6.1 Circuits for the Generation of HVDC Test Voltages
Today, HVDC test voltages are generated by rectification of HVAC voltages of transformers (see Sect. 3.1.1). Modern solid state rectifier elements, in the following “diodes” (silicium diodes), enable the generation of all necessary test voltages and currents, but the limitations in the reverse voltage to few 1000 V require the series connection of these diodes for HV rectifiers with reverse voltages up to several 100 kV’s or even MV’s. When the circuits for HVDC test voltage generation are considered, all mentioned rectifiers are HV rectifiers assembled from many diodes (see Sect. 6.2.2).
6.1.1 Half-Wave Rectification (One-Phase, One-Pulse Circuit)


One-phase, one-pulse half-wave rectification, a equivalent circuit diagram, b feeding AC voltage and DC voltage with ripple, c modular test system for HVDC 135 kV/10 mA and HVAC 100 kV/11 kVA



The lower the ripple, the smoother is the HVDC test voltage. The ripple decreases with increasing load resistance (This means with decreasing load!), increasing load capacitance and increasing frequency of the charging AC voltage. But, in case of half-wave rectification, the ripple remains quite large. Equation 6.2 shows additionally that the feeding HVAC transformer circuit must be able to supply a sufficient current i(t).
Note According to IEC 60060-1:2010, the voltage drop is the “instantaneous reduction of the test voltage for a short duration of up to few seconds”. Here, it will be used according to this definition. In literature, e.g. Kuffel et al. (2006) or Kind and Feser (1999), the term voltage drop is used for the continuous voltage reduction between the no-load case and the load case, especially of multi-stage cascades. The term “voltage reduction” will be used for this phenomenon in the following. The voltage reduction is caused due to the “forward voltage drop” and the internal resistance of the rectifiers.

One-phase two-pulse half-way rectification
6.1.2 Doubler and Multiplier Circuits (Greinacher/Cockcroft-Walton Cascades)
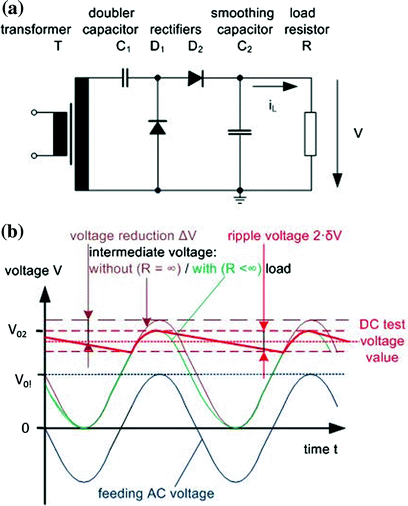
One-phase, one-pulse doubler circuit with half-wave rectification, a equivalent circuit diagram, b AC feeding, oscillating intermediate and DC voltages (R → ∞), c modular test system with doubler circuit 270 kV/10 mA







Greinacher cascade (one-phase, one-pulse multiplier circuit), a equivalent circuit diagram, b potential at the three stages, c generator with 500 kV per stage for 1500 kV/30 mA
The direct voltage per stage is twice the peak voltage Vmax of the feeding alternating voltage. In stationary operation and rated voltage, the necessary
reverse voltage
of the rectifiers is . Doubler capacitors (except that of the lowest stage) must be able to withstand a DC stress of
plus the AC stress of the feeding voltage. Smoothing capacitors have to withstand a direct voltage of
. The lowest doubler capacitor is only stressed with half of that voltage but causes the largest contribution to the ripple. Therefore, it should have the double value of the capacitance, this fits to the voltage distribution and reduces the ripple. The 1500 kV cascade with a stage voltage of 500 kV—shown in Fig. 6.4c—is fed for its rated voltage with an AC voltage of 250 kV/√2 = 177 kV (rms).



For practical cases, the voltage reduction can be remarkably higher than expressed by Eq. (6.5) which considers only the parameters of the generator. Mainly, stray capacitances in the feeding circuit cause an additional voltage reduction (Spiegelberg 1984).
Greinacher cascades are the most applied generators in HVDC testing. The polarity can be reversed by turning the rectifiers inside the generator by hand or motor. They are well suited for capacitive test objects, but have limits in case of a resistive load. The ripple can be reduced and the efficiency factor improved when the smoothing capacitances C and the frequency f of the feeding voltage are increased. AC feeding voltages of higher frequencies are traditionally generated by motor-generator sets, but nowadays static frequency converters should be applied. Furthermore, the number of stages should be limited and the stage voltage increased as much as possible. For rated currents above 100 mA, more efficient circuits should be applied.
6.1.3 Multiplier Circuits for Higher Currents

Symmetric Greinacher cascade (one-phase, two-pulse multiplier circuit)

Three-phase, six-pulse multiplier circuit
Comparison of voltage reduction and ripple for multiplier circuits of n stages (The terms “x” and “y” are the factors according to lines 2 and 3 for the n = 5 stages.)
Type of circuit parameter | Greinacher cascade (one-phase, one-pulse multiplier circuit) (Fig. 6.4) | Symmetric Greinacher cascade (one phase, two pulse multiplier circuit) (Fig. 6.5) | Three-phase, six-pulse multiplier circuit (Fig. 6.6) |
---|---|---|---|
Voltage reduction ΔV |
|
|
|
Ripple voltage δV |
|
|
|
Example n = 5: | x = 85 (assumed to be 100%) | x = 16.25 (19%) | x = 5.4 (6.3%) |
Example n = 5:
| y = 7.5 (assumed to be 100%) | y = 1.25 (16.7%) | y = 0.42 (5.6%) |
6.1.4 Multiplier Circuits with Cascaded Transformers (Delon Circuits)

Multiplier circuit with cascaded transformers

Greinacher cascade with feeding into the sixth stage, a simplified circuit diagram, b generator for 2000 kV and for very fast polarity reversal up to 700 kV

Simplified circuit diagram of a HVDC module with two internal stages

Modular HVDC generators, a 800 kV/30 mA of two modules, b 2200 kV/10 mA of 7 modules in parallel-series connection. Both generators with external blocking impedance and PD coupling capacitor (size of modules is identical in both pictures!)
6.2 Requirements to HVDC Test Voltages

Definitions to direct test voltages
6.2.1 Requirements to HVDC Test Voltages

The tolerance of the test voltage value is 1% for test durations up to 1 min, but for longer durations, 3% are acceptable. The definition of the mean value Vm results mainly from the voltage measurement with conventional voltmeters (moving-coil meters) which measure the mean value. One has to consider that the peak voltage Vmax determines breakdown processes and must be applied for research work.

The requirement δ ≤ 3% accepts that a remarkable difference appears between the peak voltage—which determines discharge phenomena in the insulation—and the test voltage value. A high ripple reduces also the inception voltage of partial discharges. Therefore, for both sides of an acceptance test, it is useful to have a ripple factor as low as possible.

Unfortunately, IEC 60060-1:2010 does not specify the current value and its duration, e.g. for an assumed rectangular pulse or any indication of the required charge. For more details, see Sect. 6.2.3.2. Some publications consider dV ≤ 10% as a too high value, (e.g. Hylten-Cavallius 1988; Köhler and Feser 1987). See also Sect. 6.2.3.2 below.
The reference value of the parameters δ and dV is always the measured test voltage value Vm. Therefore, the voltage reduction ΔV (Eq. 6.5) is not a parameter of the test voltage, but of the HVDC test system. It characterizes the utilization factor of the used test system and has to be considered when a new test system is required.
6.2.2 General Requirements to Components of HVDC Test Systems
The circuit diagrams discussed above are simplified because they consider ideal elements and stationary conditions. Additionally, a HVDC generator has to withstand also transient stresses, e.g. in cases of a breakdown of the test object or a fast polarity reversal. If no countermeasures are taken, the stray inductances and capacitances would influence the distribution of the stressing voltages inside the generator. Furthermore, high breakdown currents have to be taken into consideration.
6.2.2.1 Protection Against Transient Stresses

Example of a protection circuitry of the diodes in a rectifier
Note The protection scheme operates only if a breakdown occurs at the test object connected via the external damping resistor. A breakdown between any point of the generator and any grounded or energized object, e.g. due to wrong arrangements in the HV test hall, may change the relation between the single components of the protection scheme in such a way that rectifiers and/or capacitors of the generator are endangered.
6.2.2.2 Polarity Reversal and Switch-off

Polarity reversal, a switching process of the rectifiers, b definition of the reversal time
Under certain conditions a much faster polarity reversal is required, e.g. within 200 ms. For that, the reversal time is defined as the interval between 90% of the outgoing voltage and the same 90% value of the opposite polarity (Fig. 6.13); whereas, the discharge phase is fast enough, the charging phase must be accelerated. This is realized by selecting a rated value for the charging much higher than necessary and interrupting the charging when 90% of the required voltage is reached (t4). To avoid an overshoot of the opposite polarity, the feeding must be pulse-controlled to the exact voltage value.

Grounding of small HVDC generators
When the HVDC test system is designed for polarity reversals as described above, then the capacitors might be discharged via the turning rectifiers. After the feeding AC voltage is switched off, the grounding procedure starts with the discharge via the divider resistor down to about one-third of the rated voltage before the rectifiers are applied. They should not be applied for higher voltages to avoid an over-stress of the rectifiers. The permanent grounding of the capacitor columns shall only be used, after the generator is discharged. This can be done by earthing ropes or—for generators of rated currents up to several 10 mA by earthing switches (see Sect. 9.26 and Fig. 9.28). For discharging high capacitances see Sect. 6.2.3.1!
A new HVDC generator should be equipped with a well-established protection scheme and with a reliable discharge and grounding system. When the generator is not used, it shall be carefully grounded. For safety reasons, all capacitors of each stage of multi-stage generators must be directly grounded by a metal rope which can be moved through the generator by motor preferably. If protection scheme and grounding system of an older generator do not correspond to these requirements, an upgrade is urgently recommended.
6.2.2.3 Voltage Control, Selection of Smoothing Capacitances and Frequency
The output of the HVDC generator is controlled via the feeding AC voltage. This means that the control is one of the AC generation circuit. Traditionally, this is a regulating transformer and nowadays mainly a thyristor controller operating in a pulse-width mode. The wider the voltage pulse the higher is the output voltage. The shape of the AC voltage is not important for the output DC voltage because the HVDC generator can be understood as a filter which connects harmonics of the alternating voltage to ground. The DC output voltage is hardly influenced by conducted noise signals. The thyristor controller can be switched within less than a millisecond, what is necessary for the mentioned fast polarity reversals. When a very sensitive PD measurement shall be performed at direct voltage, the switching pulses of the thyristor controller could disturb. In such cases, the application of a regulating transformer can be recommended instead of or in addition to the thyristor controller.
With respect to voltage reduction and ripple, capacitance and frequency are interchangeable (Table 6.1). This means the system can be improved either by increasing the capacitances or by increasing the frequency of the feeding voltage. Of course, also both can be applied for improving a design. It must be taken into consideration that the frequency range of capacitors is limited. Capacitors for frequencies >300 Hz are remarkably more expensive than those for power frequency. Therefore, the selection of capacitances and frequencies of the feeding voltage should take the economic situation into account. There is no general rule for an optimum now. Each design and parameter combination has to be considered separately for a reasonable economic solution.
In the past, motor-generator sets have been applied for the generation of AC voltages of higher frequencies than 50/60 Hz for HVDC test systems. Today, static frequency converters are available (Figs. 3.26 and 3.35) and connect the selectable higher frequencies with the advantages of a thyristor controller. It can be assumed that in the next future, the power supply and control of HVDC test systems will be based on static frequency converters.
6.2.3 Interaction Between HVDC Test System and Test Object
HV testing requires the consideration of test circuits including test objects on the basis of the relevant standards. The standards of HVDC power systems are under a rapid development, a final survey cannot be given now. The IEC Technical Committee 115 on HVDC Power Transmission Systems is preparing the necessary basic standards. A survey on components of HVDC power transmission—including their HV testing—is e.g. given in the IEC Document 115/154/CD:2017. One should follow the related development of standards with the knowledge about the physical processes as tried to explain it in the following.
6.2.3.1 Capacitive Test Objects

Field strength distribution influence by space charges (explanations in the text), a sample made of “AC Polyethylene”, b sample made of “DC Polyethylene”
- (a)
For “AC XLPE” as it is used in HVAC cables , one observes during and for a certain time after the HVDC charging of the cable sample a field strength distribution with the maximum at the inner electrode as expected for a coaxial system (Fig. 6.15a: Laplace field, blue). After 5 h due to space charges the maximum has shifted to the outer electrode (dotted, green), but when steady-state conditions are reached (e.g. after 2180 h, red) space charges of opposite polarity generate an extreme maximum of field strength near to the inner electrode. This would not be acceptable for real HVDC cables.
- (b)
Therefore “DC XLPE” has been developed using special additives to the polyethylene, which prevent a high space charge field near the inner electrode (conductor) (Fig. 6.15b). This guarantees a quite uniform and very stable steady-state of the insulation (field strength distribution after 5 h (dotted, green) and 2180 h (red) are practically identical). Also depending on the applied DC voltage the characteristic of the distribution is not changed. “DC XLPE” is well suited for HVDC cables.
The selection of the test duration has to consider the space charge behavior of the insulation and is quite difficult. This includes also different charging and discharging processes.
For charging currents of usually 3–10 mA, the charging may take up to several minutes. For example, the controlled charging of a 10 km long HVDC cable system, (about 2 μF) to a test voltage of 250 kV with a constant current of 5 mA would take nearly 2 min. Even during that short time, the generation of space charges cannot be excluded. After the test voltage value is reached, the shift of the field strength distribution to the steady-state (Fig. 6.15b) takes place.

In the mentioned example of the 10-km cable and Vt = 250 kV the stored energy is 62.5 kJ which may be discharged within few seconds. The damping resistance must be able to absorb this energy. Therefore, a wire resistor needs a careful thermal design. With respect to the recovery voltage (see Chap. 5), it is necessary to guarantee a permanent grounding of the generator and the capacitive test object when not in use.
The CIGRE Working Group B1.32 summarized the state of the art on the behavior of DC XLPE insulation and published the Technical Report 496 (2012) on the testing of extruded HVDC cables which acts as a certain standard. The report comprises the electrical tests for transmission cables using the phase-to-ground voltage V0 under operational conditions as the reference voltage:
Prequalification tests
of cable systems shall demonstrate the satisfactory long term performance of all components in an about 100 m long cable system. It is made only once during the development and includes a long duration voltage test at Vt = 1.45 V0 of different cycles with and without load current generated by a cable heating equipment (in total of 360 days). It is completed by polarity reversal and composite voltage tests (superimposed voltage tests: DC/LI and DC/SI), Finally a detailed inspection shall be made.
Type tests
are made before supplying cable systems on a general basis to demonstrate satisfactory performance characteristics. It is made at Vt = 1.85V0 for 30 days on cable loops typical for the cable system. The type test include load cycles, polarity reversal test, DC/LI and a DC/SI composite voltage test followed by a HVDC test.
Routine tests
(factory acceptance tests) are made on each manufactured component (cable or accessories) to verify that they meet the specific requirement. Each delivery length of cable shall be submitted to a negative DC voltage for one hour. The CIGRE WG expresses that in addition to the DC test voltage an AC voltage test, which enables PD measurement, can be considered, provided the cable design allows AC application. Also for the cable accessories PD-monitored AC voltage tests might be useful.
On-site acceptance test
(after–installation tests) shall demonstrate the integrity of the cable system as installed. The installed cable system shall be subjected to a negative HVDC test of , details must be agreed between supplier and user.
HVDC super-long cables : The charging and especially the discharging of the cable systems under test becomes really difficult if e.g. a large submarine cable (e.g. Vm = 550 kV, 200 km long, corresponding to 70 µF, e.g. see Fig. 1.3) is tested for commissioning (Vt = 1.45 ·Vm = 800 kV). The energy stored in the cable is about 22 MJ. The discharging of this example has been investigated by Felk et al. (2017):
The discharging due to the resistance of the cable insulation itself would take nearly 10 h. This means, the cable would be stressed much longer than during the test of e.g. 1 h. Furthermore no wire resistor has the necessary thermal capacity to overtake the energy. Therefore a HVDC discharge device based on an water filled vertical resistor is proposed. A water processing unit—as used for water end terminations for cable testing (see Fig. 3.44)—controls the value of the conductivity of the water. The processing unit increases the water conductivity by dosing salt into the water, and reduces it by a special resin bed for de-ionization. Because the water is heated due to its resistance, it is also cooled in the processing unit. The water circulates in the resistor, which consists of an inner tube (where the water goes up) and an outer tube (where the water goes down). The electric field between the two tubes as well as in vertical direction must be carefully designed. The thermal design should avoid dew on the outer surface of the resistor. The resistor can be connected of 400 kV modules with a water volume of about 70 litres each. For example, the 800 kV water resistor would consist of two modules and is always connected in parallel to the cable under test.
The water resistance is controlled so that it is very high during charging and testing the cable (which means with a very low influence on the HVDC voltage source) and low for discharging the cable. The thermal capacity of the water is so high that the energy of 22 MJ will increase the water temperature only by 40 K! For a new test the water must be cooled down and de-ionized.
Liquid-impregnated paper-insulated (LIP) HVAC cables : In some respect, HVDC testing of HVAC LIP cable systems is the classic example for direct voltage application to AC insulation, especially for testing on site (see Sect. 10.4.2). Therefore, the HVDC testing of HVDC cable systems does not cause new problems. Quite small HVDC test systems are able to charge the high capacitance of a LIP cable system. Also a certain relationship between the lifetime under AC operational stress and the results of suited HVDC tests has been found.
a DC voltage withstand test,
an AC voltage withstand test,
PD measurement at DC and AC voltage,
a polarity reversal DC test (see Sect. 6.2.2.2),
a DC/LI composite voltage test (see Sect 8.2.3),
a DC/SI composite voltage test (see Sect. 8.2.3),
load condition test (withstand tests at rated current),
an insulation system test on single components (withstand and PD ≤ 5 pC).
With respect to the high effort of the type test, the routine tests and the on-site acceptance tests shall be simple and time efficient. This cannot be reached with DC voltages. As an acceptable compromise, these tests shall be performed at AC voltages and completed by PD measurement.
Finally a prototype installation test , similar to the pre-qualification test of cable systems (see above) is being discussed (Neumann et al. (2017). This test shall demonstrate the long-time performance of the complete gas-insulated HVDC system (expected life time of 50 years). It is a long time test for 30 days containing load cycles and composite DC/LI and DC/SI voltage tests (see Sect. 8.2.3). For the load cycles a DC current corresponding to the rated current shall be injected. It requires a special current source for operating on HVDC potential (Neumann et al. (2017)).
6.2.3.2 Resistive Test Objects (Wet and Pollution Tests)
Wet and pollution tests require an active current due to a low surface resistance and/or to heavy predischarges. The limitation of the required current by the HVDC test system leads to a limitation of the test voltage (voltage reduction ΔV) in case of a permanent stress in stationary operation and to an instantaneous voltage drop (dV) in case of transient stress. In both cases, the test cannot be performed correctly. Therefore, a lot of research work has been related to amplitude and shape of the required current (e.g. Reichel 1977; Rizk 1981; Matsumoto et al. 1983; Kawamura and Nagai 1984; Merkhalev and Vladimirsky 1985; Rizk and Nguyen 1987; Cigre TF 33.04.01, 2000). As a result, the IEC Technical Standard 61245:2015 gives hints for HVDC pollution testing, and the necessary specification of HVDC test systems (ripple factor ≤3%, voltage drop ≤10%, voltage overshoot ≤10%, voltage measurement for both, continuous and transient voltage components). The practice of HVDC pollution testing is described in several publications, e.g. Windmar et al. (2014).
Whereas the voltage reduction becomes only acceptable, when a HVDC test system of sufficient rated current is applied, the voltage drop dV can be reduced to an acceptable value by a very large smoothing capacitor, possibly by an additional capacitor (Reichel 1977; Spiegelberg 1984) or by a feedback control with a higher feeding voltage (Köhler and Feser 1987).
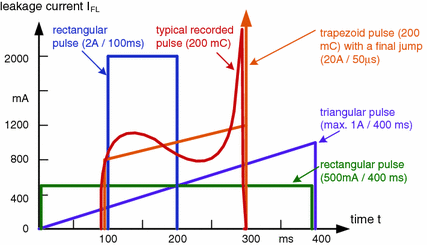
Leakage current impulse (red) and its simplified replacements for calculations



Output voltage of a HVDC generator (Fig. 6.19) depending on amplitude and duration of a rectangular leakage current impulse

Voltage drop for current pulses of rectangular and trapezoid shape

Circuit diagram of a HVDC test system with feedback control

Calculated output voltage of a feedback-controlled generator at different leakage currents, but identical pulse charge Qp = 200 mC
HVDC pollution tests must not be performed at complete insulator chains; it is sufficient to test one insulator of a chain because a linear voltage distribution can be assumed within one chain of uniform pollution. Therefore, powerful HVDC test systems for pollution tests are usually limited to test voltages up to 600 kV.
In opposite to that, for insulators under artificial rain conditions, no uniform voltage distribution can be assumed, therefore wet tests must be performed up to the highest DC test voltages. This means HVDC test systems for rated voltages of 2000 kV are able to test open air insulations for 1000 kV HVDC transmission systems. Current pulses due to heavy streamer discharges in transition to leader discharges are characterized by charges up to 10 mC. These charges can be supplied by generators without feedback control and rated currents of few 100 mA. If it shall also be used for wet testing of contaminated insulators higher rated currents and feedback control might be useful (Su et al. 2005).
6.2.3.3 Corona Cages and HVDC Test Lines
A remarkable part of the active losses of an air insulated HVDC transmission system is caused by partial discharges which are usually designated “corona” discharges . The design of the bundle conductors of a HVDC transmission line is usually verified by tests in a corona cage and/or on a test line. A corona cage is a coaxial electrode system with an outer electrode up to few metres diameter, realized by metal rods, and the bundle conductor to be investigated forms the inner electrode on HVDC potential. The outer electrode is grounded via an impedance for measurement of corona current pulses or the average corona current. A HVDC test line is a one-to-one model of a future HVDC overhead line. It shall demonstrate the performance of all components under operational conditions. Both, corona cages and test lines are outdoor arrangements and require outdoor HVDC test systems (Elstner et al. 1983; Spiegelberg 1984).

Bipolar HVDC attachment of ±1000 kV/500 mA to a 600 kV/3.3 A HVAC test system.
Courtesy of KEPRI Korea
The test system itself must withstand its output voltage at all environmental conditions under which tests shall be performed. The details of those conditions (temperature range, atmospheric pressure range, humidity up to 100%, rain, natural contamination) must be carefully specified as well as a possible reduction of the rated voltage for certain test conditions. The external surface of all components shall be equipped with silicon rubber sheds (Fig. 6.21).
6.3 Procedures and Evaluation of HVDC Tests
Developed for all continuous voltages, the procedures and evaluations of HVAC tests (see Sect. 3.3 based on Sect. 2.4) can be applied for HVDC tests, too. Therefore, the described methods will not be repeated in this section, only few differences shall be mentioned.
The progressive stress test with continuously or step by step increasing direct voltage (Fig. 2.26) is used to determine a cumulative frequency distribution which can be approximated by a theoretical distribution function. The approximation can be performed according to the recommendations of Table 3.7. Also for life-time tests the remarks of Sect. 3.3.1 are applicable.
Compared with HVAC tests, it is more difficult to guarantee independence in HVDC tests. The reason is based on the phenomenon that partial discharges (and the trace of flashovers) at direct voltage cause surface and space charges of a long lifetime. Therefore, preceding stresses may influence the result of following stresses. It is absolutely necessary to check the independence of a test result before a further statistical evaluation will be made. The graphical check (Fig. 2.28) should be performed during the tests, and the test procedure should be modified if independence appears. Modifications are, e.g. the change of the rate of voltage rise, the careful cleaning of test objects after flashovers, the application of a new test object for each stress cycle or the application of a low alternating voltage between two stress cycles (“cleaning” by an alternating electric field). When a solid insulation is investigated, usually each test cycle requires a new sample.
In quality-acceptance testing, the procedure described in Sect. 2.4.6 and Fig. 2.39a is recommended also for direct voltages (IEC 60060-1:2010). The test should be performed at the polarity which delivers the lower breakdown voltages. If this is not clear testing at both polarities is necessary. Also PD-monitored withstand tests (Sect. 3.3.2) are applicable, but the randomness of partial discharges at direct voltage shall be considered (see Sect. 6.5). This may require longer durations on the different voltage levels (Fig. 2.39b). Other measurands than partial discharges, e.g. the leakage current or the insulation resistance, might be taken into consideration for diagnostic withstand testing.
6.4 HVDC Test Voltage Measurement
To measure high DC voltages up to some hundreds of kV originally sphere gaps have been used. As already pointed out in Sect. 2.3.5, based on experimentally determined breakdown curves of sphere gaps under clean laboratory conditions, a measuring uncertainty of about 3% is achievable for voltages ranging between 20 kV and about 2000 kV (Schumann 1923; Weicker 1927; Weicker and Hoercher 1938; IEC Publication 52:1960). However, the breakdown voltage of sphere gaps is not only affected by nearby earthed objects (Kuffel 1961) but also by the roughness of the electrodes as well as by dust and pollution deposited on the electrode surface, and as usual by the humidity and density of the ambient air. As charged particles are always attracted into direction of increasing electric field strength, which forces the deposition of dust particles on the electrode surface, the use of sphere gaps for measuring DC voltages above 200 kV is not recommended (see Table 2.7).

Basic principles commonly used for indirect HVDC measurements, a ammeter in series with a resistive converting device, b voltage measurement across the LV arm of a resistive voltage divider
Example Consider the HV column of a 100 kV voltage divider having a total resistance of 10 MΩ, which is composed of 100 low-voltage resistors in series, each rated 100 kΩ and 1 kV. Applying a DC voltage of 100 kV, the current through the resistive converting device would attain 10 mA, so that the power dissipating in the HV divider column approaches 1,000 W. This leads not only to an increase of the operation temperature, which might change the divider ratio, but could also damage the HV arm. This is the reason why the current through the HV arm should be kept as low as possible, but not lower than 0.5 mA to prevent an impact of dust and pollution on the divider ratio, as mentioned above. Under this condition the voltage drop across each LV resistor forming the HV arm attains 0.5 kV, which is equivalent to a specific value of 1 MΩ/kV.
This example underlines that a divider current in the order of about 0.5 mA seems to be a reasonable choice, because from a thermal point of view the current should be as low as possible. However, a current below 0.5 mA would lead to an impact of parasite leakage currents on the measuring uncertainty, as mentioned above.

Photograph of a high-precise DC voltage divider designed by Peier and Greatsch (rated voltage 300 kV, HV resistance 600 MΩ, total high 2.1 m)
In this context it should be mentioned that the above described resistive voltage divider, which is utilized by the German National Institute of Metrology (PTB Braunschweig) for high-precise reference measurements, is not applicable for DC voltage measurements in industrial test fields. This is because an unexpected breakdown of the test object is associated with fast changing over-voltages on account of the comparatively high self-inductance of the in series connected wire-wounded resistors. This causes a strong non-linear voltage distribution and would thus damage the HV arm. To enhance the energy capability, in principle metal-oxide film or carbon composition resistors could be used as alternative. However, the main obstacle is their comparatively high temperature coefficient, which would increase the measuring uncertainty, particularly under extended test duration causing a temperature rise in the HV arm. Even if this effect could be minimized by means of an artificial ageing, which is accomplished by a long-term temperature treatment, it has to be taken into account that such a conditioning is extremely time-consuming, which is thus applied only in very specific cases.

DC generator and a resistive–capacitive divider (2 MV, 1 mA) designed for the measurement of static and dynamic voltages
To measure the output voltage of HVDC dividers, in principle classical analogue instruments indicating the arithmetic mean value can be employed. However, the better approach is the use of oscilloscopes or even digital recorders to measure DC voltages under real test condition, i.e. besides the static DC voltage also typical dynamic voltages, such as the ripple and the voltage drop as well as the parameters characterizing the polarity reversal . The requirements for approved DC voltage measuring systems are specified in IEC 60060-2:2010. So, the arithmetic mean value shall be measured with an expanded uncertainty UM ≤ 3%, which corresponds to a coverage probability of 95%. To determine the dynamic behaviour of the measuring system, it is subjected to a sinusoidal voltage at the input. Changing the frequency between 0.5 and 7 times of the fundamental ripple frequency fr, the difference of the measured output voltage magnitude shall be within 3 dB.
The above-given uncertainty limits shall not be exceeded in the presence of the maximum ripple specified in IEC 60060-1:2010. The ripple magnitude shall be measured with an expanded uncertainty ≤1% of the arithmetic mean value of the DC test voltage or ≤10% of the ripple magnitude, whichever is greater (IEC 60060-2: 2010). To measure the mean value of the DC voltage and the ripple magnitude, either separate measuring systems or the same converting device in connection with two separate measuring modes for both DC and AC voltages may be used.
The scale factor of the ripple measuring system shall be determined at the fundamental ripple frequency fr with an expanded uncertainty ≤3%. The scale factor may also be determined as the product of the scale factors of the various components. Measuring the amplitude/frequency response of the ripple measuring system in a frequency range between 0.5 and 5 fr; the amplitude shall not be lower than 85% of that value occurring at the fundamental ripple frequency fr.
To measure rising and falling DC test voltages as well as the ripple and the voltage shape at polarity reversal, the characteristic time constant of the DC measuring system shall be ≤0.25 s. In case of pollution tests, the time constant shall be ≤1/3 of the rise time typical for the appearing transients (voltage drop).
The results of the type and routine tests of HVDC measuring systems can be taken from the test protocol of the manufacturer, where routine test shall be performed on each component of the measuring system. Performance tests of the complete measuring system as well as performance checks must be performed under the responsibility of the user himself or by a calibration service. The performance test shall include the determination of the scale factor at the calibration as well as the dynamic behaviour for the ripple and shall be performed annually but at least every 5 years. Performance checks cover scale factor checks and should be performed at least annually or according to the stability of the measuring system; for more information on this issue see the Sects. 2.3.3 and 2.3.4.
6.5 PD Measurement at DC Test Voltages
The physics of gas discharges under direct voltage became especially of interest in the late 1930s when high DC voltage was increasingly used for physical, medical and military applications, for instance, to generate the operation voltage of X-ray equipment, cathode-ray tubes, electron-accelerators, image intensifiers, and radar facilities. At that time numerous technical papers and text-books have been published, mainly addressed to the fundamentals of discharges in various gases and even in vacuum (Trichel 1938; Loeb 1939; Raether 1939). An excellent survey on this subject can also be found in the textbook of Meek and Craggs (1978). In the 1960s, when the first long-distance HVDC transmission lines were put into operation, the measurement of partial discharges became also of interest, in particular to assess the insulation integrity of HVDC equipment after manufacturing, such as power cables and power capacitors (Rogers and Skipper 1960; Salvage 1962; Renne et al. 1963; Melville et al. 1965; Salvage and Sam 1967; Kutschinski 1968; Kind and Shihab 1969; Müller 1976; Densley 1979; Meek and Craggs 1978; Devins 1984).

Trichel pulses recorded for a point-to-plane air gap at test level close to the inception voltage, a under 50 Hz alternating voltage, b under direct voltage c shape of a single current pulse
To assess the insulation condition of HV apparatus and their components, however, the mechanism of internal discharges, such as cavity, interfacial and surface discharges, is especially of interest. To explain the PD occurrence as well as the charge transfer due to cavity discharges under direct voltage, the classical a-b-c model illustrated in Fig. 4.13 (see Sect. 4.2) has been modified accordingly (Fromm 1995). So the three characteristic capacitances were bridged by high-ohmic resistances to simulate the voltage distribution between the electrodes under constant DC stress as well as to assess the time elapsing between consecutive discharges, which is commonly referred to as recovery time , and dominated by the time constant deduced from the intuitively assumed cavity capacitance and the resistivity of the dielectric material (Fromm 1995; Beyer 2002; Morshuis and Smit 2005).

Basic stages typical for cavity discharges under DC stress
Stage I: Initializing the ionization processes
Rising the applied DC voltage very slowly, the potential distribution between the electrodes, and in particular the field strength in the gaseous cavity, is governed by the resistive elements shown in Fig. 6.26a. To assess the inception voltage, however, seems to be impossible due to the fact that the volume and surface resistivity of solid dielectrics decreases dramatically at increasing field strength and is furthermore strongly affected by the temperature.
Stage II: Establishment of the dipole moment
Assuming that a self-sustaining discharge ignites at static inception voltage, the number of electrons released from neutral gas molecules equals always that number of positive ions, as discussed in Sect. 4.2. As a result, a dipole moment is established because all positive ions are deposited at the cathode-side cavity wall, while the electrons and negative ions (formed by the attachment of electrons to neutral molecules) are deposited at the anode-side cavity wall. As the dipole moment opposes the electrostatic field resulting from the applied DC test voltage, the field strength inside the gaseous inclusion is diminished, so that the self-sustaining discharge processes will be quenched suddenly.
Stage III: Dissipation of the dipole moment
Example Consider a discharge in a gaseous inclusion embedded in the XLPE insulation of an extruded power cable. Assuming a field strength of Ep = 20 kV/mm, which appears in the XLPE insulation adjacent to the cavity, and a conductivity of the solid dielectric of
, the density of the current, which is exclusively carried by the electrons, would attain
. Provided, a single PD event leads to the ionization of ng = 108 gas molecules, a positive space charge of
would be deposited at the cathode-side dielectric boundary. This charge will slowly be neutralized by the electrons de-trapped from the solid dielectric adjacent to the cavity. Assuming this occurs over an area of Ac = 1 mm2, the electron current crossing the dielectric boundary and neutralizing the positive space charge could be assessed by
. Based on this the time span required to neutralize the positive space charge deposited at the cathode-side dielectric boundary gets
.
Considering now the negative space charge deposited at the anode-side dielectric boundaries, the current caused by the electrons when leaving the gaseous cavity can also be assessed as close to 0.2 pA, because this continues through the solid dielectric, i.e. from the anode-side dielectric boundary to the anode. Consequently, all electrons (including those attached to neutral gas molecules and thus forming negative ions) will leave the cavity within a time span of about 80 s. With other words: the initial space charge free field conditions will be accomplished after a relaxation time of about 80 s.
- (i)
The pulse charge qi of a single PD event appearing at instant ti.
- (ii)
The recovery time ∆ti, which is inversely proportional to the PD pulse repetition rate.

Trains of charge pulses (CH1—pink trace) and accumulated pulse charge (CH2-green trace) recorded at direct voltage for discharges in a gaseous inclusion embedded in a PE cable sample, a recording time 20 s, test level slightly above PD inception voltage, b recording time 100 s, test level approx. 20% above PD inception voltage

Graphs recommended in the Amendment to IEC 60270 to display PD tests results under constant DC voltage level, a consecutive charge pulses appearing during a 30 min test period, b associated accumulated pulse charge

Graphs recommended in the Amendment to IEC 60270:2000 for a statistical analysis of the PD data. a Count of PD pulses exceeding the pulse charges 0, 1, 2, 3, 4 and 5 nC. b Count of PD pulses, occurring within the pulse charge classes (0–1) nC, (1–2) nC, (2–3) nC, (3–4) nC and (4–5) nC
Accumulated apparent charge qa
PD pulse count m
total number of PD pulses, which exceed a specified threshold level within a specified time interval ∆ti.
Moreover it is recommended in the above mentioned Amendment to present the measured PD test results graphically, as exemplarily shown in the Figs. 6.28 and 6.29.