as a consequence of lightning strokes, which caused external over-voltages . These overvoltage impulses are characterized by front times of few microseconds and tail times of several ten microseconds. Based on that knowledge, tests with lightning impulse (LI) test voltages (front time ≈ 1…2 μs, time to half-value ≈ 40…60 μs) have been introduced in the 1930s. For LI voltage testing, suited generators have been developed (Fig. 1.4c, see also Sect. 7.1).
Another 30 years later, it has been found that internal over-voltages lead to lower breakdown voltages of long air gaps than LI or AC voltage stresses. They are caused by switching operations in the power system. Their durations lay between some hundreds of microseconds and few milliseconds. As a consequence, switching impulse (SI) test voltages have been introduced in the 1960s. SI test voltages can be generated by the same type of generators as LI test voltages (but with larger HV electrodes for better control of the electric field, Fig. 1.4d, see also Sect. 7.1) or by test transformers.
Again 30 years later, it has been found that disconnector switching of gas-insulated substations (GIS) causes oscillating over-voltages of very fast front (VFF, several ten nanoseconds) which may harm the GIS insulation itself, but also attached equipment. Whereas a test with very fast front (VFF) test voltage has been introduced for GIS, it is under discussion for other components of power systems (Sect. 7.1.5).
The mentioned overvoltages are superimposed on the operational voltages. The traditional HV testing of components of HVAC power systems must not consider the operational voltage, only for special cases, e.g. disconnectors or three phase GIS busbars, the superposition plays a role. Therefore “mixed voltages” of two voltage components have been introduced. Depending on the position of the insulation in a test, one distinguishes between “combined test voltages” for three-pole test objects (e.g. disconnectors) and “composite test voltages” for two-pole test objects (e.g. polluted insulators), for details see Chap. 8. In case of HV testing of components of HVDC power systems, composite test voltages, play a very important role because of the space charge generation at DC voltages.
1.2 The International Electrotechnical Commission and Its Standards
The International Electrotechnical Commission (IEC) is the worldwide organization for international standards on electrical engineering, electronics and information technology. It has been founded in 1906, and its first president was the famous physicist Lord Kelvin. Today, about 60 national committees are IEC members. During its first years, IEC tried to harmonize the different national standards. But now, more and more national committees contribute to maintaining existing or establishing new IEC standards which are later overtaken as national and regional standards (e.g. CENELEC Standards of the European Union). This book refers mainly to IEC Standards and mentions also relevant standards of the US organization “Institute of Electrical and Electronic Engineers” (IEEE) which play an important role in some parts of the world. IEEE publishes also “IEEE Guides” which may overtake the role of missing text books. The IEEE Guides supply only recommendations and no requirements as standards are doing. The actual trend shows a closer cooperation between IEC and IEEE for the harmonization of IEC and IEEE Standards.

Structure of the International Electrotechnical Commission (IEC)
The technical committees for horizontal and vertical standards

This book is closely related to the tasks of the TC 42 “High-voltage and high-current test techniques”. It explains the scientific and technical background of the TC 42 standards, but cannot replace any of them. Rather, it should be understood as an application guide to the relevant IEC Standards and stimulate their application.
1.3 Insulation Coordination and Its Verification by HV Testing
In service, an electrical insulation is stressed with the operational voltage (including its temporary increase, e.g. in case of a load drop) and with the over-voltages mentioned above. The reliability of a power system has to be guaranteed under all possible stresses of its insulations. This is realized by the insulation coordination and described in the relevant group of IEC Standards (IEC 60071).
Insulation coordination is the correlation of the withstand voltages of different apparatus in a power system among each other and with the characteristics of protective devices . Today, protective devices (IEC 60099-4 2009) are mainly metal oxide arresters (MOA) , and partly conventional silicon carbide arresters with internal gaps and protection air gaps are still in use. An ideal protective device conducts electric current for voltages above the protection level and is an insulator below that voltage (A MOA is near to that characteristic). In the design of a power system, protective devices are installed at sensitive points, guaranteeing the protection level and protecting the insulation from excessive over-voltages.
Standard insulation levels for HVAC equipment Vm = 3.6–245 kV (IEC 60071-2: 2006)
Highest voltage for equipment Vm kV (rms, phase-to-phase) | Short-duration AC withstand voltage Vt kV (peak/√2, phase-to-earth) | LI withstand voltage Vt kV (peak value) |
---|---|---|
3.6 | 10 | 20 |
10 | 40 | |
7.2 | 20 | 40 |
20 | 60 | |
12 | 28 | 60 |
28 | 75 | |
28 | 95 | |
24 | 50 | 95 |
50 | 125 | |
50 | 145 | |
36 | 70 | 145 |
70 | 170 | |
72.5 | 140 | 325 |
123 | (185) | (450) |
230 | 550 | |
145 | (185) | (450) |
230 | 550 | |
275 | 650 | |
170 | (230) | (550) |
275 | 650 | |
325 | 750 | |
245 | (275) | (650) |
(325) | (750) | |
360 | 850 | |
395 | 950 | |
460 | 1050 |
Standard insulation levels for HVAC equipment Vm = 300–1200 kV (IEC 60071-2: 2006), (IEC 60071-2-Amendment 2010)
Highest voltage for equipment Vm kV (rms, phase-to-phase) | SI withstand voltage kV (peak value) | LI withstand voltagec Vt kV (peak value) | ||
---|---|---|---|---|
Longitudinal insulationa | Phase-to-earth insulation | Phase-to-phase insulationb | ||
300 | 750 | 750 | 1125 | 850 |
750 | 750 | 1125 | 950 | |
750 | 850 | 1275 | 950 | |
750 | 850 | 1175 | 1050 | |
362 | 850 | 850 | 1275 | 950 |
850 | 850 | 1275 | 1050 | |
850 | 950 | 1425 | 1050 | |
850 | 950 | 1425 | 1175 | |
420 | 850 | 850 | 1360 | 1050 |
850 | 850 | 1360 | 1175 | |
950 | 950 | 1425 | 1175 | |
950 | 950 | 1425 | 1300 | |
950 | 1050 | 1575 | 1300 | |
950 | 1050 | 1575 | 1425 | |
550 | 950 | 950 | 1615 | 1175 |
950 | 950 | 1615 | 1300 | |
950 | 1050 | 1680 | 1300 | |
950 | 1050 | 1680 | 1425 | |
950 | 1175 | 1763 | 1425 | |
1050 | 1175 | 1763 | 1550 | |
800 | 1175 | 1300 | 2210 | 1675 |
1175 | 1300 | 2210 | 1800 | |
1175 | 1425 | 2423 | 1800 | |
1175 | 1425 | 2423 | 1950 | |
1175 | 1550 | 2480 | 1950 | |
1300 | 1550 | 2480 | 2100 | |
1200 | 1425 | 1550 | 2635 | 2100 |
1425 | 1550 | 2635 | 2250 | |
1550 | 1675 | 2764 | 2250 | |
1550 | 1675 | 2764 | 2400 | |
1675 | 1800 | 2880 | 2400 | |
1675 | 1800 | 2880 | 2550 |
For equipment of Vm = 3.6–245 kV, the AC voltage test covers also withstand against internal (switching) over-voltages and no SI impulse voltage withstand test is specified. For equipment of Vm = 300–1200 kV, the switching impulse test covers for air insulations also the AC voltage test; for internal insulations, the AC test voltages are specified in the relevant apparatus standards.
Simplified example for the selection of withstand test voltages for three protection levels


Highest withstand test voltages for HVAC equipment and selection of impulse voltage test systems
Example: For a transformer test field, the selection of the rated voltage of an impulse voltage test system (equal to the cumulative charging voltage of the generator, see 7.1.1) shall be shown. Outgoing from the highest test voltage (LIC in Fig. 1.6), one has to consider that the utilization factor for large test objects may go down to
. Furthermore, for internal development tests, a test voltage 20% higher than the LIC withstand voltage might be necessary. This means the rated voltage of the impulse voltage test system should be by a factor k = 1.2/0.85 ≈ 1.4 higher than the highest LIC test voltage. This means that for the rated voltage Vm = 800 kV, a 3000 kV impulse test system is sufficient. If a later extension of the test capability to 1200 kV equipment is planned, a 4000 kV test system should be considered. The selection of impulse test systems according to Fig. 1.5 is recommended.

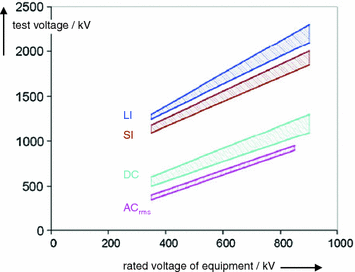
Withstand test voltage ranges for HVDC equipment
1.4 Tests and Measurements in the Life Cycle of Power Equipment
The principles of insulation coordination are only applied to new equipment and verified in factory tests. These include type tests and routine tests . Both tests are quality tests of the insulation; a successful type test demonstrates the correct design according to the test voltages (Tables 1.2 and 1.3), and a successful routine test verifies the correct production according to the confirmed design. The two tests are not the only tests in the life cycle of the insulations of power equipment (Fig. 1.8).

Tests and measurements in the life cycle of HV insulation
After the correct quality is confirmed in a successful on-site test, the equipment is overtaken to the user who has the full responsibility for all further (diagnostic) tests and measurements now. It will be commissioned and has to operate under electrical, thermal, mechanical and/or environmental influences. These influences cause an ageing process of the insulation until—after tens of years—the end of the life cycle is reached. In the past, the duration of the life cycle has been estimated and the end of use has been defined by the user independently on the real condition of the equipment. To reduce the life cycle cost, tests and measurements have been introduced for condition assessment of the insulation and estimation of the remaining life time (Zhang et al. 2007; Olearczyk et al. 2010; Balzer et al. 2004). In opposite to the quality tests, these tests for condition assessment shall be called diagnostic tests . There are no standards for diagnostic tests, only recommendations by organizations (like CIGRE or IEEE) who provide technical guides, by service providers or by equipment suppliers.
Both quality and diagnostic tests require a test voltage application and measurements (in minimum a voltage measurement, but very often partial discharge or dielectric measurements). A withstand test is a direct test , which is directly related to the insulation capability of the test object. A healthy insulation which passes the test has a high withstand voltage. A defective insulation has a low withstand voltage and fails the test (This is much better than it fails in service!). It must be considered that a voltage stress may cause life-time consumption. An insulation shall be designed in such a way that the life-time consumption of the healthy insulation is negligible during a withstand test, whereas a defective insulation breaks down. When a withstand test is completed by a parallel partial discharge (PD) measurement (see Sect. 2.5), it can be excluded that such a successful “PD-monitored” withstand test has caused or enlarged insulation defects.
When a diagnostic test is decided according to measurements of a single parameter or a set of parameters (preferably of partial discharges), the test result must be compared with pre-given limits. These limits shall be related by experience or any physical model to the remaining life time. The sharpness of such an indirect test is lower than that of a monitored withstand test. Sometimes, it is published that withstand tests are “destructive” and diagnostic measurements are “non-destructive”. Such qualifying terms are not suited to describe the quality and sharpness of a diagnostic HV test.
Diagnostic measurements performed at operational voltage in service are called on-line monitoring (CIGRE TF D1.02.08 2005) (Monitoring is not only related to dielectric measurement; there is also monitoring of voltage, current, thermal or mechanic parameters). Automatic monitoring delivers a warning when the measured parameter exceeds a preset limit.
This brings one back to Fig. 1.7: In service, online monitored data deliver the data trend, describe the situation and may supply data for maintenance. In case of a warning by the monitoring system, the reason of the defect must be clarified. Often, the monitored data are not sufficient for a clarification. In that case, a more detailed investigation is necessary, e.g. by an (off-line) on-site test including appropriate measurements. This test with a separate test voltage source enables a withstand voltage test (with a test voltage value well adapted to the age of the insulation) and the measurement of the parameters depending on the applied voltage (instead of only one fixed voltage at monitoring). After the condition of the insulation has been clarified, it might be decided to repair the equipment in the factory or on site. Then, one or several loops in the scheme appear, and one has to go back to on-site testing and service again. At the end of the life cycle, the equipment is dismantled and also this may deliver some data for future development.
The data of all tests and measurements during the life cycle must be recorded in the—preferably electronic—life cycle record of the equipment. The life cycle record is the most important document of the equipment, which delivers the trend of parameters and enables qualified decisions. As all stages of the life cycle are connected together, it must be stressed that quality and diagnostic testing have a common physical background. This is often forgotten, when quality testing and diagnostic testing/monitoring are considered separately. The only reference for all HV quality on-site tests of new equipment is the factory testing based on the test voltages of the insulation coordination. This may include that also the test voltages for diagnostic testing of service-aged equipment should be in close relation to stresses in service.